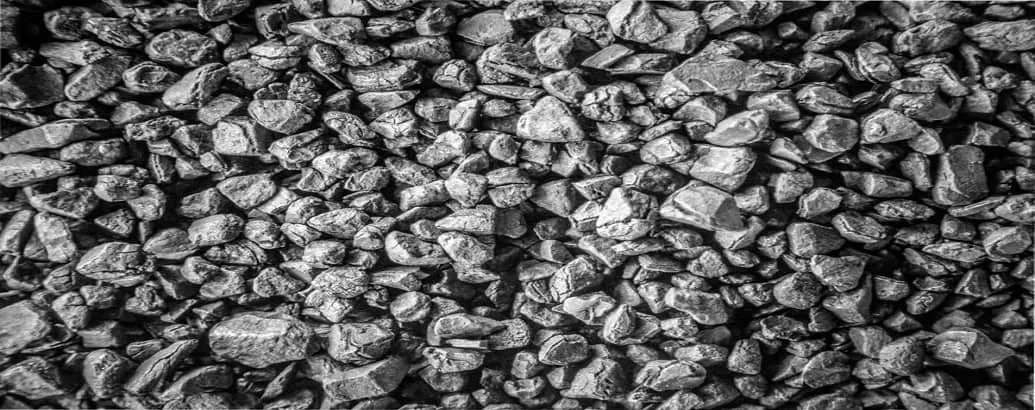
آهن اسفنجی چیست؛ روشهای تولید و کاربرد
شاید نام عجیب آهن اسفنجی (sponge iron) قبلا در اخبار یا روی تابلوی معاملات بورس کالا به چشمتان خورده باشد. محصولی که تجارت آن در چند وقت اخیر رونق زیادی پیدا کرده و گزینه جذابی برای خریداران به شمار میرود. آهن اسفنجی یا همان گندله متخلخل، حاصل احیای مستقیم سنگآهن است که یکی از ویژگیهای قابل توجه آن، داشتن عیار بالاست. این خاصیت مهم باعث شده که جایگزین مناسبی برای آهن قراضه شود وهمواره مورد توجه متخصصان قرار بگیرد. در طی سالهای اخیر روشها و تکنولوژیهای گوناگونی مانند کورهی تونلی، میدرکس و... برای تولید پربازدهتر آن ابداع شد. در این میان ایران با بهرهگیری از تلاش متخصصان داخلی در دهها واحد صنعتی کوچک و بزرگ در سراسر کشور، تکنولوژی ساخت آهن اسفنجی را تا درصد بالایی بومیسازی کرده و هماکنون دومین تولیدکننده بزرگ آن در جهان به شمار میرود.
در این مقاله سعی شده درباره این محصول توضیحات بیشترو روشنتری ارائه شود، پس اگر سوالات زیادی دربارهی آهن اسفنجی در ذهنتان شکل گرفته اصلاً نگران نباشید! در ادامه جوابشان را پیدا خواهید کرد.
طبق نظر کارشناسان آهن آنلاین:
آهن اسفنجی یا DRI (آهن احیای مستقیم) مادهای است که از احیای سنگآهن (به شکل کلوخه، گلوله یا خاکروبه) به صورت مستقیم یعنی بدون ذوب کردن، به دست میآید. امروز در کورههای القایی می توان تا ۵۰ درصد آهن اسفنجی را جایگزین ضایعات کرد.
آهن اسفنجی چیست؟
آهن اسفنجی یا DRI (آهن احیای مستقیم) مادهای است که از احیای سنگآهن (به شکل کلوخه، گلوله یا خاکروبه) به صورت مستقیم یعنی بدون ذوب کردن، به دست میآید. در طی فرآیند احیای مستقیم و به دلیل خروج گاز اکسیژن، سنگآهن به قطعههایی کروی شکل تبدیل میشود که مانند اسفنج در سطح خود دارای سوراخهای کوچکی است. همین ویژگی ظاهری علت نامگذاری خاص این محصول شده است.
