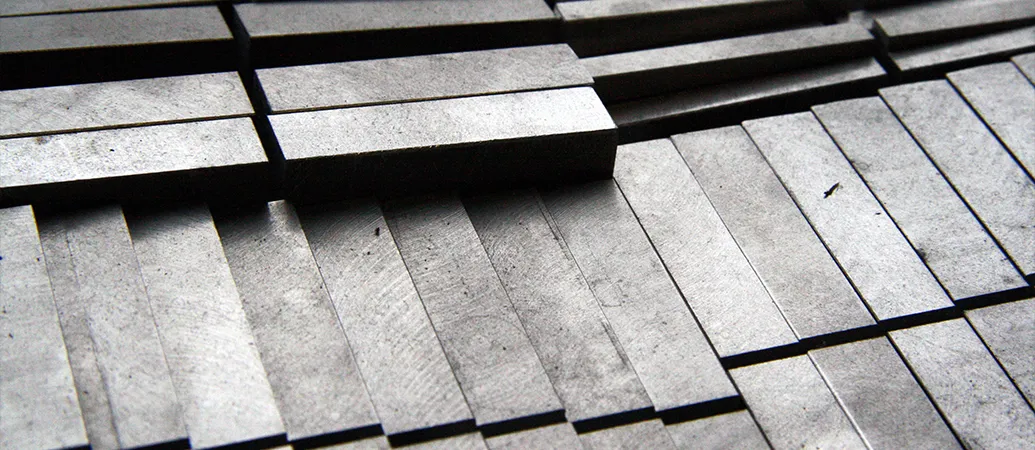
فولاد چیست و انواع آن
- فولاد چیست و تفاوت آن با آهن
- خواص فولاد
- انواع فولاد
- انواع فولاد بر اساس معیارهای مختلف
- انواع فولاد کربنی ساده
- انواع فولاد بر اساس عناصر آلیاژی
- سوپرآلیاژهای فولادی
- فولاد ابزار چیست؟
- فولادهای زنگنزن مقاوم به حرارت
- انواع فولاد پوششدار مورد استفاده در صنعت
- انواع فولاد بر اساس دیاکسیداسیون یا درجه تجزیه
- فولادهای ASTM (تقسیمبندی فولاد بر اساس استحکام فیزیکی)
- فولادهای ماریجینگ
- فولادسازی اولیه
- فولادسازی ثانویه
- ریخته گری فولاد
- شکل دهی فولاد
- تصفیه فولاد
فولاد مهمترین ماده اولیه ساختمانی و مهندسی در جهان است. کاربردهای مختلف انواع فولاد در تمامی بخشهای زندگی روزمره، از ماشینها، تولیدات ساختمانی و کشتیهای باری گرفته تا یخچال، ماشین لباسشویی و چاقوی جراحی گسترده است. این نوع مقاطع فولادی میتواند بارها و بارها، بدون از دست دادن خواص بازیافت شود و مورد استفاده قرار بگیرد. طبق آمارهای منتشرشده، میزان تولید فولاد خام جهان در سال ۲۰۱۳، ۱/۶ میلیارد تن بود، در حالی که این مقدار برای دیگر فلز مهندسی مهم در جهان یعنی آلومینیوم، ۴۷ میلیون تن ثبت شده است. تفاوت بسیار بزرگ میان این مقادیر، اهمیت نسبی انواع فولاد در صنعت جهانی را نشان میدهد. هزینههای نسبتا پایین تولید، فراوانی مواد اولیه (سنگ آهن و آهن قراضه) و گستره بینظیر خواص مکانیکی، دلایل عمده محبوبیت انواع فولاد در صنایع و کاربردهای مختلف هستند.
انواع فولاد، بر اساس معیارهای مختلف مانند ترکیب شیمیایی، کاربرد، پروسه تولید، روش ذوب، شکل ظاهری، میزان استحکام، ساختار بلوری، فرآیند جداسازی اکسیژن و عملیات حرارتی طبقهبندی میشود.
فولاد چیست و تفاوت آن با آهن
فولاد، آلیاژی از آهن و کربن است که کمتر از ۲ درصد کربن، ۱ درصد منگنز و مقدار کمی سیلیکون، فسفر، سولفور و اکسیژن دارد. اگر مقدار کربن بیشتر از ۲ درصد باشد، آلیاژ حاصل را چدن مینامند که دستهبندی، خواص و کاربردهای متفاوت دارد. قیمت این دو آلیاژ از قیمت تیرآهن کمتر است. تفاوت اصلی بین آهن و انواع فولاد، در میزان کربن موجود است که در فولاد معمولا بین ۰/۰۳ تا ۱/۰۷۵ درصد برآورد شده. فولاد ویژگیهای آهن را به بهترین شکل ممکن حفظ میکند. با این وجود افزودن کربن و عناصر فلزی و غیرفلزی دیگر به ساختار آهن، این خواص فیزیکی و شیمیایی، بهخصوص مقاومت فشاری و کششی را بهبود میبخشد. علاوه بر افزایش قابلیت شکلپذیری و مقاومت فشاری و کششی بیشتر، مقاطع فولادی فوق دارای خاصیت ضدخوردگی نیز هست، در حالی که آهن در معرض اکسیژن و آب، اکسید میشود. البته به همان میزان که استحکام این آلیاژ نسبت به آهن بالاتر است، قابلیت چکشخواری آن کمتر بوده و سختی بیشتری دارد. همچنین افزودن عناصر سیلیسیم، منگنز و کروم، مقاومت کششی فوقالعادهای به فولاد میبخشد.
