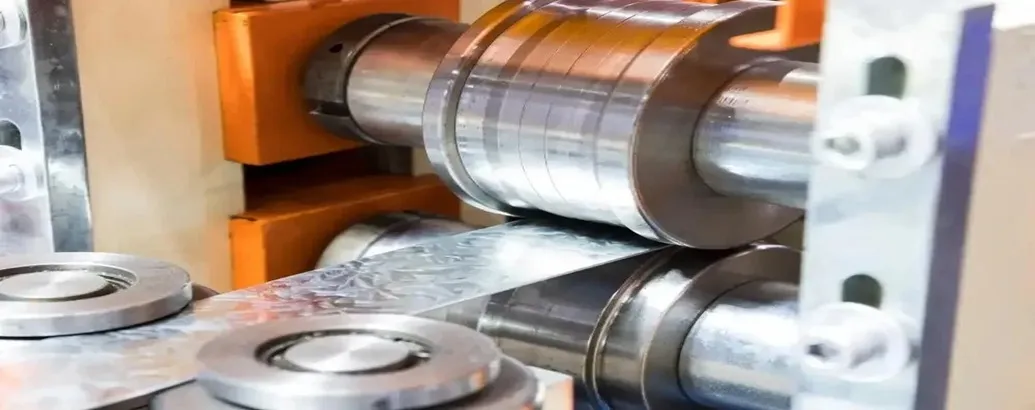
فولاد سردکار چیست؛ انواع و مشخصات آن
فولاد سردکار نوعی از فولاد است که با فرآیندهای خاصی تولید میشود که آن را از دیگر انواع فولاد متمایز میکند. به طور کلی، این فولادها در دمایی کمتر از دمای فولاد گرم کار پردازش میشوند که این امر باعث بهبود خصوصیات مکانیکی آنها مانند استحکام، سختی و بالا رفتن دقت ابعادی میشود. ویژگیهایی مانند مقاومت به سایش، انعطافپذیری در عین حفظ استحکام و تحمل تنشهای بالا، این نوع فولاد را به گزینهای ایدهآل برای صنایع مهندسی، ابزارسازی و تولید قطعات دقیق تبدیل کرده است.
این قابلیتها باعث شده که فولاد سردکار در طیف گستردهای از صنایع، از خودروسازی گرفته تا تولید قطعات قالب، ابزارآلات برش و حتی محصولات خانگی، جایگاه ویژهای پیدا کند. علاوه بر این، روش تولید آن به گونهای است که تنوع در گریدها و خواص شیمیایی و مکانیکی را ممکن میسازد و به همین دلیل توانسته در بازار جهانی نیز اهمیت زیادی پیدا کند.
فولاد سردکار چیست؟
فولاد سردکار نوعی فولاد ابزار است که برای استفاده در دماهای پایینتر از ۲۰۰ درجه سانتیگراد طراحی شده است. این نوع فولاد بهدلیل ترکیب خاصی از عناصر مانند کربن، کروم، تنگستن و منگنز، به خوبی مقاومت در برابر سایش و سختی را در شرایط کاری پایین حفظ میکند. از آنجاییکه فولاد سردکار نمیتواند سختی خود را در دماهای بالا حفظ کند؛ برای کاربردهایی که نیاز به دماهای بالا ندارند، مناسب است. درصد بالای کربن در این فولادها به افزایش مقاومت و قابلیت شکلپذیری آنها کمک میکند و بههمیندلیل این نوع فولادها در ساخت ابزارهایی که تحت سایش مکانیکی قرار میگیرند، بسیار کارآمد هستند.
در روش تولید فولاد سردکار، کنترل دقیق فرآیندهای مکانیکی و گرمایی نقش کلیدی در کیفیت نهایی محصول دارد. این فولادها معمولاً دارای سطح صافتر و تلرانسهای ابعادی بسیار دقیقتری نسبت به فولاد گرم کار هستند. همچنین، ساختار میکروسکوپی این محصولات به دلیل فرایندهای سرد شکلگیری، دارای چگالی بالاتری است که به مقاومت بیشتر در برابر سایش و خمش کمک میکند.
