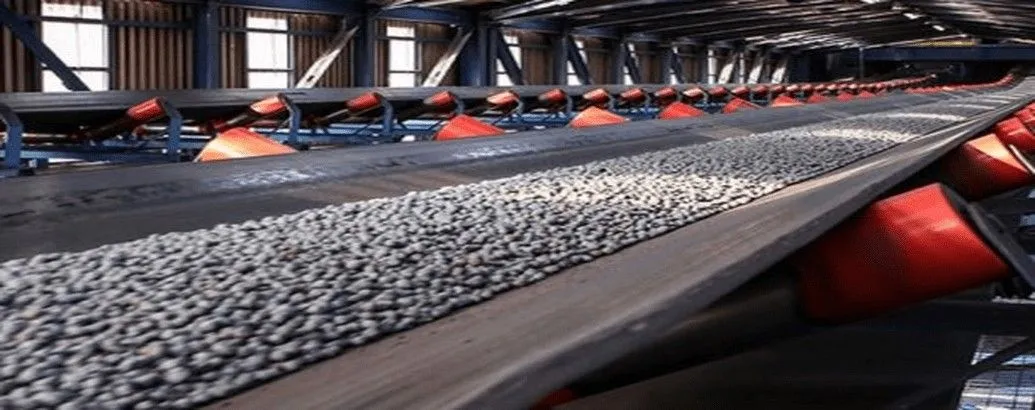
تولید آهن اسفنجی به روش احیا مستقیم
با پیشرفت صنعت فولاد، نیاز به روشهای مدرن و بهینه در تولید آهن بیش از گذشته احساس میشود. یکی از فناوریهای پیشرفته در این زمینه، روش احیای مستقیم است که به عنوان جایگزینی مؤثر برای کوره بلند مطرح شده است. این فناوری با حذف فرآیندهای پرهزینهای مانند ککسازی و سینترینگ، نهتنها هزینههای تولید را کاهش میدهد، بلکه اثرات زیستمحیطی را نیز به حداقل میرساند. آهن اسفنجی تولیدشده از این روش، به دلیل سرمایهگذاری کم و بهرهوری بالا، انتخابی مناسب برای واحدهای کوچک فولادسازی محسوب میشود. در این مقاله، به بررسی فرآیند احیای مستقیم، انواع آن و مزایای این روش خواهیم پرداخت.
احیای مستقیم چیست؟
یکی از تکنولوژی های تولید فولاد روش احیای مستقیم است. در این روش گاز طبیعی عامل احیای سنگ معدن آهن است و در کشورهایی با منابع غنی گاز طبیعی مانند ایران مورد توجه است. سهم فولاد خام تولیدی از این روش در دنیا در حدود ٧ % است. احیای مستقیم یک متد جدید تولید آهن خالص با عیار بالا است. سنگ آهن مورداستفاده در صنایع دارای اکسیدهای مختلفی است که این اکسید و ناخالصیها با کمک فرآیندهای شیمیایی از بین میروند. احیای مستقیم نیز یکی از فرآیندهای نوین تولید آهن خالص است که طی آن، آهن با عیاری بالاتر از ۹۰ درصد به دست میآید. در طی فرآیندهای آن، مواد معدنی حد واسطی نظیر هماتیت، مگنتیت و وستیت به وجود میآیند که این مواد به یکدیگر بدل شده و درنتیجه به آهن خالص تبدیل میشوند. بنابراین، تولیدکنندگان عصر ما جهت تولید آهن با عیار بالا از روش احیای مستقیم استفاده میکنند.