خواص فولاد
مقاومت بسیار بالا، مهمترین خاصیت فولاد به حساب میآید که آن را به تاثیرگذارترین ماده صنعتی تبدیل کرده است؛ بهطورکلی، این آلیاژ در برابر کشش، سایش و خوردگی مقاومت بالایی دارد. البته مقاومت در برابر خوردگی مربوط به گریدهای فولاد ضد زنگ میشود. علاوه بر این، فولادها دارای دوام و پایداری مطلوبی در شرایط بارگذاری مختلف هستند. ضمنا، فولاد به دلیل فراوانی و در دسترس بودن منابع ساختش و همینطور هزینه مناسب آن به یک آلیاژ پرمصرف و کاربردی تبدیل شده است.
فلز پایه: آهن
آهن به عنوان یکی از عناصر فراوان در پوسته زمین شناخته میشود و فلز پایه بسیاری از محصولات است. فولادها یکی از همین محصولات هستند که ۵۰ درصد آنها با آهن تشکیل شده است. بر همین اساس، از آهن به عنوان عنصر اصلی فولاد یاد میکنند. ضمنا، در صورتی که میزان آهن موجود در آلیاژ کمتر از ۵۰ درصد باشد، دیگر به آن فولاد گفته نمیشود. بهعلاوه، اگر آلیاژی متشکل از آهن و کربن دارای کربن بیش از حد باشد، فولاد نیست و در دسته چدنها قرار میگیرد.
اثرات کربن
کربن را مهمترین عنصر فولاد میدانند؛ زیرا بیشترین تاثیر را بر ساختار آن میگذارد. بهطورکلی، فولاد حداکثر ۲ درصد کربن دارد و هرگونه تغییر در مقدار آن، تمام خصوصیات فولاد مانند مقاومت کششی، نقطه تسلیم، میزان شکنندگی، جوشپذیری و... را تحتتاثیر قرار میدهد. با افزایش میزان کربن، استحکام و سختیپذیری فولاد بیشتر و قابلیت جوشکاری، ماشینکاری و چکشخواری آن کمتر میشود. به این ترتیب، اگر مقاومت و سختی فولاد برایتان اهمیت دارد، باید درصد کربن آن را افزایش دهید.
اثرات عملیات حرارتی
عملیات حرارتی یکی از فرآیندهای مهم در صنعت فولادسازی است که با اهداف مختلفی انجام میگیرد. این عملیات به مجموعه روندهایی گفته میشود که با حرارتدهی و خنک کردن قطعات همراه است. عملیات حرارتی باعث تغییر خواص متالورژیکی قطعات میشود؛ هدف از انجام این کار، آمادهسازی قطعات برای کاربردهای متنوع است. به عبارت دیگر، خصوصیات فیزیکی، شیمیایی و متالورژیکی فولاد در طول عملیات حرارتی تغییر میکند و در نهایت، به سطح تعادل مورد نظر میرسد.
اثرات آلیاژسازی
آلیاژسازی در فولاد، خواص و ویژگیهای مختلفی را در آن ایجاد میکند؛ به صورتی که با تغییر درصد هر یک از این عناصر آلیاژی در ساختار شیمیایی فولاد، خصوصیات آن دچار تغییرات زیادی میشود. از عناصر آلیاژی که قابل افزودن به ترکیب فولاد هستند میتوان به مس، مولیبدن، منگنز، کروم، نیکل و... اشاره کرد. این عناصر آلیاژی بنا بر ماهیت خود تاثیرات زیادی بر خواص فولاد میگذارند.
انواع فولاد
انواع فولاد بر اساس معیارهای مختلف
انواع فولاد را میتوان بر اساس معیارهای مختلف مانند ترکیب شیمیایی کاربرد، پروسه تولید، روش ذوب، شکل ظاهری، میزان استحکام، ساختار بلوری، فرآیند جداسازی اکسیژن و عملیات حرارتی طبقهبندی کرد که در ادامه برخی تقسیمبندیهای مهم معرفی میشود.
بر اساس ترکیب شیمیایی:
بر اساس ساختار شیمیایی، انواع فولاد را به دو دسته بزرگ ساده کربنی و آلیاژی تقسیم میکنند. فولاد ساده کربنی، شامل کربن و مقدار کمی از عناصر معمول دیگر است، در حالی که فولاد آلیاژی از ترکیب فولاد کربنی و تعدادی از عناصر آلیاژی مانند منگنز، سیلیکون، نیکل، تیتانیوم، مس، کروم و آلومینیوم، به دست میآید. تعیین قیمت آهن و دیگر آلیاژهای فولاد، بر اساس مواد اولیه و عناصر تشکیلدهنده آنها تعیین میشود.
برای مشاهده لیست قیمت آهن و کلیه مقاطع فولادی میتوانید به لینک فوق در وبسایت آهن آنلاین مراجعه کنید.
انواع فولاد و کاربرد آنها:
- سازهای: این محصولات، جز انواع فولادهای معمولی با درجه کیفیت ۱، ۲ و ۳ بوده و در صنعت ساختمانسازی و برای ساخت اسکلت فلزی، نرده، توری، جرثقیل و ... مورد استفاده قرار میگیرند.
- فنر: فولاد فنر، مقاومت بالایی در برابر ارتعاش و سایش داشته و با وجود مقاومت کششی بالا، به دلیل داشتن سلیسیم، خاصیت آلاستیسیته بالایی نیز دارد. انواع فولاد فنر در ساخت فنرهای استوانهای، تخت و مخروطی کاربرد دارند.
- قالبی: این فولاد برای ساخت قالبهای پلاستیکزنی به کار میرود.
- ابزار: برای ساخت ابزار مناسب هستند.
- یاتاقان: در قطعاتی که تحت بار و سایش زیادی هستند و باید تنش فشاری را تحمل نمایند، از این فولاد استفاده میشود؛ مانند ساچمهها، غلتکها، مفاصل، سوزنها، یاتاقانها و...
- ضدسایش: از انواع فولاد مقاوم در برابر سایش است که در ساخت ماشینآلات پردازش سنگ، سنگشکنها و بیلهای مکانیکی به کار گرفته میشود.