میزان عیار آهن اسفنجی بین ۸۴ تا ۹۵ درصد است که مقدار بالایی به شمار میرود. در جد.ل زیر ترکیب شیمیایی و چگالی این محصول فولادی در دو شکل متفاوت کلوخه و نرمه نمایش داده میشود.
در سالهای اخیر بیش از ۵ درصد فولاد مصرفی جهان ازاین نوع آهن به دست آمده است. با توجه به میزان بالای آلایندگی هوا، مشکلات زیست محیطی موجود در سایر روشهای تولید آهن و همچنین مناسبتر بودن قیمت آهن اسفنجی انتظار میرود که میزان استفاده از این محصول در آینده بیشتر نیز بشود. برای کسب اطلاع بیشتر در مورد لیست قیمت آهن برای لینک فوق مراجعه کنید.
در سال ۱۳۸۹ برای اولین بار در ایران و در استان یزد کارخانهای از این ماده در کوره القایی خود استفاده کرد. به دنبال آن کارخانههای دیگر نیز شروع به استفاده از این محصول کردند اما به دلایلی مانند عدم آشنایی با روش شارژ، بالا بودن کربن موجود و... زمان ذوب در کورههای القایی افزایش پیدا کرد. درمجموع بازخورهای اولیه از این محصول رضایتبخش نبود. اما به تدریج و با گذشت زمان تولیدکنندگان توانستند با روشهایی راندمان کورهها را افزایش داده و استفاده از آهن اسفنجی را ادامه دهند.
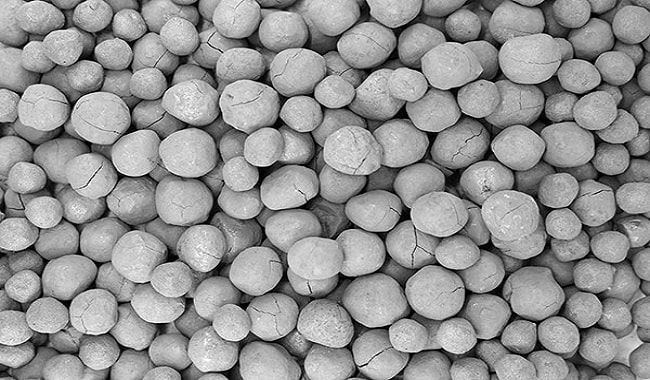
روش های تولید آهن اسفنجی sponge iron
تولید آهن به روش احیای مستقیم که آهن اسفنجی از آن حاصل میشود، در مقایسه با سایر شیوههای تولید آهن جدیدتر است و پیدایش آن در جهان به دهه ۷۰ میلادی برمیگردد. در روشهای احیای مستقیم ماده احیاکننده مورد استفاده، میتواند ذغالسنگ یا گاز طبیعی باشد که البته استفاده از ذغالسنگ سابقهی طولانیتری دارد.
برای تولید آهن اسفنجی با استفاده از گاز طبیعی از فناوریهای زیر استفاده میشود:
• میدرکس
• HYL
• Purofer
از بین این سه فناوری، میدرکس و HYL پرکاربردتر و پربازدهتر هستند.
در روش میدرکس، سنگآهن دارای عیار ۶۷ درصد، بدون نیاز به واسطه و با استفاده از گازهای شکسته شده احیا میشود. به این شکل که گاز طبیعی به وسیله حرارت و کاتالیزورهای خاصی، در واحد شکست گاز تجزیه شده و هیدروژن و کربن مونواکسید آزاد میکند. سپس این دو گاز وارد کوره احیا شده، با اکسیژن موجود در آهن مذاب ترکیب میشوند و سنگآهن احیا میشود، در نتیجه آهن اسفنجی با عیار بالا به دست میآید. آهن اسفنجی تولید شده در دمای ۶۰۰ درجه سانتیگراد، جهت تصفیه به کورههای قوس الکتریکی (EAF) منتقل شده و عملیات فولادسازی روی آن آغاز میشود.