از دیگر ویژگیهای برجسته فولاد سردکار میتوان به قابلیت کار بیشتر روی آن پس از تولید اشاره کرد. این ویژگی باعث میشود که این نوع فولاد در تولید ابزارآلات دقیق، قطعات حساس صنعتی و محصولاتی که به تحمل فشارهای مکانیکی بالا نیاز دارند، کاربرد فراوانی داشته باشد. علاوه بر این، خواص یکنواختتر و رفتار پایدارتر این فولادها، استفاده از آنها در صنایع حساس مانند هوافضا، خودرو و ابزارسازی را افزایش داده است.
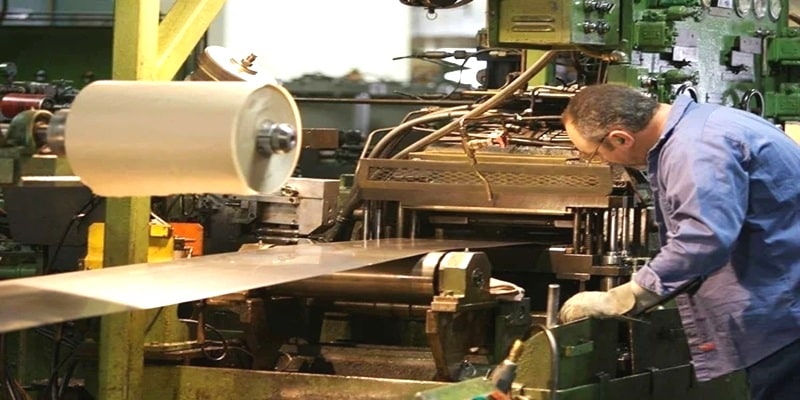
انواع دستهبندیهای فولاد سردکار
فولاد سردکار در دسته فولادهای ابزاری یا Tool Steel قرار دارد و در سه گرید اصلی دستهبندی میشود که هر کدام بر اساس روش سختکاری و کاربردهای ویژه طراحی شدهاند:
- فولاد ابزاری سختشونده با هوا (Air Hardening) یا A-Grade: این گرید بدون نیاز به کوئنچینگ سریع و با سرد کردن در هوا سخت میشود. پایداری ابعادی بالا و مقاومت به سایش از ویژگیهای بارز آن است که باعث میشود در تولید ابزارهای دقیق و قالبهای پیچیده استفاده شود.
- فولاد ابزاری سختشونده با روغن (Oil Hardening) یا O-Grade: این گرید بهصورت خاص در روغن سختکاری میشود و چقرمگی بالایی دارد. مناسب برای تولید ابزارهایی است که باید مقاومت بالایی در برابر ضربه داشته باشند.
- فولاد ابزاری نوع D (D Type) یا D-Grade: این گرید با محتوای کروم بالا طراحی شده و مقاومت فوقالعادهای در برابر سایش دارد. برای تولید ابزارهای برش، قالبهای پانچ و قطعاتی که تحت فشار زیاد قرار دارند، ایدهآل است.
گریدهای دیگر فولاد ابزارسازی که سردکار نیستند:
سایر گریدها مانند W-Grade (سختشونده با آب)، S-Grade (مقاوم به ضربه)، H-Grade (گرمکار) و گروههای خاص Special Purpose گریدهایی هستند که به دلیل روش تولید و ویژگیهای خاص، در دستهبندی فولاد سردکار قرار نمیگیرند. بنابراین، در دستهبندی دقیق، تنها سه گرید O، A و D بهعنوان فولاد سردکار شناخته میشوند. این دستهبندی هم بر اساس استانداردهای بینالمللی است و هم در جهت جلوگیری از اشتباهات رایج در برخی منابع داخلی که فولاد سردکار را در پنج یا چند دسته معرفی میکنند برای شما آورده شده است.
انواع گریدهای فولاد سردکار
فولادهای سردکار به سه دسته اصلی تقسیم میشوند که هر یک دارای ویژگیها و کاربردهای منحصربهفردی هستند. در ادامه، توضیحات این گریدها ارائه شده است:
- فولاد سختشونده با هوا (Air Hardening) یا گرید A
این نوع فولاد به دلیل محتوای بالای کروم، هنگام عملیات حرارتدهی کمترین میزان تغییر شکل را دارا است. از جمله ویژگیهای شاخص این گرید میتوان به مقاومت فوقالعاده در برابر سایش، سختی بالا و قابلیت ماشینکاری عالی اشاره کرد. این گرید معمولاً در ساخت ابزارهایی مانند قالبهای کلهزنی، سنبهها، میلههای سربی، ابزارهای برجستهکاری، چاقو و ابزارهای تراشکاری به کار گرفته میشود.
