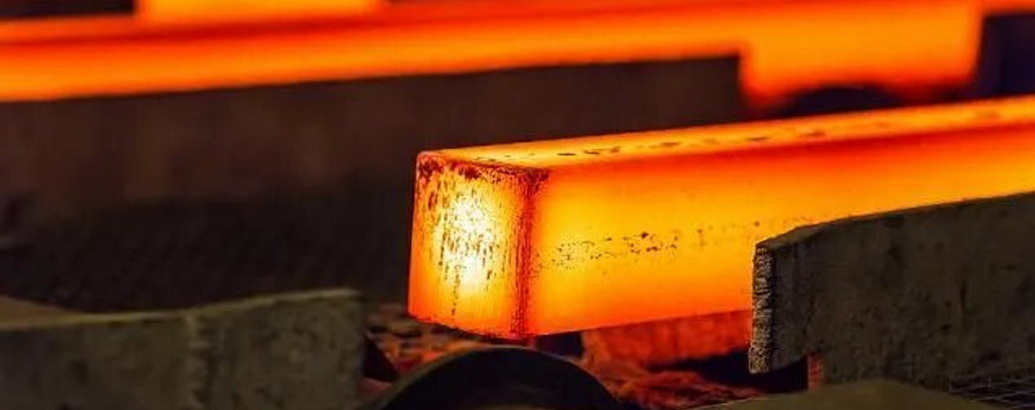
نورد گرم چیست؟ بررسی فرآیند تابکاری نورد گرم
یکی از رایجترین انواع نورد، نورد گرم است که یک فرایند اساسی در فلزکاری محسوب میشود و شامل تغییر شکل یا شکلدهی فلزات است. این کار، با رساندن دمای فلز به حرارت لازم برای تبلور مجدد آن و همچنین قالبگیری و شکل دادن فلز به فرمهای گوناگون رخ میدهد. در فرآیند نورد گرم از ماشین آلات تخصصی همچون دستگاه نورد استفاده میشود که شامل غلتکهای دواری جهت اعمال نیروهای فشاری بر فلز است و موجب تغییر شکل آن میگردد. این فرآیند با ویژگیهای منحصربهفرد خود در تولید مقاطع بزرگ و قطعات پیچیده، به یک تکنیک ضروری در صنایع مختلف از جمله ساخت و ساز و خودروسازی بدل شده است. در ادامه این مطلب به شرح جزئیاتی در رابطه با فرآیند نورد گرم میپردازیم.
نورد گرم چیست؟
در عملیات نورد گرم، فلز را از میان دو غلتک که فاصله بین آنها اندکی کمتر از ضخامت فلز ورودی و خلاف جهت یکدیگر چرخانده میشوند، عبور میدهند. در ادامه به علت بیشتر بودن سرعت چرخش غلتکها از ریلی که سطح فلز بر روی آن قرار دارد، اصطکاک میان فلز غلتک منجر به جلو راندن فلز شده و بدین ترتیب، طول آن را افزایش و ضخامتش را کم خواهد کرد.
میزان کم شدن ضخامت در طی فرآیند نورد در نوع گرم، بستگی به میزان اصطکاک بین غلتک و سطح فلز دارد؛ بهگونهای که برای تغییر شکل زیاد غلتکها بهجای حرکت ماده، بر روی آن میلغزند.
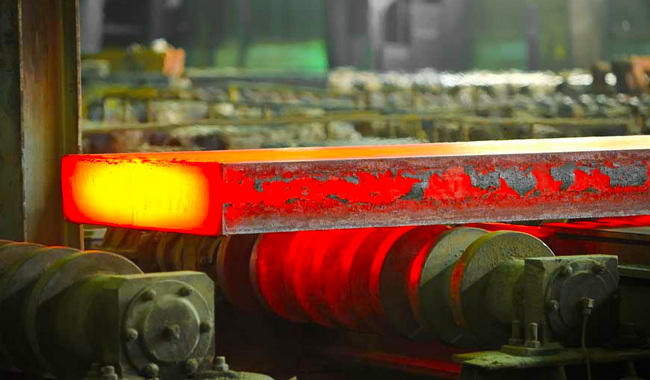
مراحل نورد گرم
نورد گرم دارای مراحل متعددی است که موجب تبدیل بیلت یا شمس به ورقها یا دیگر مقاطع فولادی میشود. در ادامه به شرح مختصری از مراحل نورد گرم خواهیم پرداخت.