در روش HYL علاوه بر استفاده از گاز طبیعی شکسته شده به عنوان احیاکننده، از بخار آب نیز برای افزایش مقدار هیدروژن تولید شده استفاده میکنند. بنابراین در این روش مقدار هیدروژن نسبت به مونواکسید کربن بسیار بیشتر بوده و نقش عامل اصلی احیاکننده را ایفا میکند. کوره احیا نیز مشابه همان کوره میدرکس است، ولی فشارمحیط واکنش در سطح بالاتری (۷ اتمسفر) در نظر گرفته شده تا واکنشها با سرعت موردنظر انجام شود.
برای تولید آهن اسفنجی با استفاده از زغالسنگ نیز از روشهای زیر استفاده میشود:
- روش کورهی تونلی
- SL/RN
کوره تونلی دارای ساختاری بلند و طویل است که از آجرهای نسوز ساخته شده و در کف آن ریلهای مخصوص قرار داده میشود. فرآیند طراحی شده در این کوره به ترتیب شامل سه مرحله پیشگرمایش، احیا و خنک شدن است. آهن اولیه به شکل پودر از این تونل عبور کرده و در مجاورت ذغالسنگ قرار میگیرد و در اثر حرارت ناشی از سوختن گاز طبیعی با اکسیژن هوا احیا میشود.
روشSR/NL از قدیمیترین فرآیندهای احیا به شمار میرود و ایده آن از کوره افقی تولید سیمان گرفته شده است. در این کوره ذغالسنگ حرارتی به عنوان ماده احیاکننده با ذغالسنگ ترکیب شده و آهن اسفنجی تولید میشود.
روش میدرکس برای تولید آهن اسفنجی چیست؟
کاربردیترین و پراستفادهترین روش برای تولید آهن اسفنجی، روش میدرکس است. برای تولید آهن اسفنجی به این روش، در ابتدا گاز طبیعی به واحد شکست گاز ورود پیدا میکند و پس از دریافت حرارت و پروسهای پیچیده به هیدروژن و کربن تبدیل میشود. هیدروژن و کربن به دست آمده از گاز طبیعی وارد کوره القایی یا کوره احیا میشوند تا با ترکیب با گندله سنگ آهن که از قبل در کوره پخته شده است، باعث احیای سنگ آهن و تولید آهن اسفنجی شود.
روش میدرکس از این جهات بسیار مورد اسقتبال قرار گرفته است که میتواند با کاهش حداکثری مصرف گاز، بیشترین بازدهی ممکن را برای تولیدکننده به ارمغان بیاورد. هماکنون در ایران و جهان، تولید آهن اسفنجی در اکثر مواقع با تکیه بر همین روش حاصل میشود. سوال مهمی که ممکن است ایجاد شود، این است که تفاوت اصلی روش میدرکس و HYL برای تولید آهن اسفنجی چیست؟ پاسخ کوتاه و واضح است؛ مصرف بسیار بالای برق و محدودیت در ظرفیت تولید، 2 دلیل اصلی هستند.
تفاوت کوره احیا و کوره میدرکس در چیست؟
یکی دیگر از روشهای تولید آهن اسفنجی، استفاده از روش HYL است؛ در این روش با استفاده از گاز طبیعی شکستهشده، از عوامل دیگر مثل بخار آب هم برای تولید بیشتر هیدروژن استفاده میشود. با همه این اوصاف، در روش HYL مقدار هیدروژن نسبت به میزان مونو اکسید کربن تولیدشده بیشتر است و همین میتواند به احیا شدن مستقیم سنگ آهن منجر شود. کوره احیا عملکردی شبیه به کوره میدرکس دارد، ولی فشار محیطی در اندازهای بالاتر (معادل با 7 اتمسفر) صورت خواهد گرفت.