تنوع این گرید شامل مدلهایی مانند A2، A3، A4، A6، A7، A8، A9 و A10 است که هرکدام برای کاربردهای خاص طراحی شدهاند. جایگاه این فولاد در میان گریدهای D و S قرار دارد و از لحاظ عملکرد، ترکیبی از مزایای این دو گروه را ارائه میدهد.
- فولاد نوع D (D Type) یا گرید D
این گرید، به دلیل درصد بالای کربن و کروم، از مقاومت بسیار زیادی در برابر سایش برخوردار است. اگرچه این فولاد گاهی در دسته فولادهای نیمهضدزنگ قرار میگیرد، اما به دلیل تشکیل کاربیدهای کروم و کربن مقاومت به خوردگی آن نسبتاً کم است. این فولاد میتواند سختی خود را تا دمای 425 درجه سانتیگراد حفظ کند.
کاربردهای آن شامل ساخت ابزارهای پرداختکاری، ابزارهای برجستهکاری، لمینیتکاری، قالبهای سردکار، کاترها و چاقوهای برش سرد است. این گرید بهویژه در انواع D2، D3، D6 و D7 تولید میشود که در میان آنها، گرید D2 به دلیل عملکرد عالی، محبوبترین است.
- فولاد سختشونده با روغن (Oil Hardening) یا گرید O
این فولاد به دلیل فرآیند سختکاری در روغن، از مقاومت بالایی در برابر سایش برخوردار است و بهطور گسترده در کاربردهای عمومی مورد استفاده قرار میگیرد. فرآیند حرارتی این فولاد شامل حرارتدهی تا دمای 800 درجه سانتیگراد، سرد کردن در روغن و سپس حرارتدهی مجدد در دمای 200 درجه برای دستیابی به سختی و چقرمگی بهینه است.
از این گرید در تولید قطعاتی مانند دریلها، میلهها، حدیدهها، گیرههای ماشین تراش و ابزارهای رزوهکاری پیچ استفاده میشود. انواع مختلف این گرید شامل O1، O2، O6 و O7 هستند که هرکدام با توجه به نیازهای صنعتی خاص طراحی شدهاند.
کاربردهای فولاد سردکار
این نوع فولاد به دلیل مقاومت و انعطافپذیری بالا در تولید ابزارآلات، قطعات خودرو، قالبهای صنعتی و بسیاری دیگر از کاربردهای مهندسی استفاده میشود. در ادامه کاربردهای فولاد سردکار را به صورت فهرست آوردهایم:
- تولید ابزارهای برش و پانچ: بهدلیل مقاومت بالا در برابر سایش و لبپر شدن، این فولاد در ساخت ابزارهایی مانند مته، تیغه و فرز بهکار میرود.
- ساخت قالبهای صنعتی: مناسب برای قالبهای تزریق پلاستیک و قالبهای فلزی.
- تولید قطعات خودرو: استفاده در محورهای انتقال قدرت و قطعات مقاوم به ضربه.
- ساخت قطعات دقیق ماشینی: به دلیل تلرانسهای ابعادی بالا.
- صنایع هوافضا: برای تولید قطعاتی که نیاز به مقاومت در دماهای بالا دارند.
- تولید تجهیزات معدنی: استفاده در ابزارهای سنگین و مقاوم به سایش.
- ساخت قطعات سازهای: برای کاربردهایی که نیاز به استحکام کششی بالا دارند.
- تولید لولههای صنعتی: مناسب برای کاربردهایی که نیازمند انعطافپذیری بالا هستند.
- تولید ابزارهای خانگی: برای محصولاتی که نیاز به دقت و کیفیت بالا دارند.
- صنایع پزشکی: در تولید ابزارهای حساس و دقیق.
- قالب تزریق: فولاد سردکار بهدلیل سختی و پایداری ابعادی بالا، در ساخت قالبهایی استفاده میشود که باید در برابر فشار و حرارت بالا مقاوم باشند.