مراحل احیای مستقیم فولاد
احیای مستقیم فولاد طی چهار مرحله زیر انجام میگیرد:
- گندله سازی
گندله با اسامی مختلفی نظیر کنسانتره یا سنگ آهن خردشده هم شناخته میشود. برای تولید گندله ابتدا باید سنگ معدن را در معرض حرارت قرار داد. درواقع، سنگهای خام بزرگ مشکلات زیادی را در زمان جابهجایی در فازهای بعدی ایجاد میکنند؛ به همین دلیل، سنگها ابتدا کوچک میشوند تا فرآیندهای مختلف را راحتتر بتوان بر روی آنها انجام داد. گندلههای تولیدی شبیه گویهای متخلخل هستند و تقریبا سایز مشابهی دارند و بعد از عبور کنسانتره از دیسکها تغییر شکل میدهند. قطر آنها نیز از ۸ تا ۱۶ میلیمتر متغیر است و نهایتا، بعد از سرد و خشک شدن وارد مرحله بعدی میشوند.
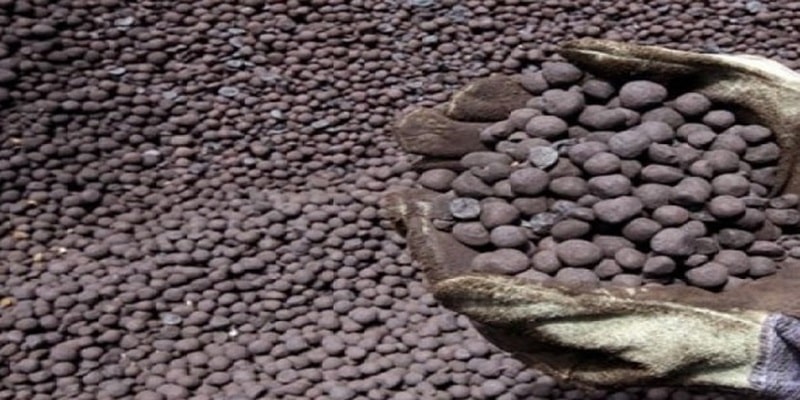
- احیای مستقیم
مرحله احیای مستقیم با یکی از روشهای MIDREX و HYL انجام میگیرد. در کشور ما از روش میدرکس جهت احیای مستقیم فولاد استفاده میکنند و بیشتر رواج دارد. در این متد، مونواکسیدکربن و گاز طبیعی با دمای بالا وارد مخزن گندلهها میشوند. در اینجا اتفاقی که میافتد، واکنش هیدروژن موجود در متان با اکسیژن است که با آزادسازی بخار آب، آهن با عیار بالاتر، تا حد امکان خالص میشود. این آهن همان آهن اسفنجی است که با مواد فلزی جهت استفاده در کورههای ذوب و تولید فولاد مورداستفاده تولیدکنندگان قرار میگیرد و از مواد مهم صنعت فولاد به شمار میآید.کارخانه فولاد مبارکه اصفهان یکی از کارخانههایی است که فرایند احیای مستقیم و تولید گندله را انجام میدهد و میتوانید با مراجعه به صفحه این کارخانه به صورت جامع و کامل با آن آشنا شوید.
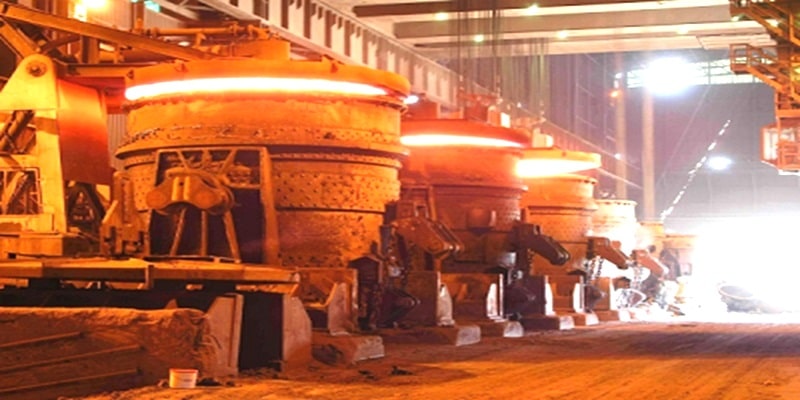
- کوره ذوب
کوره ذوب مرحله بعدی احیای فولاد است. در این مرحله، استفاده از کورههای قوس الکتریکی و القایی رواج دارد. این کورهها در گام نخست با ضایعات آهن شارژ میشوند و بعد، آهن اسفنجی حاصلشده در مرحله قبل به ضایعات مذاب آن افزوده میشود. همچنین، در زمان اضافه کردن آهن اسفنجی به کوره ذوب بایستی به نسبت آن توجه داشته باشید. نسبت آهن اسفنجی به قراضههای کورهها ۳ به ۱ است. در آخر پروسه ذوب، فولاد مذاب به دست آمده را وارد پاتیلها میکنند. تمام فرآیندها و پروسههای تولید باید با حساسیت زیادی انجام بگیرند تا محصول نهایی از کیفیت لازم برخوردار باشد.