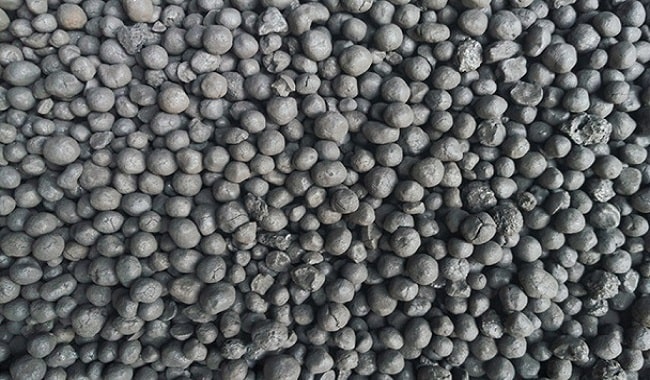
روشهای دیگر برای تولید آهن اسفنجی چیست؟
از روشهای دیگری که برای تولید آهن اسفنجی به کار گرفته میشوند، میتوان به روشهای کوره تونلی و SL/RN اشاره کرد. کورههای تونلی بسیار طویل هستند و 3 مرحله پیشگرمایش، عملیات احیای سنگ آهن و خنک شدن را شامل میشوند. در این روش، سنگ آهن به شکل خردشده وارد کوره خواهد شد و با قرار گرفتن در کنار ذغال سنگ و مواجهه با حرارتی که از سوختن گاز طبیعی با اکسیژن حاصل شده است، به اصطلاح احیا میشود.
اما روش SL/RN برای تولید آهن اسفنجی چیست؟ در این روش هم به جای استفاده از گاز طبیعی، از ذغال سنگ برای احیای سنگ آهن استفاده میشود تا با استفاده از کورههای افقی، آهن اسفنجی تولید شود.
مزایای استفاده از آهن اسفنجی چیست؟
همانطور که گفتیم، حدود 5 درصد از بازار آهنآلات جهان را آهنهای اسفنجی تشکیل میدهند؛ این آمار نشاندهنده اهمیت این محصولات آهنی در صنایع مختلف است. اما چه مزیتهایی در بطن آهنهای اسفنجی نهفته شدهاند که میتوانند آن را به یک محصول بسیار مهم تبدیل کنند؟ در زیر، خلاصهای از مزایای مهم آهن اسفنجی را در اختیار شما قرار خواهیم داد:
• آهن اسفنجی بهترین جایگزین برای ضایعات است.
• کورههای القایی یا واحدهای احیای مستقیم، هزینه کمتری نسبت به کورههای بلند دارند.
• آهنهای اسفنجی از عیار و خلصو بسیار بیشتری نسبت به یگر محصولات آهنی برخوردارند.
• انتقال و حملونقل آهن اسفنجی به شکل آهن گرم کلوخهشده (HBI) بسیار آسان و بدون دردسر است.
• برای تولید آهن اسفنجی به روش مستقیم میتوان از گاز طبیعی، آنهم بدون جداسازی ناخالصیها استفاده کرد.
• صرفه اقتصادی آهنهای اسفنجی بسیار بالاست و میتوان با تولید آنها از بازدهی بالایی برخوردار شد.
کاربردهای آهن اسفنجی
با توجه به کمبود آهن قراضه که جهت تولید شمش و سایر محصولات فولادی به کار میرود، یافتن جایگزین مناسبی برای آن دارای اهمیت است. آهن اسفنجی محصولی است که میتواند برای تولید این محصولات، در کورههای القایی جایگزین آهن ضایعاتی شود.
امروز در کورههای القایی می توان تا ۵۰ درصد آهن اسفنجی را جایگزین ضایعات کرد. همچنین آهن اسفنجی درریخته گری به سه شکل بیلت، اسلب و میلگرد کاربرد داشته و تحول عظیمی در این صنعت ایجاد کرده است.
