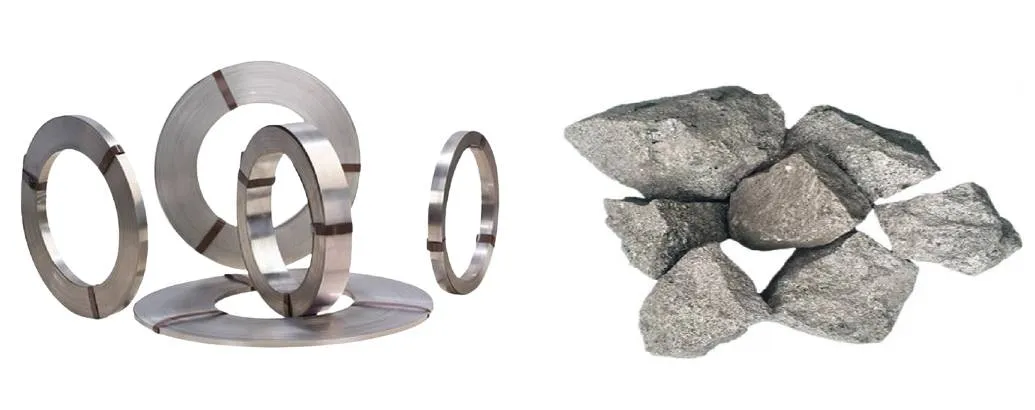
آلیاژ آهنی چیست؛ بررسی مشخصات و فرآیند تولید آن
صنعت مدرن بدون مواد مقاوم و بادوام نمیتواند پیشرفت کند، و آلیاژهای آهنی یکی از مهمترین موادی هستند که نقش کلیدی در توسعه فناوری و زیرساختهای جهانی دارند. این ترکیبات با ویژگیهای منحصربهفرد خود، بهینهسازی عملکرد و افزایش طول عمر محصولات صنعتی را ممکن میسازند. در بسیاری از صنایع، از ساختوساز و خودروسازی گرفته تا تجهیزات صنعتی و فناوریهای پیشرفته، حضور این آلیاژها ضروری است. شناخت ترکیب، خواص و کاربردهای آنها میتواند به درک بهتر نحوه انتخاب و استفاده از مواد مناسب در پروژههای مختلف کمک کند. در این مقاله، به بررسی دقیقتر آلیاژهای آهنی، انواع مختلف آنها و تأثیرشان بر صنعت و زندگی روزمره خواهیم پرداخت.
آلیاژ آهن چیست؟
آلیاژ آهنی به ترکیباتی گفته میشود که در آن آهن بهعنوان عنصر پایه حضور دارد و با افزودن عناصر دیگری مانند منگنز، سیلیسیم، آلومینیوم و سایر عناصر آلیاژی، ویژگیهای فیزیکی و شیمیایی آن بهبود مییابد. این آلیاژها نقش اساسی در تولید فولاد و چدن ایفا میکنند و بسته به ترکیب عناصر، خواصی مانند استحکام، مقاومت به خوردگی، شکلپذیری و سختی را در محصولات نهایی تقویت میکنند. آلیاژهای آهنی به دلیل کاربرد گسترده در صنایع مختلف از جمله ساختوساز، خودروسازی، تولید ماشینآلات صنعتی و زیرساختهای عمرانی، بهعنوان مواد استراتژیک در جهان شناخته میشوند. چین، هند و آفریقای جنوبی از بزرگترین تولیدکنندگان این مواد هستند و تأمین پایدار آنها نقش مهمی در توسعه صنعت فولاد و صنایع وابسته دارد.
ترکیبات آلیاژ آهنی
درصد کربن به عنوان یکی از عناصر اصلی موجود در ترکیب آلیاژ آهنی حدود 02/0 الی 6 است. معمولا آلیاژهای آهنی از نوع فولاد کمتر از 2 درصد و دسته مربوط به چدنها بیش از 2 درصد کربن دارند. از سایر عناصری که قابلافزودن به ترکیب آلیاژهای آهنی هستند میتوان به فروآلومینیوم، فرو سر یوم، فرونیکل، فروکروم، فروبور، فرومنگنز، فرومنیزیوم، فروفسفر، فرومولیبدن، فرونیوبیم، فروتیتانیوم، فروسیلیسیم، فروسیلیکون منیزیوم، فروتنگستن، فرووانادیوم و فرو اورانیوم اشاره کرد. آلیاژهای آهنی بر مبنای میزان کربن و عناصر مختلف خود دارای خواص و ویژگیهای منحصربهفردی هستند.