آماده سازی مواد
در این مرحله، مواد فلزی مورد نیاز را انتخاب میکنند. از جمله این مواد میتوان به فولاد، مس یا آلومینیوم که اغلب بهصورت بلیتها یا شمشهای بزرگ تهیه شده و آماده حرارت دادن هستند، اشاره داشت.
گرم کردن و آمادهسازی مواد
در این مرحله، بیلتها یا شمشهای فولادی انتخاب شده در کورهای تحت عنوان کوره پیش گرم کن به دمای بالاتر از نقطه تبلور مجدد رسیده و انعطافپذیری مطلوبی را دریافت میکنند.
پوسته زدایی
در این مرحله، پوستهزدا به اشکال گوناگون به برداشتن پوستههای ایجاد شده بر روی فلز میپردازد. برداشت موثر پوستهها در طی فرآیند نورد گرم، از اهمیت بسیار زیادی برای دستیابی به کیفیت بالای فولاد برخوردار خواهد بود.
انجام عملیات نورد
برای نورد کردن شمش یا بیلتهای پوستهزدایی شده، از استند نورد استفاده میشود؛ بدین صورت که شمش یا بیلت گرم شده از میان غلتکهایی که فاصله آنها کمتر از قطر فلز است، عبور داده میشود. حرکت در میان غلتکها منجر به تغییر شکل و کم شدن ضخامت فلز شده و محصول را برای مراحل پایانی آماده میسازد.
ضخامت سنجی، تاب گیری و خنک کاری
پس از نورد شدن فلز، آن را بهوسیله دستگاه ضخامت سنج اندازه میگیرند و از طریق دستگاه تابگیر، احتمال تاب داشتن آن را از بین خواهند برد. پس از آن، قطعه را وارد خط خنک سازی میکنند و با روشهای گوناگون، اقدام به خنک کردن آن خواهند کرد.
پس از اتمام عملیات نورد، محصول نهایی در اندازههای دلخواه برش خورده و به شکل اتوماتیک رول میشود. گفتنی است که ورقهای تولید شده در این مرحله، همان ورقهای سیاه هستند که برای تبدیل شدن به ورقهای سبکتر میبایستی فرآیند نورد سرد را بر روی آنها اعمال کرد.
دستگاه و تجهیزات نورد گرم چیست؟
یکی از دستگاهها و تجهیزات منحصربهفرد و کاربردی که در کارخانههای آهن و فولاد از آن برای شکلدهی فلزات استفاده میشود، دستگاه نورد گرم است. از این دستگاه برای تولید تختال از شمشهای فولادی استفاده میگردد. نحوه کار با این دستگاه بدین گونه است که در ابتدا شمشها وارد کورههایی میشوند که دمایشان تا ۱۱۰۰ درجه سانتیگراد رسیده است. برای انجام این کار، شمشها را توسط یک جک هیدرولیکی در ردیفهای مشخصی به درون کورهها هدایت کرده و زمانی که شمشها درون کوره قرار گرفتند، بهوسیله جریانات گرد آبی در دمای ۱۱۰۰ درجه سانتیگراد برای نورد آماده خواهند شد.
انواع محصولات همچون تیرآهن و نبشی بهوسیله این دستگاهها طراحی و تولید میشوند و اهمیت ویژهای دارند. از دستگاه نورد گرم به شکل بسیار گسترده برای گرم کاری بسیاری از فلزات و آلیاژها در اندازههای متنوع استفاده میگردد. نورد به کمک دستگاه نورد گرم، قابلیت تغییر شکل بالایی را دریافت خواهد کرد. با توجه به اینکه در اثر تبلور مجدد، استحکام تسلیم به میزان قابل توجهی کاهش پیدا میکند، لذا نیروی لازم برای فرآیند نورد قطعات بزرگ در فرآیند نورد گرم از افت محسوسی برخوردار است.
فرآیند تابکاری نورد گرم و بررسی مراحل آن
در فرآیند تابکاری، با قرار دادن فولاد سرد شده در دمایی بالاتر از تبلور مجدد، در مدت زمان مشخصی ساختار متالورژیکی و ویژگیهای مکانیکی مورد نظر در فولاد ایجاد خواهد شد. هدف اصلی این عملیات، حذف تنش و بازگردانی خاصیتهای اولیه ماده به فرآورده است. فرآیند تابکاری در کورههای پیوسته و جعبهای صورت میگیرد. در ادامه به بررسی مراحل تابکاری خواهیم پرداخت.
