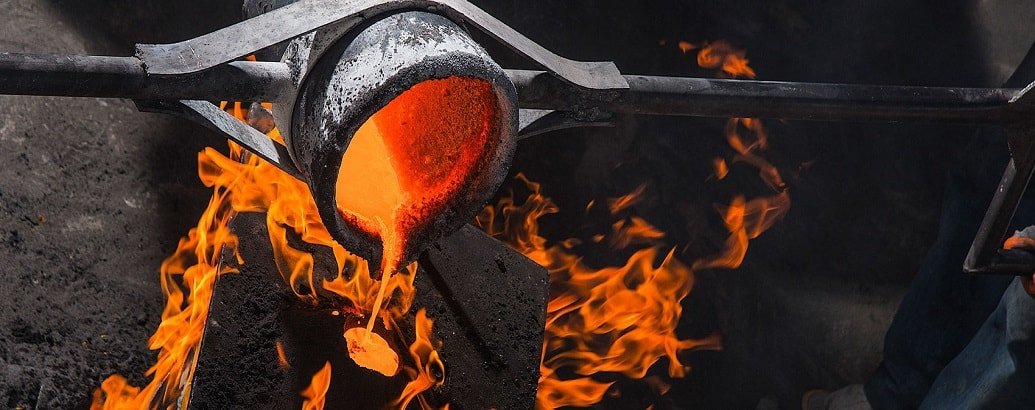
ریخته گری فلزات
ریختهگری فرایندی است که در طی آن مذاب به شکل محفظه قالب منجمد میشود، بنابراین تولید شکلهای پیچیده تنها با روشهای ریخته گری ممکن است، زیرا مذاب با جریان پیدا کردن درون قالب میتواند شکل قالب را به خود بگیرد. در صورتی که در روشهای حالت جامد شکلدهی، بدست آوردن شکلهای پیچیده دشوار است. در این دانشنامه میخواهیم با انواع روشهای ریختهگری فلزات آشنا شویم. انواع روشها عبارت است از:
ریختهگیری در ماسه
دقیق
دایکاستریختهگری گریز از مرکز
مجموعه آهن آنلاین قیمت بیلت را در حالتها، استانداردها، ابعاد و طولهای مختلف ارائه و عرضه میکند. به منظور مشاهده قیمتها به لیست قیمت مربوطه مراجعه فرمایید.
ریخته گری در ماسه
این نوع سادهترین روش است. در این روش ابتدا فلز یا آلیاژ مد نظر تا کمی بالاتر از دمای ذوب آهن درون یک بوته سرامیکی حرارت میدهیم. سپس مذاب را برای یکنواخت شدن توسط یک لوله شیشهای که در تماس با مذاب حل نشود، هم میزنیم. پس از آن مذاب را به درون قالب میریزیم و به آن زمان میدهیم تا قطعه منجمد شود. پس از انجماد کامل قالب را باز میکنیم و ماسه آن را تخریب میکنیم. بلافاصله باید گیت و سیستم تغذیه را با یک ضربه جدا کرد. در ادامه گاهی به منظور بدست آوردن خواص بهتر مکانیکی، قطعه را عملیات حرارتی میکنیم.
معایب ریختهگری معمولی (ریختهگری در ماسه):
- محدودیت در بدست آوردن خواص مکانیکی نهایی بسیار مهم است. به همین دلیل نمونههای ریختهگری اغلب برای بدست آوردن خواص بهتر عملیات حرارتی میشوند.
- کیفیت سطحی و دقت ابعادی در بیشتر این فرآیندها بخصوص در ماسه ضعیف بوده و نیاز به عملیاتهای ثانویه دارد.
- بدلیل تماس مستقیم کارگر با مذاب، خطرات جانی برای کارگر دارد.
- مشکلات و آلودگیهای محیطی
ریخته گری دقیق Casting Investment
روش دقیق یا همان (Casting Investment ) که اصطلاحاً به آن Lost-Wax نیز گفته میشود، روشی است که در آن قالب از مواد فراری تهیه میشوند که این مواد پس از انجماد کامل و در اثر جذب حرارت از مذاب از بین میروند، این مواد به روش دوغاب سرامیکی تهیه میشوند و با توجه به فرار بودن آنها میتوان گفت در روش دقیق هم مدل و هم قالب فقط یک بار استفاده میشود.
باتوجه به نوع تهیه قالب دو نوع روش دقیق وجود دارد:
- روش پوستهای
- روش توپر
به طور کلی میتوان گفت که این دو روش در تهیه مدل با هم تفاوتی ندارند و فقط در نوع قالب با هم متفاوت هستند.