ویژگی های آلیاژ آهنی
ویژگیهای آلیاژ آهنی به نوع آن بستگی دارد؛ اما بهطورکلی، میتوان گفت که آنها ساختاری سخت و قوی دارند. البته مقاومت برخی از مدلهای آن مانند فولاد نرم در برابر خوردگی کم است. چدنها نیز به عنوان یکی دیگر از آلیاژهای آهنی ساختار نرم و شکنندهای دارند و احتمال خوردگی آنها بر اثر زنگزدگی وجود دارد. از آلیاژهای آهنی سخت و محکم که در برابر سایش و خوردگی آسیب نمیبینند میتوان به فولاد ضد زنگ و فولاد کربن بالا اشاره کرد. در ادامه با انواع آلیاژ آهنی و خصوصیات آنها بهطور کامل آشنا خواهید شد.
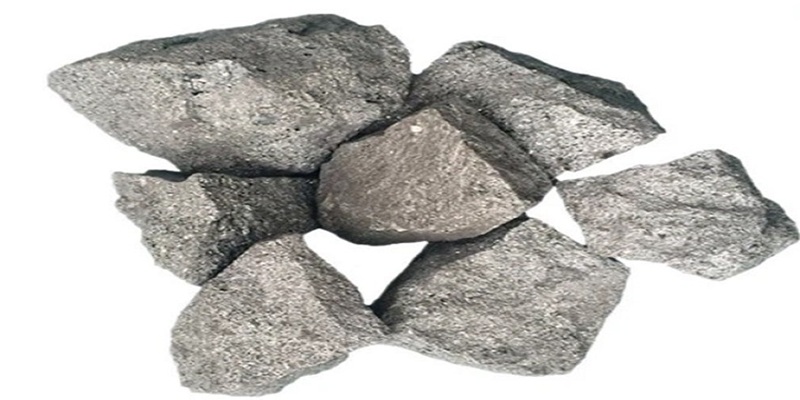
مصرف یا کاربرد آلیاژ آهنی
آلیاژ آهنی بهطور گستردهای در صنعت فولادسازی بکار گرفته میشود. به عبارت بهتر، بسیاری از محصولات فولادی را با بهرهگیری از آلیاژهای آهنی میسازند؛ از میز و صندلی گرفته تا تجهیزات مختلف صنعتی قابلتولید با آلیاژهای آهنی هستند. شایان ذکر است، آلیاژهای آهنی بسته به عناصر موجود در ترکیب خود در حوزه خاصی بکار گرفته میشوند. در ادامه عناصر آلیاژهای آهنی را که روند تولید و مصرف آنها را تعیین میکنند، معرفی کردهایم:
- فرونیکل
اکثر شهابسنگهایی که راهی زمین میشوند از نوع فرونیکل بوده و به صورت کاماسیت یا تانیت هستند. همچنین، ساختار کریستالی فرونیکل به حالت FCC است که میتواند به اشکال فریت، مارتنزیت یا آستنیت درآید. بعلاوه از کشورهای تولیدکننده فرونیکل میتوان به چین، ژاپن، کلمبیا و کالدونیای جدید اشاره کرد.
- فرومنگنز
منگنز دارای آلیاژهای مختلفی است که از بین آنها، فرومنگنز و سیلیکومنگنز در صنعت فولادسازی بکار گرفته میشوند؛ درواقع، این دو آلیاژ از مواد اصلی فولادسازی هستند. آلیاژ فرومنگنز توسط کشور چین در تناژهای سنگین تولید شده و راهی بازار جهانی میشود. ظرفیت تولید فرومنگنز چین به عنوان بزرگترین تولیدکننده آن به حدود 2.7 میلیون تن در سال میرسد. از سایر تولیدکنندگان بزرگ و مطرح فرومنگنز میتوان به برزیل، آفریقای جنوبی و اوکراین اشاره کرد.
- فرومولیبدن
کنسانترههای مولیبدنت جهت ایجاد اکسید مولیبدیک برشته شده و تبدیل به فرومولیبدن یا فلز مولیبدن میشوند. کشورهای شیلی، چین و ایالات متحده از بزرگترین تولیدکنندگان فرومولیبدن در جهان هستند. حدود 78 درصد از تولید سنگ معدن مولیبدنیت در جهان نیز به این کشورها تعلق دارد و آنها با بهرهگیری از امکانات خود به تولیدکنندگان مطرح فرومولیبدن در عصر ما تبدیل شدهاند. از دیگر تولیدکنندگان فرومولیبدن میتوان به کانادا، مکزیک و پرو اشاره کرد.
