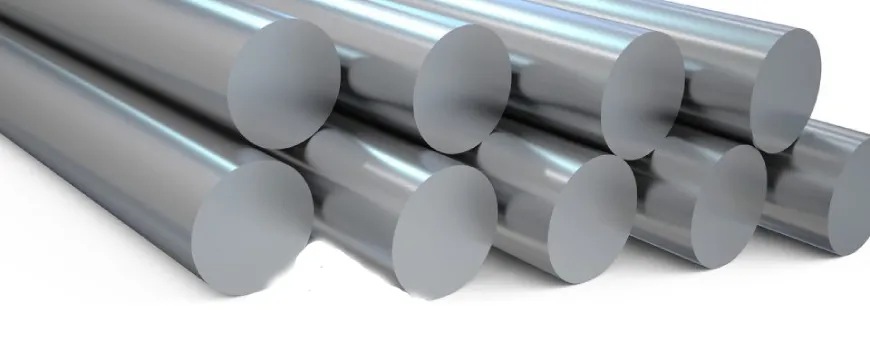
میلگرد آلیاژی چیست و انواع آن
به طور کلی از میلگردها برای بسیاری از صنایع مختلف از جمله صنعت ساختمانسازی استفاده میشود. میلگردها از جمله مقاطع فولادی هستند که برای کاربری بیشتر، با ترکیباتی خاص به آهن اضافه میشوند و در نهایت به صورت آلیاژهای آهن در قالبها، انواع و کاربریهای مختلف روانه بازار خواهند شد. میلگرد آلیاژی یکی از همین مقاطع فولادی است که با هدف بالابردن میزان استحکام و مقاومت سازهها ساخته میشوند و از سختی بسیار بالاتری نسبت به دیگر فلزها برخوردار هستند. برای اینکه با میلگرد آلیاژی به صورت کامل آشنا شویم، لازم است تا آگاهی مختصری در رابطه با آلیاژها داشته باشیم تا بدانیم این نوع میلگردها با چه نوع ساختاری تولید میشوند.
آشنایی با آلیاژ فولادی
آلیاژها در حالت استاندارد از ترکیب یک، دو یا چند فلز مختلف به وجود میآیند و همانطور که گفتیم از سختی و مقاومت بسیار بالاتری نسبت به دیگر فلزها بهرهمند میشوند. برای مثال یک آلیاژ که از ترکیب مس و روی ساخته میشود، مقاومت بسیار بالاتری نسب به یک فلز مسی دارد که تنها از یک ساختار تشکیل شده است. اواضاع در رابطه با یک میلگرد آلیاژی هم همینطور است؛ میلگردها شامل 2 نوع آلیاژی و غیر آلیاژی هستند. میلگردهای آلیاژی از ترکیب فولادهای آلیاژی ساخته میشوند و انواعی مثل میلگرد St52 دارند. اما نحوه ساخت این میلگرد چگونه است و چند نوع از این نوع میلگردهای آلیاژی در بازار وجود دارد؟ مهمترین مولفههای میلگردهای آلیاژی مقاومت بسیار بالای آن در برابر فشار و حرارت بسیار بالاست. همین ویژگیهای مهم باعث شدهاند تا کاربرد میلگردهای آلیاژی در صنایع مختلف مورد استفاده قرار بگیرند. اما میلگردهای آلیاژی از چند درصد آلیاژ ساخته میشوند و تفاوت آنها با میلگردهای غیر آلیاژی در چه چیز یا چیزهایی است؟
میلگرد آلیاژی چیست؟
میلگرد آلیاژی از جمله مقاطع فلزی است که با ترکیب کربن و 7 عنصر مختلف از جمله تنگستن، منگنز و نیکل به دست میآید. میلگردهای آلیاژی از طریق 2 روش مرسوم ترمکس و آلیاژسازی تولید میشوند که در این بین، روش ترمکس مقرون به صرفهتر است. بسته به نسبت این عناصر، میلگردهای آلیاژی ویژگیها و کاربردهای متنوعی خواهند داشت. البته ناگقته نماند که میلگرد آلیاژی تولیدشده توسط روش آلیاژسازی از مقاومت و ضخامت بسیار بیشتر برخوردار هستند و میتوان از آنها برای ساختن منازل در مناطق زلزلهخیز به خوبی استفاده کرد.