- سوپاپ: برای ساخت سوپاپهای خودروها و موتورهای احتراق سبک و سنگین، سوپاپهای دود و... استفاده میشوند.
- دریایی: در کف، عرشه و بدنه کشتیها و قایقهای مختلف، زیر دریاییها، شناورها و… کاربرد دارد.
- ماشینکاری
- دیگ بخار
- مخزن تحت فشار
- آبکاری
انواع فولاد بر اساس پروسه تولید:
- نورد گرم: تحت عملیات نورد گرم تولید شده و در مواردی کاربرد دارد که دقت بالایی نیاز است.
- نورد سرد: همان فولاد نورد گرم است که فرآیند پرداخت آن طولانیتر میباشد. این تفاوت باعث افزایش کیفیت فولاد نورد سرد میشود.
- سرد کشیده شده: تحت فرآیند کشش سرد تولید شده و از کیفیت خوبی برخوردار است.
- ریختهگری: قطعاتی که با روش ریختهگری تولید شده و میزان کربن آنها بین ۰/۱۵ تا ۰/۶ درصد است
- آهنگریشده: قطعاتی که با روش آهنگری تولید شده و کیفیت بالاتری نسبت به روش ریختهگری دارند.
انواع فولاد بر اساس شکل ظاهری: به صورت شمش، میله، لوله، صفحه، ورق و... یافت میشود.
از نظر ترکیب شیمیایی
فولادها بر اساس ترکیب شیمیایی خود به یکی از گروههای فولادهای کم آلیاژ، فولادهای پر آلیاژ، فولادهای کم آلیاژ با مقاومت بالا و فولادهای کربنی تعلق دارند. فولادهای کربنی یکی از کارآمدترین فولادهای مورد استفاده در صنایع هستند که در ترکیب آنها، آهن و حداکثر ۱ درصد کربن وجود دارد. سه گروه دیگر که از مدل آلیاژی هستند، مقاومت بالاتری در مقایسه با فولادهای کربنی دارند. کاربردهای فولادهای پر آلیاژ نیز بیشتر از سایر مدلها است.
فولادهای ماشینکاری آزاد
فولادهای ماشینکاری آزاد همان فولادهای خوش تراش هستند که قابلیت ماشینکاری بسیار آسان و مناسبی دارند. با مکانیزم فولادهای خوش تراش، قابلیت ماشینکاری مواد بهبود یافته و به دنبال آن، تراشهها در زمان ماشینکاری به قطعات کوچک تقسیم و شکسته میشوند. با این قابلیت میتوان از درهمتنیدگی مواد در ماشینآلات پیشگیری کرد. ضمنا، فولادهای خوش تراش با سرب، قابلیت ماشینکاری بهتری دارند. در کل، این شرایط اجرای خودکار تجهیزات بدون دخالت انسانی را مهیا میکند.
فولادهای مقاوم در برابر سایش
فولادهای مقاوم در برابر سایش را با نام فولادهای آستنیتی منگنزدار نیز میشناسند. این فولادها از 2/1 درصد کربن و ۱۱ درصد منگنز تشکیل شدهاند. فولادهای این گروه توسط رابرت هادفیلد در سال ۱۸۸۲ کشف شدند. در کل، این فولادهای ضد سایش، به دلیل مقاومت بالایی که در برابر ساییدگی و خراشیدگی دارند به یکی از فولادهای پرکاربرد صنعتی تبدیل شدهاند. ساخت آنها نیز تحت گریدهای مختلفی انجام میگیرد؛ از گریدهای فولاد مقاوم به سایش میتوان به A، B1، C، D و E1 اشاره کرد.
فولادهای بلبرینگ
فولاد بلبرینگ (Ball Bearing Steel) یکی دیگر از انواع فولاد است که در تولید بلبرینگها مورد استفاده قرار میگیرد. فولادهای این گروه به دلیل نوع کاربردشان باید از استحکام و مقاومت بالایی در برابر فشار و فرسایش برخوردار باشند و حد خستگی (Fatigue) آنها نیز بالا باشد. درواقع، بلبرینگها نوعی عناصر ماشینی هستند که دقت بالایی داشته و حرکت نسبی میان اجزای ماشین را با کمترین اصطکاک ممکن فراهم میکنند.
فولادهای ضد زنگ
فولادهای ضد زنگ، دستهای از فولادها هستند که کربن کمی در ترکیب آنها وجود دارد. کروم، عنصر اصلی فولاد زنگ نزن را تشکیل میدهد که ترکیب آن با سایر عناصر باعث مقاومت فولاد در برابر زنگزدگی و خوردگی میشود. همچنین، این فولادها توانایی حفظ مقاومت خود در دمای بالا را دارند. از انواع فولادهای ضد زنگ میتوان به فولاد ضد زنگ رسوب سخت، فولاد ضد زنگ فریتی سری 400، فولاد ضد زنگ مارتنزیتی سری 400، فولاد ضد زنگ آستنیتی سری ۳۰۰ و فولاد ضد زنگ دوفازی (فریتی + آستنیتی) اشاره کرد.
فولادهای الکتریکی
فولادهای الکتریکی یا همان فولادهای سیلیکونی دارای عنصر سیلیسیم هستند. وجود سیلیسیم در ترکیب این فولادها باعث افزایش خواص مغناطیسی آنها شده است؛ اما در عین حال منجر به سخت و ترد شدن فولاد میشود. این سخت و ترد شدن فولاد به مفهوم کاهش شکلپذیری آن است. ضمن اینکه از فولادهای مدل الکتریکی در روتورها، موتورها، ترانسفورماتورها و... استفاده میشود و آنها به نوعی مناسب وسایل و تجهیزات الکتریکی هستند.