- نورد سرد: در غلتکهای نورد سرد، فولاد سردکار بهدلیل تحمل فشار زیاد و حفظ سطح صاف قطعه، انتخاب مناسبی است.
- اجزای ماشینآلات: قطعاتی مانند چرخدنده و شفت، برای حفظ دقت عملکرد در شرایط اصطکاک بالا از فولاد سردکار ساخته میشوند.
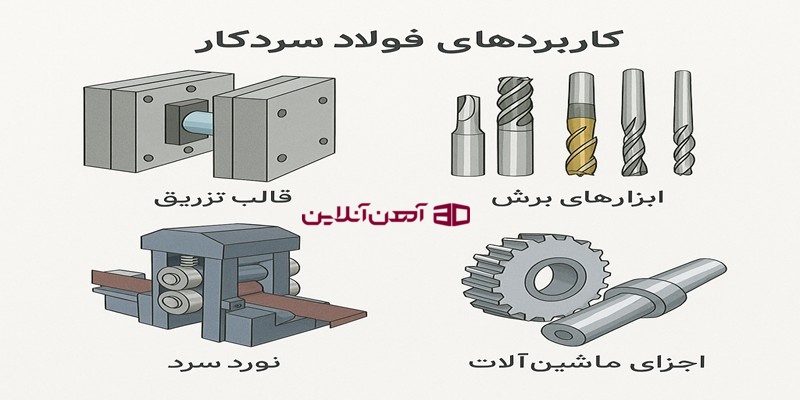
مشخصات فولاد سردکار
فولادهای سردکار با استانداردهای دقیق و جامعی توصیف میشوند که تضمینکننده کیفیت و عملکرد مناسب آنها در کاربردهای صنعتی حساس هستند. یکی از این استانداردها DIN 17350 است که در آلمان تدوین شده و مشخصات مکانیکی و شیمیایی فولادهای ابزارسازی سردکار را بهطور دقیق تعریف میکند. این استاندارد شامل پارامترهایی مانند سختی، استحکام کششی و ترکیبات آلیاژی است.
ASTM A681 استانداردی آمریکایی است که فولادهای ابزارسازی را بر اساس ویژگیهایی نظیر مقاومت در برابر سایش و قابلیت سختکاری دستهبندی میکند. این استاندارد مشخصات شیمیایی دقیقی مانند درصد کروم، کربن و سایر عناصر آلیاژی را ارائه میدهد.
از طرفی، ISO 4957 بهعنوان یک استاندارد بینالمللی، مشخصات کامل فولادهای ابزارسازی را پوشش میدهد. این استاندارد به تعریف ویژگیهایی نظیر سختیپذیری، چقرمگی و رفتار مکانیکی فولادها پرداخته و برای تولید قطعاتی که در صنایع حساس مانند هوافضا و خودرو استفاده میشوند ایدهآل است. برای مثال، این استاندارد کیفیت فرآیندهای نورد و سختکاری را تضمین میکند تا خواص مکانیکی مطلوب به دست آید.
در ژاپن، JIS G4404 استانداردی جامع برای فولادهای ابزارسازی مانند SKD11 (معادل D2) و SKS3 (معادل O1) ارائه میدهد. این استاندارد مشخصات ابعادی دقیق و رفتار مکانیکی فولادها را تحت شرایط متنوع توصیف میکند. این گریدها در ابزارهای صنعتی پیشرفته و قالبهای تخصصی کاربرد گسترده دارند.
همچنین، استانداردها مقادیر خاصی برای سختی بر حسب مقیاس راکول (HRC) تعریف میکنند که معمولاً در محدوده 50 تا 64 HRC قرار دارد. ترکیب شیمیایی نیز شامل درصد دقیق عناصر آلیاژی نظیر کروم، مولیبدن و وانادیوم است. علاوه بر این، مقادیر حداقل استحکام کششی و تسلیم نیز در استانداردها تعیین شده که برای تولید قطعات حساس الزامی است.
این استانداردها تضمین میکنند که فولاد سردکار با کیفیت بالا و قابلیت اطمینان، برای صنایع حساس و پیشرفته تولید شود. جزئیات هر گرید به کمک این استانداردها بهطور دقیق مشخص میشود تا نیازهای مختلف صنعتی را برآورده سازد.