- فروکروم
فروکروم یکی دیگر از آلیاژهای مصرفی در دنیای آهن و فولادسازی است که بهطور گستردهای در تولید فولاد ضد زنگ مورداستفاده قرار میگیرد. این آلیاژ با ذوب سنگ کرومیت در کوره قوس الکتریکی تولید میشود و حدود 50 الی 70 درصد کروم دارد. میزان تولید فروکروم در گذشته نیز حدود 11.7 میلیون تن در سال بود؛ اما اکنون به بیش از 40 میلیون تن رسیده است. همچنین، درصد قابلتوجهی از این حجم به کشورهای چین، آفریقای جنوبی، قزاقستان و هند تعلق دارد.
- فرو سیلیسیم
فرو سیلیسیم یکی دیگر از انواع آلیاژ است که عناصر اصلی آن را آهن و سیلیسیم تشکیل میدهند. از سایر عناصر موجود در آن که در زمره عناصر ناخواسته قرار دارند میتوان به آلومینیوم، کربن، کروم، گوگرد، فسفر و تیتانیوم اشاره کرد. همچنین، این آلیاژ به روش کوره قوس الکتریکی در درصدهای 10 الی 90 درصد تولید میشود؛ هدف از تولید فرو سیلیسیم نیز ساخت فولاد و چدن است. بزرگترین تولیدکنندگان فرو سیلیسیم عبارتاند از چین، نروژ، روسیه و ایالات متحده که بیشترین سهم تولید به چین اختصاص دارد.
- فروتیتانیوم
معمولا فروتیتانیوم با ذوب القایی قراضه تیتانیوم با فولاد یا آهن به دست میآید. حتی آن را میتوان به شکل مستقیم با کنسانتره معدنی تیتانیوم تولید کرد. بهطورکلی، از آلیاژ تیتانیوم در فولادسازی جهت اکسیدزدایی، تنظیم اندازه دانه و ثابتسازی کربن و نیتروژن استفاده میکنند. در جریان فولادسازی، تیتانیوم به علت دمای ذوب کم و چگالی بالا اغلب به عنوان فروتیتانیوم مورداستفاده قرار میگیرد. بعلاوه از کشورهای فعال در زمینه تولید فروتیتانیوم میتوان به هند، چین، ژاپن، روسیه، اوکراین، بریتانیا، ایالات متحده و برزیل اشاره کرد.
- فروتنگستن
تنگستن از آلیاژهای مهم صنعت فولادسازی است که در فولادهای مختلف مانند فولاد ضد زنگ بکار میرود. این آلیاژ به مذاب فولاد تحت عنوان فروتنگستن افزوده میشود؛ این ترکیب میتواند تا حدود 80 درصد تنگستن را در خود جای دهد. همچنین، فروتنگستن جزو آلیاژهای باارزش و گرانقیمت بازار جهانی است که با نرخ نسبتا بالایی در اختیار مصرفکنندگان قرار میگیرد. بزرگترین تولیدکننده فروتنگستن نیز کشور چین است که به عنوان صادرکننده اصلی آن در جهان شناخته میشود.
- فرو وانادیم
فرو وانادیم معمولا از سنگ معدن مگنتیت دارای تیتانیوم که جهت ساخت آهن خام فرآوری شده موردبازیابی قرار میگیرد. این پروسه نیاز به احیای اکسید وانادیم توسط واکنش آلومینوترمیک، آهن قراضه و همینطور، آلومینیوم به عنوان عنصر احیاکننده دارد. سرباره موجود دارای 20 الی 24 درصد پنتوکسید وانادیم است که امکان تبدیل آن به فرووانادیم حاوی 40 الی 50 درصد وانادیم وجود دارد. همچنین، بیشترین فرووانادیم تولیدشده در جهان نیز به کشورهای چین، روسیه و آمریکای جنوبی تعلق دارد.