انواع فولاد کربنی ساده
این نوع فولاد، تقریبا ۹۰ درصد از انواع فولاد تولیدی در جهان را شامل میشود و به دلیل تنوع بالا، در صنایع گوناگون مانند نفت، گاز و پتروشیمی مورد استفاده قرار میگیرد. معمولا کربنی ساده را بر اساس میزان کربن موجود، به صورت زیر دستهبندی میکنند:
- نرم: این آلیاژ کمتر از ۰/۱۵ درصد کربن داشته و برای ساخت میخ، پرچ، لوله و... مورد استفاده قرار میگیرد.
- کمکربن: میزان کربن موجود در ساختار این فولاد بین ۰/۱۵ تا ۰/۳ درصد است. پایین بودن میزان کربن در این نوع آلیاژ آهن، آن را برای جوشکاری و ماشینکاری مناسب ساخته است و خواص مغناطیسی بالایی به آن بخشیده. به دلیل آسانتر بودن فرآیند تولید فولاد کمکربن، این محصول نسبت به دیگر انواع فولاد به میزان بیشتری تولید شده و در مواردی که قطعات، تحت عملیات سختی سطحی قرار میگیرند، به کار میرود. همچنین قیمت آن نسبتا پایین است و در بیشتر قطعات مهندسی، ساختمان کشتیها و راه آهن، میتوان آن را یافت.
- کربنمتوسط: مقدار کربن موجود در آن بین ۰/۳ تا ۰/۶ درصد است. این نوع آلیاژ برای سایشهای متوسط گزینه خوبی است، ولی برای عملیات حرارتی مناسب نیست. ساخت شفت، میللنگ و فنرها، از جمله کاربردهای فولاد کربن متوسط است.
- پرکربن: بیش از ۰/۶ درصد از ساختار این فولاد را کربن تشکیل داده و همین امر باعث شده تا یکی از سختترین و بادوام ترین انواع فولاد غیرآلیاژی به شمار برود. مقاومت این فولاد در برابر سایش بالا بوده، اما قابلیت جوشپذیری آن بسیار کم است. این فولاد بیشتر در مواردی به کار میرود که لازم است قطعات ریخته شده، از سختی بالایی برخوردار باشند. همچنین در ساخت انواع اره، آچار، مته، تیغه، فنر و... از آن استفاده میشود.
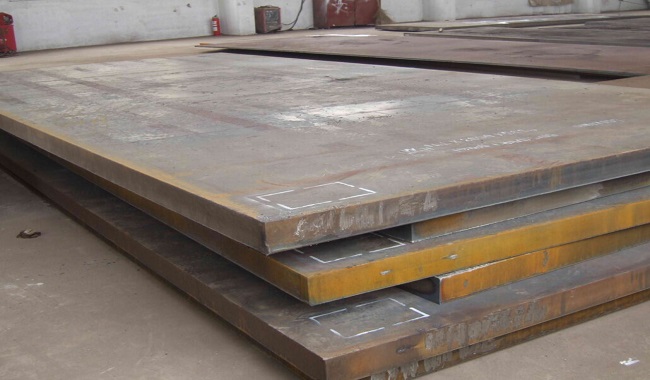
انواع فولاد بر اساس عناصر آلیاژی
عناصر آلیاژی برای افزودن خواص مشخص و در نسبتها و ترکیبهای مختلف به کربنی اضافه میشوند. این عمل باعث ایجاد تغییراتی مانند افزایش سختی، مقاومت به خوردگی، استحکام و شکلپذیری میشود. انواع آلیاژی نسبت به انواع فولاد کربنی، پذیرایی عملیات حرارتی بیشتری داشته و به دلیل خواص مکانیکی خوب، سادگی پردازش، دسترسی گسترده و... در صنعت پرکاربردند.
انواع فولادهای آلیاژی عبارتند از:
- کمآلیاژ: میزان منگنز و سیلیسیوم موجود در این فولادها نسبت به ساده بیشتر بوده و عناصر دیگری مانند وانادیم، کلمبیم و تیتانیوم به آنها اضافه میشود. به طور کلی میزان عناصر آلیاژی در این فولاد، حدود ۰/۴ درصد است.
- پرآلیاژ: دارای حدود ۰/۸ درصد عناصر آلیاژی باشند، فولاد پرآلیاژ نامیده میشوند.
تعداد دیگری از عناصر مورد استفاده در تولید انواع فولاد آلیاژی، عبارتند از: - مولیبدن: باعث افزایش چقرمگی و مقاومت کششی میشود.
- تنگستن: میزان برندگی و مقاومت گرمایی فولاد را بالا میبرد.
- ترکیب نیکل و کروم: نیروی کششی فولاد را افزایش میدهد.
- کبالت: در ترکیب فولاد مورداستفاده در ابزارهای برش به کار رفته و سختی گرم را بهبود میبخشد.
- منگنز: مقاومت سطحی را افزایش داده و قابلیت کششی، چکشخواری و شوکپذیری را بیشتر میکند.
- وانادیوم: استحکام و مقاومت در برابر خوردگی و ضربه را افزایش میدهد.
- ترکیب کروم و وانادیوم: مقاومت کششی را به طور موثری بیشتر میکند. فولاد حاصله مستحکم است، اما خم کردن و بریدن آن آسان است.
همچنین متداولترین انواع فولادهای آلیاژی شامل دستههای زیر هستند:
- دسته 4140: کروم-مولیبدن
- دسته 4340: نیکل-کروم-مولیبدن
- دسته 6150: کروم-وانادیوم
- دسته 8620: HSLA (کمآلیاژ پراستحکام نیکل-کروم-مولیبدن)
به انواع فولاد تولیدشده با مقدار عناصر آلیاژی بیش از ۵۰ درصد، فولاد سوپرآلیاژی گفته میشود. استحکام مکانیکی و مقاومت در برابر خزش، در این فولاد بسیار بالا بوده و در راکتورهای هستهای و توربینهای غولپیکر صنعتی، به کار گرفته میشوند.