نوع فشرده شده آهن اسفنجی که به آن بریکت (Briquette) گفته میشود مشکلات حمل و نقل کمتری داشته و ذخیرهسازی آن نیز آسانتر است. علاوه بر این بریکت مقاومت بالاتری در برابر ساییدگی و زنگزدگی هم دارد و احتمال ایجاد تخلخل (جدایی سطح) در آن کمتر است. با توجه به نوع مواد و دمایی که در آن بریکتزنی انجام میشود سه نوع بریکت وجود دارد:
- بریکت گرم
- بریکت سرد
- بریکت نرمه
بریکت گرم در دمای بیشتر از ۶۵۰ درجه سانتیگراد تولید شده و شناخته شدهترین و پرکاربردترین نوع بریکت به شمارمیرود. بریکتهای سرد و نرمه در دمای محیط تولید میشوند ولی نوع مواد استفاده شده در آنها متفاوت است.
تفاوت بریکت با آهن اسفنجی چیست؟
بریکتها در واقع همان آهنهای اسفنجی هستند، البته با تفاوت اینکه آنها در قالبهایی بزرگ قرار میگیرند و در نهایت فشرده میشوند. بریکتها از طریق 2 روش بریکستسازی سرد و گرم قابل تولید هستند و در انواع بریکت گرم، بریکت نرمه آهن اسفنجی و بریکت سرد آهن اسفنجی قابل ارائه خواهند بود.
بریکت گرم بریکت سرد آهنی
در پروسه بریکتسازی و با توجه به آهن اسفنجی گرم یا HDRI در دمای بالای 650 درجه سانتیگراد تولید میشود. موارد ورودی در دمای محیط وارد پروسه بریکتسازی میشوند.
شناختهشدهترین بریکت حال حاضر است و حملونقل آن آسان خواهد بود. 2 نوع محصول، شامل بریکت نرمه و بریکت سرد از آن حاصل میشوند.
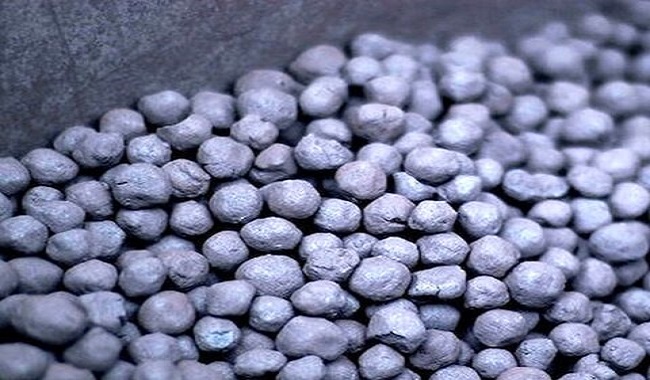
تفاوت گندله و آهن اسفنجی
کنستانتره سنگآهن مادهی اصلی اولیه در تولید گندله است که به دلیل ریز بودن ذراتش، امکان استفاده مستقیم از آن در فرآیند احیا وجود ندارد. گلولههایی که از ترکیب کنستانتره سنگآهن و چند نوع مواد افزودنی دیگر تولید میشوند را گندله میگویند. این گلولهها در ابتدا خام هستند و سپس پخته و سخت میشوند و در فرآیند احیا با روشهای گفته شده به آهن اسفنجی تبدیل میگردند. بنابراین گندله ماده اولیه برای تولید آهن اسفنجی است. به آهن اسفنجی گندله متخلخل نیز میگویند که باید ویژگیهای مکانیکی و شیمیایی خاصی را برای استفاده در کورههای احیا داشته باشد.