- ریخته گری مداوم
در مرحله ریختهگری مداوم, فولاد ذوبشده بعد از تجزیه شیمیایی از پاتیلها به قالبهای شمش فولاد منتقل میشود. برای افت دمای قالبها نیز از آب استفاده میکنند؛ جریان آب با خنکسازی دیوارههای قالب دمای آن را به تدریج کاهش میدهد. پروسه کاهش دما، پوسته نازکی را در اطراف شمش به حالت جامد در میآورد. درواقع، این هدایت آب بر روی فولاد موجود در قالبها دمای آن را تا حد زیادی کم میکند و آن را به شکل جامد در میآورد. محصول نهایی، شمشهای فولادی مقاوم هستند که با کمک آنها میتوان مهمترین پروفیلهای فولادی موردنیاز صنایع را ساخت.
فرآیند احیای مستقیم آهن و فولاد
احیای مستقیم آهن و فولاد با چندین فرآیند امکانپذیر است که در قسمت زیر به رایجترین آنها اشاره کردهایم:
- روش MIDREX
روش میدرکس یکی از بهترین روشهای احیای مستقیم آهن و فولاد است که بر مبنای احیاکننده گازی صورت میگیرد. در این روش، گاز طبیعی دارای دمای بالا از پایین کوره داخل میشود و بعد از احیای آهن، مجدد از قسمت بالای کوره خارج میشود. جالب است بدانید، حدود ۶۰ درصد آهن اسفنجی موجود در بازار با این روش احیای مستقیم تولید شدهاند. از مزایای آن نیز میتوان به راندمان بالا و یکنواختی محصول ازنظر ترکیبات شیمیایی اشاره کرد.
- روش HYL
روش اچ وای ال یکی دیگر از روشهای احیای مستقیم آهن و فولاد است که تولیدکنندگان کشور ما علاقهای به استفاده از آن ندارند. این روش توسط کشور مکزیک ابداع شده است و اولین بار در قالب یک سیستم ۷۵ هزار تنی اجرایی شد. روال کار HYL بدین شکل است که گاز طبیعی تبدیل به بخار آب شده و از گاز احیاکننده به دست آمده در راکتورها استفاده میکنند. این روش احیا به دلیل عدم استقبال تولیدکنندگان با فرآیندهای دیگری جایگزین شده است.
تولید آهن اسفنجی به روش احیای مستقیم
آهن اسفنجی طی پروسه اکسایش و کاهش آهن به دست میآید؛ به همین دلیل، عناصر کاهنده در روند تولید آن مورداستفاده قرار میگیرند. عنصر کربن یکی از همین عناصر کاهنده است که از زغال سنگ یا منابع گازی به دست میآید. گاز متان نیز به عنوان یکی از بهترین گازها میتواند کربن موردنیاز آن را تامین کند. زغال سنگ هم غنی از کربن است و در این زمینه کارایی دارد. بسیاری از تولیدکنندگان با قرار دادن سنگ آهن در داخل کوره و حرارت دادن آن اقدام به تولید آهن اسفنجی میکنند. نهایتا، محصول بعد از خنکسازی وارد مرحله اندارهگیری و ارسال میشود.