سوپرآلیاژهای فولادی
سوپرآلیاژ پایه نیکل: ترکیب شیمیایی آن شامل کروم (۱۰ تا ۲۰ درصد)، تیتانیوم، آلومینیوم (بیش از ۸ درصد) و کبالت (۵ تا ۱۰ درصد) است. همچنین مقادیر کمی از بور، زیرکونیوم و کربن نیز برای ایجاد پایداری حرارتی بیشتر استفاده میشوند. In738 معروفترین دسته سوپرآلومینیومهای پایه نیکل است که کاربرد گستردهای در ساخت پرههای توربین دارد.
سوپرآلیاژ پایه آهن: مهمترین ویژگی این سوپرآلیاژها، مقاومت حرارتی بسیار بالاست، به طوری که افزایش چشمگیر درجه حرارت نیز تاثیری در دمای آنها ندارد. استفاده از آهن در کاربردهای سوپرآلیاژی اهمیت زیادی دارد ، چون سوپر آلیاژهای مبتنی بر آهن، علیرقم مقاومت سایشی و مقاومت در برابر اکسیداسیون بالا، قیمت نسبی کمتری دارند.
سوپرآلیاژ پایه کبالت: نقطه ذوب آنها از سوپر آلیاژهای پایه نیکل بالاتر بوده و مقاومت حرارتی، اکسیداسیون و مقاومت سایشی بیشتری دارند. مقاومت به شکست خستگی بالا و قابلیت جوشکاری مناسب نیز از دیگر ویژگیهای این سوپرآلیاژها به شمار میرود.
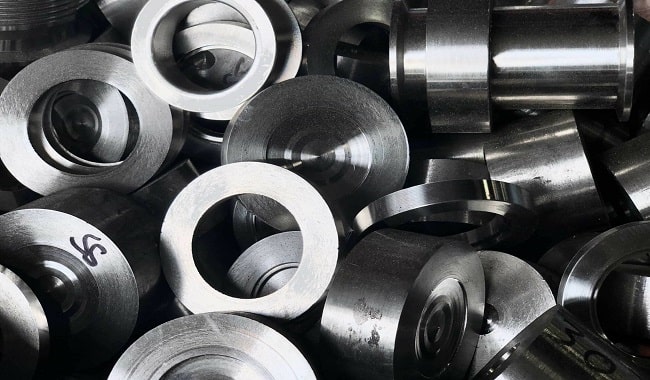
فولاد ابزار چیست؟
این فولادها دو نوع دارند: فولاد ابزار سردکار که برای ساخت ابزار دستی یا ماشینی به کار میرود و فولاد ابزار گرمکار که برای شکل دادن یا برش دادن مواد در دماهای بالا استفاده میشود و تفاوت آن با نوع سردکار، در میزان مقاومت حرارتی آنها میباشد. فولادهای کربنی و آلیاژی استفاده شده به این منظور، باید با توجه به کاربرد ابزار موردنظر انتخاب شده و خواصی مانند سختیپذیری، مقاومت سایشی، درجه حساسیت در برابر انقباض و مقاومت در برابر درجه حرارت بازپخت را دارا باشند. برای تامین این خواص، از فولادهای شامل تنگستن، مولیبدن، کبالت و وانادیم استفاده میکنند.
ساخت فولاد ابزار با استفاده از کورههای قوس الکتریکی امروزه متداولتر است. این آلیاژ آهنی عموما در شرایطی به کار میرود که عملیات حرارتی، سختی را افزایش میدهد. به دلیل احتمال ظاهر شدن تردی حرارتی در فولادهای ابزار، عملیات حرارتی باید با دقت بیشتری انجام شود. این عملیات مشابه عملیات حرارتی فولادهای ساده و کمآلیاژ است.
به طور کلی فولاد ابزار به شش گروه تقسیم میشود:
- سختکاری شده در هوا: این دسته از فولادهای ابزار بسیار متنوع بوده و در ساخت میله، قالبهای سکهزنی و لمینیت کاربرد دارند.
- سختکاری شده در روغن: این گروه از انواع پرکاربرد بوده و سختی اولیه آنها زیاد است. مصرف آنها بیشتر در ساخت میله، دستگاه برشزنی و قالبریزی سرد است.
- نوع D: این آلیاژ ابزار با کروم بالا بوده و برای ترکیب دو خاصیت مقاومت در برابر سایش و سختکاری با هوا تنظیم شده است.
- نوع S (مقاوم در برابر ضربه): این نوع، برای مقاومت در برابر ضربه در هر دماهای پایین و بالا طراحی شده و دارای چقرمگی بسیار بالا و مقاومت کم در برابر سایش است.
- نوع C (سردکاری شده): شامل سه گروه سردکاری شده در روغن، سردکاری شده در هوا و کربن و کروم بالا بوده و در ساخت قطعات بزرگتر یا قطعاتی که نیاز به تخریب کمتری در هنگام سخت شدن دارند، استفاده میشود.
- گرمکار: فولاد ابزار گرم کار، بیشتر در در ریختهگری تحت فشار، قالبهای آهنگری و اکستروژن استفاده میشود.