تابکاری کامل
در این فرآیند، فلز را در خلال یک برنامه زمانی_دمایی مشخص گرم و سرد میکنند و ساختار نهایی فرآورده، از نوع دانهبندیهای درشت و پرلیت است. در چنین شرایطی، فلز از خاصیت چکشخواری شگفتانگیزی برخوردار میگردد.
تابکاری هم دمایی
در این روش، فولاد سریعتر از حالت قبل سرد میشود. به نحوی که تغییر حالات متالورژیکی در شرایط هم دمایی انجام میگیرد. در این نوع تابکاری، ساختار پرلیت یا دانهبندی ریز ایجاد میشود.
تابکاری کروی
در فرآیند تابکاری کروی به کمک بازپخت کردن فولاد و نرمالایز کردن آن، سعی در کربید کروی کردن ساختار فولاد خواهد شد. این مدل تابکاری، بهدلیل نیاز به نگهداری طولانی فلز در دمای زیر بحرانی، زمان انجام فرآیند بیشتر از مدلهای قبلی است.
کار گرم
این روش نیز یکی دیگر از فرآیندهای حرارتی بهشمار میرود که در خلال آن، ماده در دمایی بیش از دمای تبلور مجدد فلز، تغییر شکل پلاستیکی پیدا میکند.
دمای لازم برای فرآیند نورد گرم چند است؟
در فرآیند نورد گرم، کنترل دما امری لازم و ضروری بهشمار میرود. بدین منظور، ابتدا بهتر است دمای فلز را بهصورت یکنواخت تا میزان مشخصی بالا برد. این فرآیند نیازمند نگهداشتن قطعه در حرارت معین برای مدت زمان طولانی است. چنانچه دمای قطعه یکنواخت نباشد، تغییر شکل ایجاد شده نیز غیر یکنواخت خواهد بود. بهعنوان نمونه، اگر قطعه به اندازه کافی و بهصورت همگن گرم نشود سطوح گرمتر بیرونی نسبت به سطوح داخلی که سردتر و محکمتر هستند، زودتر نورد میشوند. اگر پس از گرم کردن قطعه یا در فاصله دو نورد انجام شده فلز سرد شود، سطوح سرد شده در برابر تغییر شکل مقاومت خواهند کرد.
پس در هنگام تغییر شکل در قسمت داخلی که داغتر و ضعیفتر است، احتمال اینکه ترک و گسیختگیهای سطحی در قطعه ایجاد گردد، وجود دارد. برای فولادهای کربنی ساده و فولادهای کم آلیاژ، دمای نورد کردن معمولا در حدود ۱۲۰۰ درجه سانتیگراد در نظر گرفته میشود. گفتنی است که نورد گرم معمولا در حدود ۵۰ تا ۱۰۰ درجه سانتیگراد بالای دمای تبلور متوقف میگردد. پایان دادن عملیات نورد گرم در این دما، از سخت شدن کرنشی مقطع پیشگیری کرده و منجر به ایجاد دانههای ریز و یکنواخت میشود.
مزایا و معایب نورد گرم
نورد گرم مزایای فراوانی در تولید فولاد و سایر فلزات دارد که در ادامه به بررسی مهمترین مزایا و معایب آن میپردازیم.
- شکلپذیری
نورد گرم امکان شکلپذیری و چکشخواری فلزات را در حین نوردکاری فراهم میآورد. چرا که دماهای بالاتر، منجر به نرمتر شدن فلز شده و سبب تغییر شکل آنها به اشکال مختلف از جمله ورقها، صفحات، میله و غیره میشود.
- بهبود خواص مکانیکی
فرآیند نورد گرم میتواند سبب بهبود خواص مکانیکی فلزات شود. این موضوع به این دلیل است که دماهای بالا در فرآیند نورد گرم، سبب تبلور مجدد و رشد دانه شده و این اتفاق موجب ایجاد ریزساختارهای تصفیه شده خواهد شد. از طرفی این پالایش، خواص مکانیکی فلز از قبیل استحکام و چقرمگی را هم افزایش میدهد.