مزایای استفاده از فولاد سردکار
فولاد سردکار همانطور که تا اینجای مقاله توضیح دادهایم، مزایای بسیار زیادی در زمینه مشخصات فیزیکی دارد که باعث شده کاربردهای آن نیز گسترده باشد. در ادامه به برخی از مزایای این محصولات فولادی اشاره میکنیم:
- انعطافپذیری بالا برای تولید قطعات متنوع
- هزینه تولید نسبتاً پایین در مقایسه با دیگر آلیاژها
- استحکام کششی بالا برای کاربردهای حساس
- مقاومت به سایش و ضربه در محیطهای صنعتی سخت
- مقاومت به خوردگی برای استفاده در شرایط محیطی دشوار
- دوام و کارایی طولانیمدت با حداقل خرابی
- تلرانس ابعادی بالا که نیاز به ماشینکاری را کاهش میدهد
- سطح صاف و براق برای کاربردهای زیباییشناسانه
- سازگاری با استانداردهای بینالمللی در صنایع مختلف
- مقاومت حرارتی در گریدهایی که تحت دمای بالا کار میکنند
کارخانههای تولید کننده فولاد سردکار
در ایران و جهان، کارخانههای متعددی به تولید این نوع فولاد مشغول هستند. این کارخانهها با بهرهگیری از فناوریهای پیشرفته، فولادهایی با کیفیت بالا تولید میکنند. فهرست زیر نام برخی از مهمترین کارخانههایی است که در ایران این نوع فولاد را تولید میکنند:
- مجتمع فولاد مبارکه اصفهان
- ذوب آهن اصفهان
- فولاد خوزستان
- فولاد آلیاژی ایران
- مجتمع فولاد خراسان
- صنایع فولاد هفت الماس
- فولاد امیرکبیر خزر
- مجتمع فولاد ظفر بناب
- فولاد البرز تاکستان
- فولاد سیرجان حدید جنوب
عوامل تأثیرگذار بر قیمت فولاد سردکار
قیمت فولاد سردکار به عوامل مختلفی بستگی دارد که هر کدام میتوانند تأثیر قابلتوجهی بر تغییرات آن داشته باشند. یکی از مهمترین عوامل، نوسانات قیمت مواد اولیه مانند سنگ آهن و کک است که پایه تولید فولاد را تشکیل میدهند. تغییرات نرخ ارز نیز بهویژه در کشورهایی که به واردات مواد اولیه یا صادرات محصولات فولادی وابسته هستند، نقش مهمی در تعیین قیمت دارد. از سوی دیگر، میزان تقاضا در بازار، بهویژه از سمت صنایع مصرفکننده نظیر خودروسازی، ساختوساز و تولید ابزار، تأثیر مستقیمی بر قیمت دارد. شرایط اقتصادی جهانی و عوامل کلان مانند رکود یا رونق بازار نیز میتوانند بر قیمتگذاری این محصول تأثیرگذار باشند.
هزینه انرژی که برای تولید فولاد مصرف میشود، بهدلیل مصرف بالای انرژی در این فرآیند، یکی دیگر از عوامل کلیدی است. علاوه بر این، میزان عرضه فولاد و توان تولید کارخانهها، نقشی تعیینکننده در تعادل بازار ایفا میکند. هزینههای حملونقل، بهویژه در مواردی که نیاز به جابهجایی در مسافتهای طولانی وجود دارد، میتواند بهطور مستقیم قیمت را افزایش دهد. قوانین و تعرفههای گمرکی نیز، بسته به سیاستهای واردات و صادرات، به کنترل یا افزایش هزینههای تولید و عرضه کمک میکنند. کیفیت و استاندارد فولاد تولیدی نیز بر اساس گرید و ترکیبات خاص، عاملی است که میتواند قیمت را تغییر دهد. در نهایت، فناوریهای بهکار رفته در فرآیند تولید فولاد سردکار، نقش مهمی در کاهش یا افزایش هزینهها و در نتیجه قیمت نهایی دارند. تمامی این عوامل به صورت همزمان و با تعامل یکدیگر، قیمت فولاد سردکار را در بازار تعیین میکنند.