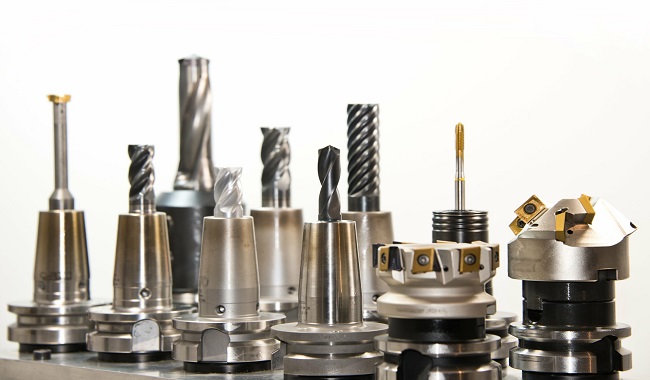
فولادهای زنگنزن مقاوم به حرارت
فولادهای زنگنزن یا همان استنلس استیل، در مقایسه با نرم، ۲۰۰ برابر مقاومت بیشتری در برابر خوردگی دارند و در عین حال، در برابر حرارت نیز مقاومت بالایی دارند. عنصر آلیاژی اصلی در این فولادها کروم بوده که حداقل مقدار آن ۱۱ درصد و معمولا بین ۲۰ تا ۳۰ درصد است. برای بهبود خواص دیگر فولادهای زنگنزن، عناصری مانند نیکل، مولیبدن، مس، تیتانیم، آلومینیوم، سیلیسیم، نیوبیوم، نیتروژن، گوگرد و سلنیم را به آنها اضافه میکنند.
فولادهای زنگنزن، شامل 5 گروه هستند:
- آستنیتی: یکی از پرکاربردترین انواع فولاد بوده و مقدار بالای نیکل موجود، باعث مقاومت و انعطاف آن شده است. این فولاد برای جوشکاری مناسب بوده و در برابر خوردگی نیز مقاوم است.
- فریتی: انواع فولادهای فریتی، در برابر ترکخوردگی ایجاد شده در اثر تنش، مقاومت خوبی دارند، ولی استحکام دمای آنها در مقایسه با فولاد زنگنزن آستنیتی کمتر است. مقدار کروم موجود در این نوع فولاد بین ۱۲ تا ۱۷ درصد و میزان کربن آن کمتر از ۰/۱ درصد است.
- مارتنزیتی: ترکیب آن شامل ۱۱ تا ۱۷ درصد کروم، ۰/۴ درصد نیکل و ۱/۲ درصد کربن است. مقاومت این نوع فولاد زنگنزن در برابر ساییدگی، باعث حفظ لبههای تیز آن شده و به همین دلیل در ساخت کارد، لوازم جراحی و... به کار میرود.
- رسوب سختشده: این فولاد مقاومت زیادی در برابر خوردگی دارد و میزان نیکل موجود در آن ۳ تا ۵ درصد و کروم ۱۵ تا ۱۷ درصد است. همچنین فلزات دیگری مانند مس، تیتانیوم و آلومینیوم نیز در ترکیب آن یافت میشوند.
- دوپلکس: نوعی آلیاژ ضدزنگ دوپلکس که حاوی ۲۲ تا ۲۵ درصد کروم، 5 درصد نیکل، مولیبدن و نیتروژن است، نسبت به نوع آستنیتی مستحکمتر بوده و مقاومت تنش ترکخوردگی بالایی نیز دارد.
انواع فولاد پوششدار مورد استفاده در صنعت
برای محافظت فلزات مختلف در برابر خوردگی و همچنین ایجاد ظاهر زیبا، سطح فلزات را پوشش میدهند. به این منظور، از روشهای زیر استفاده میشود:
- غوطهوری: فولاد را در داخل حمام مذاب روی، فرو میبرند.
- اسپری حرارتی: روی مذاب را به سطح فلز میپاشند.
- گالوانیزه کردن خشک: فلز را در معرض بخار روی قرار میدهند.
- گالوانیزه کردن الکترولیتی: الکترولیز ورق فولادی
علاوه بر محافظت در برابر خوردگی، ترکیب آهن و روی باعث افزایش خواص رنگپذیری و جوشپذیری نیز میشود. طول عمر فولادهای روکشدار، به شرایط محیطی و ضخامت روی استفاده شده وابسته است. علاوه بر روی، از مواد دیگری نیز به منظور حفاظت در برابر عوامل خورنده استفاده میشود.
ورق گالوانیزه، ورق آلوزینک، ورق رنگی و ورق قلع اندود، از مهمترین ورقهای پوششدار فولادی به شمار میروند که در این میان ورق گالوانیزه متداولتر بوده و در صنایع مختلفی استفاده میشود. بیشترین کاربرد ورق گالوانیزه در ساخت کانال کولر، کابینت آشپزخانه ، شیروانی و لولههای بخاری است. ورق آلوزینک از ترکیب آلومینیوم و روی ساخته شده و در ساخت روکش دیوار، زه کشی و لولهکشی، نردهها، قاب خانههای فولادی و... کاربرد دارد. ورق رنگی از جمله ورقهای پایه گالوانیزه است که رنگآمیزی آن به صورت کورهای انجام شده و در صنایع ساختمانی و لوازم خانگی استفاده میشود. ورق قلعاندود یا همان حلبی، به طور گستردهای در ساخت قوطیهای کنسرو کاربرد دارد.
انواع فولاد بر اساس دیاکسیداسیون یا درجه تجزیه
فولاد مذاب به دست آمده از کورههای فولادسازی، مقادیر زیادی اکسیژن محلول دارد که باید قبل از ریختهگری حذف شود. عملیات حذف اکسیژن از فولاد را آرامسازی (killing) مینامند. برا این اساس، سه نوع فولاد وجود دارد:
- آرام (killed): فولادی است که اکسیژن آن به طور کامل حذف شده و خواص همگنی دارد، از این رو برای کربوره کردن یا آهنگری مناسب است.
- نیمهآرام (semi-killed): نسبت به آرام، اکسیژن زدای کمتری به آن اضافه میشود.
- جوشان (rimmed steel): در این آلیاژ، فرآیند اکسیژنزدایی انجام نشده و اکسیژن با کربن واکنش نشان داده و باعث ایجاد تخلخل (حفره گازی) میشود. ترکیب شیمیایی این نوع فولاد، تغییرات زیادی داشته و پوسته خارجی آنها شامل آهن خالص، کربن اندک، فسفر و گوگرد است.