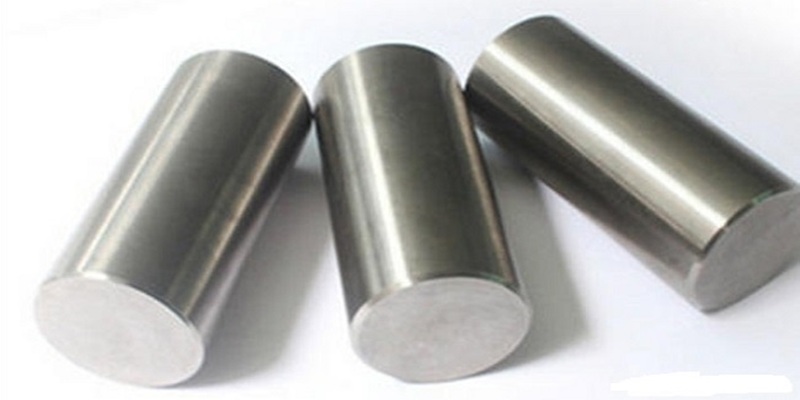
انواع آلیاژ آهنی
بهطورکلی، آلیاژ به دو گروه بزرگ آلیاژ آهنی و آلیاژ غیر آهنی تقسیم میشود. آلیاژ آهنی همانطور که اشاره شد، بر پایه آهن است و گروهبندی مختص به خود را دارد. مهمترین آلیاژ آهنی نیز فولاد است که کشف آن، تحول عظیمی در زندگی ما ایجاد کرد. در ادامه انواع آلیاژ آهنی و خصوصیات آنها را به صورت مختصر و مفید شرح دادهایم:
- آهن فرفوژه
آهن فرفوژه یکی از انواع آلیاژ آهنی است که از آهن خالص به دست میآید. مقدار کربن آن که از آهن خام در کوره پودینگ حاصل میشود از 0.08 درصد کمتر است. درضمن، کربن و سایر عناصر موجود در آهن خام طی فرآیند صورت گرفته در کوره از آن خارج میشوند و درنهایت خروجی کار، آهن خالص است. همچنین، در روند تولید، کمی سرباره با آهن ترکیب میشود تا ساختاری فیبری ایجاد کند و رشتههای بلند سرباره واقع در طول آن با رشتههای بلند آهن ترکیب شوند. شایان ذکر است، این سرباره میزان مقاومت آهن فرفوژه در برابر خوردگی و اکسیداسیون را بهبود بخشیده و آن را به یک آهن ضد زنگ تبدیل میکند. درکل، از این آلیاژ آهنی در مواردی نظیر ساخت مبلمان مدرن خانگی، نردههای ایوان، زنجیر، سیم خاردار، میخ و... استفاده میکنند.
- چدن
چدن از ذوب مواد پایهای نظیر آهن خام، کک و سنگ آهن در کوره حاصل میشود و سپس، آن را به قالبهای شن و ماسه یا فولاد آلیاژی منتقل میکنند. مقدار کربن آلیاژ آهنی چدن حدود 1.7 الی 4.5 درصد است و عنصر سیلیکون نیز در ساختار آن وجود دارد. از مهمترین مشخصات چدن میتوان به سختی بالا و مقاومت مطلوب در برابر سایش اشاره کرد. تردی و استحکام کششی پایین نیز از محدودیتهای آن است. با این حال، شاهد استفاده گسترده از چدن در صنایع مختلف هستیم. این آلیاژ آهنی در مواردی مانند ساخت دیسک ترمز، لولههای آب، غلتکهای نورد، بلوک سیلندر، پیستون، لوازم آشپزخانه و... بکار گرفته میشود.
- فولاد
فولاد یکی دیگر از آلیاژهای آهنی پرکاربرد است که حدود 0.002 الی 2.1 درصد جرم آن را کربن تشکیل میدهد. درواقع، آهن و کربن از عناصر مهم موجود در فولاد هستند که مقدارشان تعیینکننده میزان سختی و مقاومت آن است. بنابراین، خواص فولاد را با تغییر درصد کربن و عناصر آلیاژی دیگر میتوان کنترل کرد. همچنین، این آلیاژ آهنی از مقاومت بالا و قیمت نسبتا پایینی برخوردار است؛ به همین جهت، در بسیاری از صنایع مهم امروزی مورداستفاده قرار میگیرد. از این صنایع میتوان به صنعت ساختمانسازی، پلسازی، خودروسازی، کشتیسازی، ساخت تجهیزات و ماشینآلات مختلف اشاره کرد.
- فولاد ضد زنگ
فولاد ضد زنگ یا فولاد زنگ نزن از دیگر آلیاژهای آهنی است که عناصر اصلی آن شامل آهن، کروم و نیکل میشود. حداقل درصد جرمی کروم موجود در آن برابر با 10.5 درصد است و درصد جرمی کربن نیز حدود 1.2 درصد برآورد میشود. این مقدار کروم در داخل فولاد از خوردگی آن جلوگیری میکند و حتی در صورتی که کمی خراشیدگی بر روی سطحش ایجاد شود میتواند خود را ترمیم و بازسازی کند. بهطورکلی، فولادهای ضد زنگ به دلیل مقاومت بالایی که در برابر خوردگی از خود نشان میدهند موردتوجه مصرفکنندگان قرار گرفتهاند. این آلیاژ آهنی مقاوم با توجه به خصوصیاتی که دارد در ساخت لوازم آشپزخانه، ابزارهای جراحی، مصالح ساختمانی، تجهیزات صنعتی موردنیاز کارخانههای مختلف و... بهکار گرفته میشود.