مهمترین مزایای ریختهگری دقیق
- با توجه به دقت ابعادی این روش، امکان طراحی و ریختهگری قطعات پیچیده صنعتی وجود دارد.
- امکان دستیابی به انوع آلیاژ های فولادی و غیر فولادی.
- دقت ابعادی بسیار بالا طبق استانداردهای ASM.
- کیفیت سطحی بسیار خوب که از بدون شک از کیفیت سطحی قطعات تولید شده به روش ریختهگری در ماسه بالاتر است.
- به حداقل رسیدن سطوح تراش بعلت کیفیت سطحی عالی و در نتیجه صرفه جویی در اتلاف مواد.
- کاهش عیوب و به حداقل رسیدن امکان ایجاد مک و ترکهای سطحی، با اعمال پیش گرم کردن و یا پخت قالبهای سرامیکی قبل از این فرآیند.
- بدلیل ایجاد عیوب کمتر در حین ریختگی، خواص مکانیکی بالاتر قابل دستیابی است.
- بعلت فرار بودن مواد قالب خط جدایش حذف میشود که با حذف این خط در نهایت عیوبی حذف خواهند شد که در اثر خط جدایش به وجود آمدهاند.
مهمترین محدودیتهای ریختهگری دقیق
- اندازه و وزن قطعات تولید شده با این روش محدود بوده و عموما قطعات با وزن کمتر از ۵ کیلوگرم با این روش تولید میشود
- هزینه تجهیزات و ابزارها در این روش نسبت به روشهای دیگر، بیشتر است.
ریختهگری به روش دایکاست
این ریختهگری از روشهای دیگر دائم بوده که در آن مذاب با فشار بالا به درون محفظه قالب تزریق میشود. روش دائم به روشهایی گفته میشود که در آن قالب از بین نمیرود و برای قطعات بعدی نیز مورد استفاده قرار میگیرد. جنس این قالبها از فلزات است. در این روش مذابی که تحت فشار به درون قالب فرستاده شده است، تا انجماد نهایی تحت فشار قرار دارد و پس از انجماد کامل فشار برداشته شده، قالب باز شده و قطعه به بیرون پرت میشود. فشار مورد استفاده در این روش بین ۷ تا ۳۵ مگاپاسکال است.
مزایای دایکاست
- با توجه به صرفهجویی در قالب، برای تولید بالا مناسب است.
- دقت ابعادی (۰۷۶۰ (±و کیفیت سطح خوب است.
- تولید مقاطع نازک امکانپذیر است.
- به خاطر نرخ سرد شدن بالا ساختار ریزدانه شده و خواص مکانیکی بهبود مییابد.
معایب دایکاست
- بخاطر جنس فولادی قالبها معمولا این روش محدود به فلزات با نقطه ذوب پایین است ضمن اینکه تولید قطعات خیلی پیچیده امکانپذیر نیست
- وجود پلیسه در فصل مشترک و پینهای پران
ریختهگری گریز از مرکز
این ریختهگری روش نیرویی که سبب انتقال فلز مذاب به درون قالب میشود نیروی گریز از مرکزی است که موجب میشود مذاب روی بدنه قالب توزیع میشود، این نیرو از چرخش سریع قالب ایجاد میشود.
این روش به سه حالت زیر صورت میگیرد:
- گریز از مرکز حقیقی
- نیمه گریز از مرکز
- تحت نیروی گریز از مرکز یا قطعات گریز از مرکز شده
از معایب این روش به طور خلاصه میتوان گفت:
- پر نشدن کامل قطعه که به علتهای زیر مربوط میشود: عدم کافی سیالیت مذاب، دمای فوق ذوب کم، سرعت پایین ریختن مذاب درون قالب و سطح مقطع خیلی کم ورود مذاب در این روش.
- ترک سرد که هنگامی بوجود میآید که دو جبهه جریان مذاب به هنگام رسیدن به یکدیگر، به دلیل سرد شدن زود هنگام در هم نفوذ نکردهاند و موجب ایجاد ترک درون قطعه میگردد.
- تاول سرد یعنی فلز مذاب در طول ریختن پاشش کرده و گلولههای جامد شکل گرفته و در قطعه محبوس میشوند.
- ایجاد حفرات انقباضی که همانطور که از نام آن پیداست، تورفتگی سطحی یا حفره های داخلی که به دلیل انقباض پس از انجماد بوجود میآیند.