- تولید و ساخت اقتصادی
بهطور کلی، نورد گرم روش مقرون بهصرفهتری در مقایسه با نورد سرد است. دمای بالا، نیروهای مورد نیاز جهت تغییر شکل را کاهش داده و سبب نرخ تولید بالاتر در واحدهای خروجی میگردد.
در حالی که نورد گرم مزایای زیادی را ارائه میدهد، معایب و محدودیتهایی هم به همراه دارد که در ادامه به آنها اشاره کردهایم.
- عدم دقت ابعادی
نورد گرم بهدلیل دمای بالا و تغییر شکل فلز، موجب ایجاد اعوجاج میشود و دقت ابعادی پایینتری نسبت به نورد سرد دارد. این موضوع سبب شده است تا افرادی که نیاز به دقت بالا در محصول نهایی دارند، نورد سرد را هم انجام دهند.
- عیوب سطحی
همانگونه که در مراحل نورد گرم هم اشاره شد، این عملیات منجر به ایجاد رسوباتی میشود که نیاز به پوستهزدایی دارد. علاوهبر این، ممکن است سطح کار به اندازه دلخواه صاف و یکنواخت نباشد و اعوجاجهایی هم بر روی آن وجود داشته باشد که جهت رفع آنها، نیاز به فرآیندهای تکمیلی اضافی خواهد بود.
- مصرف انرژی
نورد گرم نیاز به حرارت دادن فلزات تا دماهای بسیار بالا دارد که نتیجه آن، مصرف انرژی بالا است. این مصرف انرژی بالا، اثرات زیست محیطی متعددی را بهدنبال دارد و سبب بروز مشکلاتی خواهد شد.
در چه صنایعی از نورد گرم استفاده میشود؟
از نورد گرم برای تولید لوله و پروفیلهای سنگین از جمله قوطی آهن و لوله گاز استفاده میگردد. این فرآیند کاربردهای گستردهای را در صنایع مختلف دارد که از جمله مهمترین آنها میتوان به موارد زیر اشاره کرد:
- ساخت و ساز
فولاد نورد گرم شده، یک ماده اساسی در پروژههای عمرانی بهشمار میرود که از آن برای تولید اجزای سازهای، تیرها، ستونها و صفحات سنگین استفاده میشود. این فرآیند استحکام و دوام ساختمانها، پلها و پروژههای زیربنایی را فراهم میسازد.
- صنعت خودروسازی
در صنایع خودروسازی به شکل گستردهای از فولاد نورد گرم شده برای تولید قطعاتی همچون قاب، قطعات شاسی، چرخها و قطعات موتور استفاده میکنند. استحکام و مقرون بهصرفه بودن فولاد نورد گرم، آن را تبدیل به انتخابی ایدهآل برای صنعت خودروسازی کرده است.
- کشتی سازی
صفحات فولادی نورد گرم دارای کاربردهای وسیعی در کشتیسازی هستند. از این صفحات فولادی در بدنه، عرشه و دیگر اجزای ساختاری کشتی استفاده میشود. زیرا این فرآیند، تولید صفحات ضخیم با استحکام و چقرمگی بالا را امکانپذیر خواهد کرد.
کارخانههای نورد گرم ایران کدامند؟
در کشور ما کارخانههای تولید کننده ورق سیاه، بسیار فعالانه در بازارهای داخلی و خارجی حضور پیدا کردهاند. برترین کارخانههای فولادی یا تولید کننده ورق سیاه ( نور گرم) در ایران عبارتند از:
- کارخانه فولاد مبارکه اصفهان
- کارخانه فولاد کاویان اهواز
- کارخانه فولاد اکسین خوزستان
- کارخانه فولاد گیلان
- کارخانه فولاد سمنان
- کارخانه فولاد تهران
- کارخانه فولاد مبارکه
- کارخانه فولاد خرمدشت
- کارخانه فولاد قطعات البرز
جمع بندی
فرآیند نورد گرم، سنگ بنای تولید فلزات محسوب میشود که امکان تبدیل مواد خام به طیف وسیعی از محصولات با خواص مکانیکی عالی را فراهم میکند. کاربردهای این فرآیند در صنایع مختلف غیرقابل انکار است. در انتها، لازم به ذکر است که فرآیند نورد گرم، بسیاری از نیازهای صنعتی را مرتفع میسازد.