- سردار (capped steel): بین فولادهای نیمهآرام و ناآرام قرار داشته و برای تولید ورق، نوار، سیم و… با کربن بیش از ۰/۱۵ درصد استفاده میشود.
انواع فولاد ازنظر شکل و سطح مقطع
فولادها از نظر شکل و سطح مقطع به دو دسته محصولات تخت و محصولات بلند تقسیم میشوند. فولادهای تخت همانطور که از نامشان پیداست، سطح مقطع تختی دارند. از انواع فولادهای تخت میتوان به ورق، تسمه و کویل تولید نورد سرد و... اشاره کرد. فولادهای بلند یا طولی نیز شامل میلهها، میلگردها، تیرآهنها، نبشیها، سپریها، مفتولها و... میشوند. این فولادهای تخت و بلند دارای استانداردهای مشخصی هستند و اندازه آنها بر همین مبنا تعیین میشود.
فولادهای ASTM (تقسیمبندی فولاد بر اساس استحکام فیزیکی)
استانداردهای فولادی ASTM توسط انجمن آزمایشها و مواد آمریکا، تدوین شده و در طبقهبندی و ارزیابی ویژگیهای مکانیکی، شیمیایی، مادی و ساختاری تمام انواع فولاد قابلاستفاده هستند. در این استاندارد، حرف A بعد از عبارت ASTM به مواد آهنی اشاره دارد. سپس یک عدد ۱ تا ۳ رقمی قرار گرفته و بعد سال تصویب یا ویرایش استاندارد نوشته میشود.
برخی از محصولات مهم این نوع آلیاژی با استفاده از این استاندارد در جدول زیر نمایش داده شده.
استانداردهای ASTM توسط انجمن آزمایشها و مواد آمریکا، تدوین شده و در طبقهبندی و ارزیابی ویژگیهای مکانیکی، شیمیایی، مادی و ساختاری تمام انواع فولاد قابلاستفاده هستند. در این استاندارد، حرف A بعد از عبارت ASTM به مواد آهنی اشاره دارد. سپس یک عدد ۱ تا ۳ رقمی قرار گرفته و بعد سال تصویب یا ویرایش استاندارد نوشته میشود.
برخی از محصولات مهم فولادی با استفاده از این استاندارد در جدول زیر نمایش داده شده است.
فولادهای ماریجینگ
فولادهای ماریجینگ از انواع آلیاژ آهنی به شمار میروند که میزان کربن موجود در آنها پایین و حتی گاهی صفر بوده و شامل مقدار زیادی نیکل (بین ۱۵ تا ۲۰ درصد) و همچنین عناصر کبالت، مولیبدن، تیتانیم و آلومینیوم میباشند. نام ماریجینگ از عملیات استحکامدهی این نوع فولاد گرفته شده است. علت مستحکم بودن این فولاد، با وجود مدار کمکربن، رسوب ترکیبات بین فلزی است. فولادهای ماریجینگ برای ماشینکاری مناسب بوده و قابلیت جوشپذیری خوبی نیز دارند. وجود مقادیر بالای عناصر آلیاژی باعث شده تا قابلیت سختشوندگی این فولاد افزایش بیابد. انواع فولاد غیرزنگنزن ماریجینگ نسبت به خوردگی و تردی هیدروژنی مقاوم است و این خاصیت با استفاده از ورق کاری کادمین یا فسفاته کردن آن بیشتر میشود. فولادهای ماریجینگ بر اساس میزان استحکام کششی آنها در صدها پوند در اینچ مربع، با اعداد ۲۰۰، ۲۵۰، ۳۰۰ و ۳۵۰ نامگذاری میشوند.
انواع فولادهای ماریجینگ در پوستهی راکت موشک، هوافضا، ساخت سانتریفیوژها، قطعات داخلی موتورها، قالبهای تولید، قطعات الکترومکانیکی و... مورد استفاده قرار میگیرند.
فولادسازی اولیه
فرایند تولید فولاد در کارخانه های فولادی نسبت به دهههای گذشته دستخوش تغییرات زیادی شده است. امروزه فولادسازی شامل فولادسازی اولیه و فولادسازی ثانویه میشود. فولادسازی اولیه با روشهای اکسیژن قلیایی و کوره قوس الکتریکی انجام میگیرد. در فولادسازی با اکسیژن قلیایی برای تولید فولاد از آهن چدن پرکربن استفاده میکنند. دمش اکسیژن از داخل آهن چدن، درصد کربن آلیاژی را کم کرده و موجبات تولید فولاد را فراهم میکند؛ بنابراین، این روش فولادسازی پایه اکسیژن است. همچنین این پروسه به علت طبیعت شیمیایی مواد نسوز مصرفی در آستر نسوز مخزن و همینطور، قابلیت خورنده فلز مذاب و سرباره به روش قلیایی معروف شده است.
فولادسازی قوس الکتریکی نیز یکی دیگر از روشهای فولادسازی اولیه است که اصول خاص خود را دارد. در این فرآیند، مقداری آهن با دمای بالا با قراضه آهن در حد لازم به کوره ریخته میشود و با القای جریان الکتریکی توسط میلههای حامل جریان دما افزایش مییابد و در نهایت، تغییرات لازم اعمال شده و فولادسازی انجام میگیرد. در این فرآیند، از خالصکنندههایی همچون آهک برای آسان شدن جداسازی سرباره به مذاب استفاده میکنند. ضمن اینکه فولادسازی با کوره قوس الکتریکی حدود ۴۰ الی ۵۰ دقیقه به طول میانجامد.