- فولاد نرم
فولاد نرم دارای مقدار کمی کربن است و آن را با نام فولاد کم کربن نیز میشناسند؛ مقدار کربن موجود در آن حدود 0.05 الی 0.25 درصد است. همچنین، این فولاد با بهرهگیری از آهن تولید میشود و حاوی عناصری نظیر کروم و مولیبدن است. از مشخصات بارز آن میتوان به انعطافپذیری و جوشپذیری مطلوب به دلیل داشتن کربن کم، مقاومت کششی پایین، خاصیت مغناطیسی بالا، قابلیت بازیافت و قیمت مناسب اشاره کرد. افزون بر این، فولادهای نرم در صورتی که پوششدهی نشوند ممکن است بر اثر عوامل مختلفی مانند رطوبت دچار زنگزدگی شوند. این فولاد با توجه به مشخصاتی که دارد در ساخت خودرو، مبلمان، وسایل تزیینی و... مورداستفاده قرار میگیرد.
- فولاد متوسط
حدود 30 الی 60 درصد فولاد متوسط را کربن تشکیل میدهد. این فولاد، پردازش حرارتی و برش مطلوبی دارد؛ اما در جوشکاری ضعیف است؛ به همین جهت، پیش از عملیات جوشکاری به پیش گرمایش نیاز دارد. همچنین، میزان سختی و مقاومت آن بیشتر از فولاد نرم و کم کربن است و درمقابل، میزان انعطافپذیری کمتری دارد. درضمن، فولاد متوسط را معمولا در تولید قطعات متحرک با استقامت بالا بکار میگیرند. از این قطعات میتوان به پیستونهای پمپ، کمپرسورهای هوا، چرخ دندهها، پروانههای توربین بخار، دوکهای ماشین ابزار، میل لنگ، غلتکها، ابزارهای صندلی و... اشاره کرد.
- فولاد ریخته گری
فولاد ریخته گری یکی از انواع آلیاژ آهنی دارای نیکل یا مولیبدن یا هر دوی آنها است. این آلیاژ آهنی ازنظر ظاهری روشنتر از چدن یا چدن چکشخوار بوده و از منظر تست شکستگی هم سختتر از آهن چکشخوار است. همچنین، مقاومت بالای فولاد ریختهگری در برابر سایش را مهمترین مشخصه آن میدانند که این ویژگی موردتوجه فولادسازان قرار گرفته است. به این ترتیب، افرادی که در صنعت فولادسازی فعال هستند با این فولاد مقاوم میتوانند قطعات و تجهیزات مستحکمی بسازند. این فولاد علاوه بر مقاوم بودن به راحتی جوش داده میشود. لازم به ذکر است، جوشکاری آلیاژهایی که کروم یا وانادیوم دارند به سختی انجام میگیرد.
- فولاد کم آلیاژ
فولاد کم آلیاژ که از آن با نام ریزآلیاژ نیز یاد میشود یک مدل فولاد آلیاژی است که با مقادیر کمی کربن، کروم، نیکل، منگنز، مولیبدن، سیلیکون و وانادیوم ساخته میشود. این آلیاژ فولادی مقاومت قابلقبولی در برابر خوردگی دارد؛ به همین علت، در مهمترین صنایع مورداستفاده قرار میگیرد. از صنعت ساختوساز و کشتیسازی گرفته تا صنعت نفت و لولهکشی از آن استفاده میکنند. از سایر موارد مصرف فولادهای کم آلیاژ میتوان به مخازن تحتفشار، تجهیزات خاکبرداری و سازههای فولادی اشاره کرد.
فرآیند تولید آلیاژ آهنی
تولید آلیاژ آهنی به دو روش کوره بلند و احیای مستقیم انجام میگیرد. فرآیند تولید آلیاژهای آهنی در کوره بلند یک روش قدیمی است که از قرن بیستم به بعد کمتر مورداستفاده قرار گرفت؛ در صورتی که روش احیای مستقیم همچنان در واحدهای تولیدی استفاده میشود. درکل، آلیاژهای آهن با واکنشهای کربوترمیک ساخته میشوند که شامل کمتر شدن اکسیدها با کربن (به عنوان کک) با وجود آهن است. تعدادی از آلیاژهای آهن نیز با اضافه شدن عناصر مختلف به آهن مذاب ایجاد میشوند. بهطورکلی، روشهای مختلفی برای تولید آلیاژ آهنی وجود دارد و هرتولیدکنندهای بنا بر امکانات و تمایلات خود از یک روش استفاده میکند.