سایرمواد اولیه برای تولید گندله سنگآهن عبارتند از:
- بنتونیت
- شیرآهک
- مادهی آلی
- آهک
- آب
- سیمان
کارخانههای تولیدکننده آهن اسفنجی
همانطور که اشاره شد تولید و استفاده از آهن اسفنجی در ایران از سال ۸۹ شروع شده و سابقه کوتاهی دارد ولی جالب است بدانید که هماکنون کشور ما در کنار هندوستان از بزرگترین تولیدکنندگان آهن اسفنجی در جهان به شمار میرود. بدون شک این امر حاصل تلاش بیوقفه واحدهای صنعتی کوچک و بزرگ در سراسر کشور بوده است.
فولاد مبارکه اصفهان و زیرمجموعههای آن مانند فولاد هرمزگان جنوب، صنایع معدنی فولاد سنگان و فولاد امیرکبیر کاشان و... از جمله این شرکتها هستند که سهم بزرگی از تولید آن در کشور را به خود اختصاص دادهاند.
برای مشاهده کلیه کارخانههای فولاد ایران میتوانید به لینک فوق مراجعه کنید و در مورد هرکدام اطلاعات کاملی را کسب کنید.
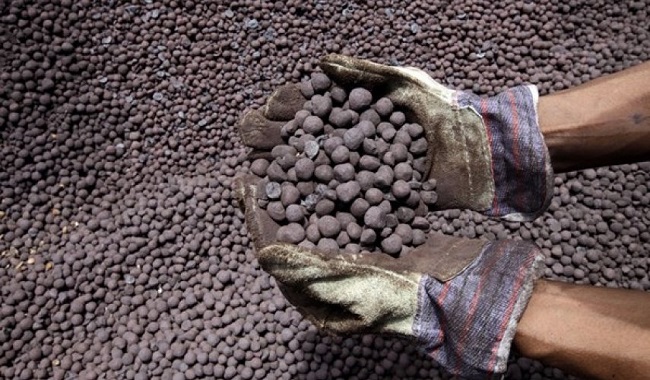
یکی دیگر از برندهای مطرح کشور در این حوزه، شرکت توسعه و آهن فولاد گلگهر است که گام بزرگی در بومی سازی تولید کنستانتره، گندله، احیا و تولید فولاد برداشته و توانسته تا ۸۰ درصد ابزارهای مورد نیاز در این بخش را در داخل کشور تامین کند. این کارخانه در سال گذشته بیش از ۳ میلیون تن آهن اسفنجی به بازار عرضه کرده که از این مقدار بیش از ۹۰ درصد آن به مصرف داخلی رسیده است.
در بیشتر کشورها از جمله ایران واحدهای تولید آهن اسفنجی و فولاد در کنار هم ساخته میشوند و به نوعی خود تولیدکنندگان مصرفکننده آن هستند، بنابراین تجارت این محصول برآیندی از عدم توازن بین تولید و مصرف در این واحدها است. آهن اسفنجی همواره به عنوان جایگزینی برای قیمت ضایعات آهن و البته ماده اصلی تولید مقاطع و محصولات فولادی محسوب میشود و میتوان نفوذ و اهمیت آن در بازارهای جهانی را به وضوح مشاهده کرد.
سخن پایانی
آهن اسفنجی که در طی فرآیندهایی از نرمه (کنستانتره) سنگآهن به دست میآید به عنوان ماده اولیه برای تولید محصولات فولادی مختلف به کار میرود. با توجه به حجم بالای تولید و قیمت پایینتر آن در کشور، یکی از محصولات مناسب صادراتی به شمار میرود و تجارت آن سود خوبی دارد. با این وجود، قیمت آن مانند تمامی کالاها تابعی از وضعیت اقتصاد جهانی و داخلی است.
شما درباره آینده این محصول چگونه فکر میکنید؟ آیا همچنان ثبات خود را حفظ کرده و میزان تولید آن بیشتر از نیاز داخلی خواهد بود یا ممکن است وضعیت متفاوتتری پیش روی کارخانههای تولیدکننده قرار داشته باشد؟