فولادسازی ثانویه
اغلب فرآیند تولید ثانویه فولاد در پاتیل صورت میگیرد. از عملیاتی که در پاتیل انجام میشوند میتوان به اکسیژنزدایی، گوگردزدایی، همگنسازی، گاززدایی و درمان در خلاء، نابودی ناخالصیها و اصلاح شیمیایی آنها اشاره کرد؛ این عملیات با هم زدن و حرارت قوس الکتریکی اجرا میشوند. ضمنا، مدیریت دقیق متالورژی پاتیل به تولید فولادهای درجه یک با تلرانس باثبات ختم میشود. در این روش فولادسازی، مدیریت واحدهای متالورژیکی پاتیلی و کنترل دما اهمیت زیادی دارد. با به کارگیری فولادسازی ثانویه امکان عملیاتی نظیر کربن زدایی، آلیاژسازی و... وجود دارد.
ریخته گری فولاد
ریختهگری، روشی جهت تغییر شکل فولاد است؛ در این روش، تغییر شکل با فرآیندهای انجماد ویژه و ذوب انجام میگیرد. این نحوه تغییرات و شکلدهی فولاد سنگ بنای صنایع مهم فولادی جهان است. در کشور ما نیز معمولا برای رویههای ریختهگری از کورههای قوسی استفاده میکنند؛ با این کورهها میتوان فولادهای کربنی و آلیاژی باکیفیتی را تولید کرد. بعلاوه تکنیک شکلدهی فلزات و آلیاژها توسط ذوب شامل مراحل ریختن مذاب در قالب و سپس، شروع فرآیندهای انجماد میشود. این سبک ریختهگری فولاد از قدیمیترین فرآیندهای شکلدهی به فولاد است.
شکل دهی فولاد
همانطور که بیان شد، شکلدهی فولاد با فرآیند ریختهگری امکانپذیر است. این فرآیند شامل دو نوع شکلریزی و شمشریزی میشود. محصولات در ریختهگری شکلریزی دارای هندسه پیچیدهای هستند؛ به همین خاطر درون قالبهای ویژه به شکل نهایی تبدیل میشوند. پروسه شکلدهی نیز با ماشینکاری قطعی میشود و قطعه به سایز دقیق میرسد. بهعلاوه با هدف رسیدن فولاد به خواص مکانیکی عالی یک مرحله عملیات حرارتی بر روی آن صورت میگیرد. با فرآیند شمشریزی نیز مذاب فولاد به مقاطعی نظیر بیلت، بلوم یا اسلب تبدیل میشود. این مقاطع به شکل مربع یا مستطیل هستند و سایز آنها با یکدیگر فرق دارد. بیلت با هدف ریختهگری ساخت میلگرد، سپری، نبشی و ناودانی و... به کار میرود. ابعاد بلوم نیز در مقایسه با بلیت بزرگتر بوده و در ساخت لولههای مانیسمان یا همان لولههای بدون درز استفاده میشود.
تصفیه فولاد
عملیات مختلفی جهت پاکسازی و تصفیه فولاد وجود دارد که یکی از مهمترین آنها، عملیات حرارتی است. عملیات حرارتی شامل بازپخت یا آنیلینگ (آنیل کردن)، نرمال کردن، خاموش و تمپر کردن میشود. بازپخت یا آنیلینگ، میکرو ساختارهایی مانند فریت و سمانتیت را ایجاد میکند و در طی آن، ویژگیهای فیزیکی و شیمیایی فولاد تغییر میکند؛ از تغییرات آن میتوان به کاهش سختی فولاد و افزایش شکلپذیری آن اشاره کرد. تمپر کردن نیز گرم کردن دوباره فولاد تا پایینتر از دمای استحاله یوتکتوئید است. خاموشکننده و معتدل نیز از دیگر عملیات حرارتی است که بعد از سخت و سرد شدن فولاد، چندین تنش داخلی بر روی آن اعمال میشود.
برای تمیز کردن فولاد هم از اسیدشویی استفاده میکنند. سطوح فولاد بنا بر دلایل مختلفی آلوده میشود که این آلودگیها را میتوان با عملیات اسیدشویی برطرف کرد. در این عملیات که نوعی درمان سطحی محسوب میشود، سطوح فولاد با مایع شستشو حاوی اسید پاکسازی شده و ناخالصیهای آن از لکهها و رسوبات گرفته تا زنگزدگی و آلایندههای غیر آلی حذف میشوند. بنابراین، با روش اسیدشویی میتوان فولاد را رسوبزدایی کرد و باعث افزایش طول عمر و پایداری آن شد.
عملیات پوشش سطح نیز که با نام کوتینگ سطح شناخته میشود یکی دیگر از فرآیندهایی است که بر روی فولادهای مختلف انجام میگیرد. این فرآیند، یک رویه پیوسته جهت پوششدهی و رنگآمیزی فولاد است. در فرآیند کوتینگ، سطوح فولاد را با فلز میپوشانند تا مقاومت آن افزایش یابد؛ این پوشش فلزی باعث بهبود کیفیت و مقاومت مواد فولادی میشود. به عبارتی، فولادهایی که عملیات کوتینگ بر روی آنها صورت گرفته است و دارای پوشش فلزی هستند، استحکام بالاتری دارند. بهطورکلی، انجام عملیات حرارتی و پوشش سطحی بر روی فولادها به کارکرد بهتر آنها کمک میکند.
جایگاه ویژه صنعت فولاد ایران
در این مقاله به طور مفصل درباره انواع فولاد و کاربردهای آن صحبت کردیم و با کاربردهای گوناگون آن آشنا شدیم. خوشبختانه صنعت این آلیاژ آهنی در کشور ما از جایگاه ویژه و مهمی برخوردار است. طبق آمارهای منتشر شده، ایران یازدهمین تولیدکننده فولاد در جهان به شمار میرود. شرکت فولاد مبارکه، فولاد کاویان، فولاد خوزستان، گروه ملی صنعتی فولاد ایران و شرکت گروه صنعتی سپاهان از جمله مهمترین قطبهای تولید فولاد در ایران به شمار میروند. به نظر شما چه عواملی در تسریع رشد این صنعت مادر، تاثیرگذارند؟