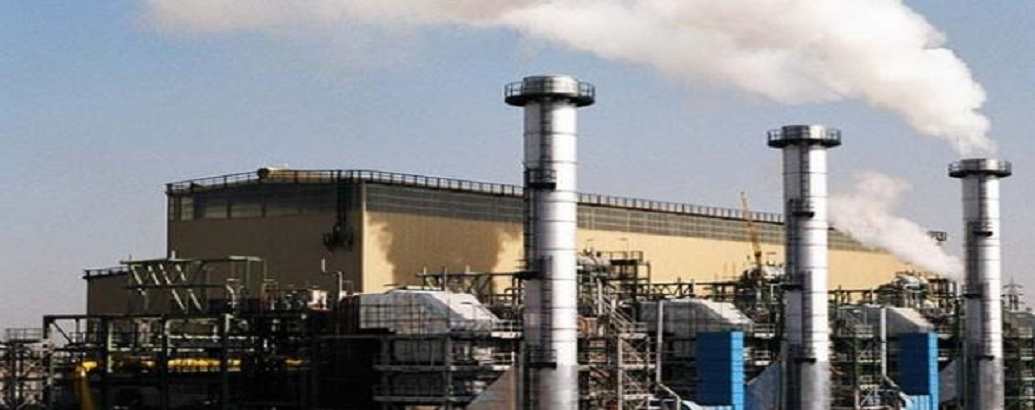
300 راهکار برای کاهش مصرف انرژی در زنجیره فولاد
یک کارشناس صنعت فولاد گفت: انرژی موردنیاز برای ذوب مواد آهندار در کورههای قوس الکتریکی از توان الکتریکی (تقریبا ۶۰ درصد) و انرژی حاصل از فرآیندهای شیمیایی حاصل از ترکیب اکسیژن و کربن تامین میشود، ضمن اینکه سوزاندن کربن در کوره سبب تولید گاز دیاکسیدکربن میشود.
حسن طاهری در گفتگویی با تاکید بر این موضوع که تولید فولاد سبز یک ضرورت است و در فرآیند تولید فولاد باید منشأ آلودگیها را پیدا کرد، گفت:
آلایندگی در صنعت فولاد بیشتر مربوط به ذوب است و واحدهای نورد به علت استفاده از گاز طبیعی آلایندگی کمتری دارند. در فرآیند تولید فولادخام حجم بالایی گاز دیاکسیدکربن به عنوان یک گاز گلخانهای تولید میشود. به ازای تولید هر تن فولاد خام ۶ تا ۱۸ کیلوگرم گاز دیاکسیدکربن تولید میشود و نرخ تولید آن به نوع و ترکیب بار کوره بستگی دارد. قیمت آهن کیلویی و تولید آن، به دلیل آلودگی بالایی که دارد، همواره دچار نوسان است.
طاهری یادآور شد: کارخانههای فولاد به دو صورت مستقیم و غیرمستقیم سبب تولید آلایندگی میشوند. مستقیم از طریق تولید گاز دیاکسیدکربن کارخانههای ذوب و غیرمستقیم از طریق نیروگاههای برق این گاز آلاینده تولید میشود. جمع این دو آلایندگی را اثر محیط زیستی کارخانه فولاد مینامند.
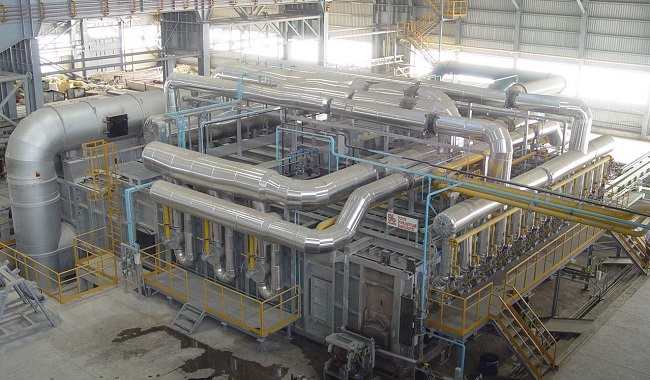
این کارشناس حوزه فولاد با اشاره به شارژ کورههایی که سبب آلایندگی میشوند، عنوان کرد: کمترین میزان آلایندگی مربوط به کورههایی است که تمام شارژ آنها از آهن قراضه تشکیل شده است. در این کورهها به ازای هر تن فولاد خام 6/2 کیلوگرم گاز دیاکسیدکربن تولید میشود. اگر بار کوره از ۸۰ درصد آهن اسفنجی سرد تشکیل شده باشد به ازای هر تن فولاد خام ۱/ ۱۸ کیلوگرم گاز دیاکسیدکربن تولید میشود که سه برابر میزان مربوط به کورهای با ۱۰۰ درصد شارژ قراضه است. از سوی دیگر، آهن اسفنجی حدود ۱٫۵ تا ۲ درصد کربن دارد که سبب تولید گاز دیاکسیدکربن میشود، بنابراین اگر در بار کوره نسبت قراضه به آهن اسفنجی به ۷۰ به ۳۰ درصد برسد، میزان آلایندگی کورههای ذوب بسیار کاهش پیدا میکند. برای کاهش آلودگی در تولید فولاد، راهکارهایی وجود دارد.
۲۰۰ تا ۳۰۰ راهکار برای کاهش مصرف انرژی در زنجیره فولاد
وی در پاسخ به این پرسش که آیا راهکارهای مطرحشده نیازمند هزینه بالاست؟ گفت: میتوان ۲۰۰ تا ۳۰۰ راهکار برای کاهش مصرف انرژی در زنجیره فولاد ارائه داد. بسیاری از این روشها به مدیریت بهرهبرداری از کوره مرتبط هستند و به سرمایهگذاری چندانی نیاز ندارند. برای نمونه در کوره قوس میتوان طول قوس را زیادتر کرد و مصرف انرژی را کاهش داد. یا در ذوبگیری فاصله دو زمان ذوبگیری را تا حد ممکن کوتاه کرد، چراکه توقف کار هزینه انرژی را افزایش میدهد. همچنین در کوره قوس، پاتیلی و ریختهگری مداوم بهرهبرداری از کوره را باید به حداکثر و زمان توقف را به حداقل رساند، چراکه تولید مداوم میزان مصرف انرژی را کاهش میدهد. چنانچه در تولید این مقاطع، میزان کمتری آلودگی ایجاد شود، در قیمت آهن اثر گذار خواهد بود.