فولاد به کار رفته در میلگرد آلیاژی
همانطور که گفته بودیم، میلگردهای فولادی به 2 نوع میلگردهای آلیاژی و میلگردهای غیر آلیاژی تقسیم میشوند. اصلیترین تفاوت این 2 نوع میلگرد هم به فولادهای به کار رفته در ساختار هرکدام آنها مربوط میشود. برای مثال فولادهای آلیاژی برای ساختن میلگردهای آلیاژی به کار گرفته میشوند و معمولاً به تولید میلگردهای ساده منجر میشوند. در عوض، فولادهای غیر آلیاژی برای ساختن میلگردهای آجدار به کار گرفته میشوند و ساختاری متفاوتتر از میلگردهای آلیاژی دارند. میلگردهای آلیاژی موجود در بازار هماکنون از نوع Mo40، ST52 و ST57 هستند. بدیهی است که هرکدام از این میلگردها، از کاربردهای خاصی بهرهمند شدهاند و از هرکدام آنها برای ساخت یک سازه خاص استفاده میشود.
این نوع از مقاطع فولادی با اضافه شدن فولاد آلیاژی و شمش تولیدی در عملیات نورد در قالب میلگردهای آلیاژی تولید میشوند و در نهایت برای سرد کردن، آنها را در محیط آزاد قرار میدهند تا به آرامی خنک شوند تا در بازار آهنآلات به فروش برسند. پروسه سرد شدن میلگردهای آلیاژی تا قسمت مرکزی و سطح میلگرد از ویژگیهای شیمیایی و مکانیکی یکسان و یکنواختی بهرهمند شوند و در نهایت، استحکام و مقاومت بسیار بالایی را برای سازههای مختلف به ارمغان بیاورند.
میلگرد آلیاژی در صنایع مختلفی از جمله ساختمانسازی مورد استفاده قرار میگیرد. این نوع از مقاطع فولادی به دلیل بهرهمندی از ساختار مقاوم و مستحکم، بهترین گزینه برای به کارگیری در ساختمان منازلی است که در مناطق زلزلهخیر احداث میشوند.
معرفی میلگرد آلیاژی ST52
معروفترین و کاربردیترین میلگرد از انواع میلگردهای آلیاژی، میلگرد ST52 است که به دلیل استحکام بسیار بالا، در صنایع پرخطر از جمله ماشینسازی مورد استفاده قرار میگیرد. از این میلگرد همچنین در صنایع دیگر از جمله ریلسازی و ساخت شاسی و دیگر قطعات مهم خودروهای سنگین استفاده میشود.
میلگرد ST52 معمولاً در شاخههای 6 تا 12 متری در قطرهای 20 تا 800 میلیمتری ارائه و عرضه میشوند و میتوان آنها را در بازار آهنآلات ایران به راحتی تهیه کرد.
میلگردهای آلیاژی موجود در بازار ایران و جهان از 2 روش ساخت ترمکس و آلیاژسازی با درصد آلیاژ پایین 8 درصد و بالای 8 درصد تولید و عرضه میشوند. برای ساختن میلگردهای آلیاژی معمولاً از 7 نوع آلیاژ استفاده میشود؛ این 7 نوع آلیاژ شامل انواع زیر هستند:
- آلیاژ کروم دار
- آلیاژ وانادیم دار
- آلیاژ تنگستن دار
- آلیاژ منگنز دار
- آلیاژ کبالت دار
- آلیاژ نیکل دار
- آلیاژ مولیبیدن دار
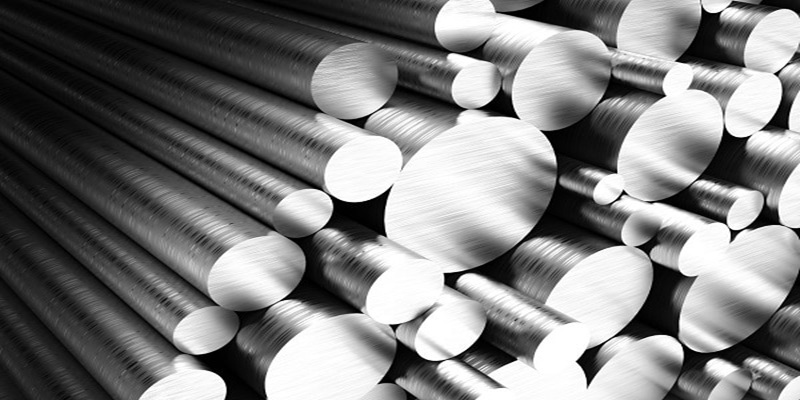
بررسی 2 روش تولید میلگرد آلیاژی
همانطور که گفتیم، میلگردهای آلیاژی از 2 روش ترمکس و آلیاژسازی ساخته میشوند؛ اما کدامیک از روشها مقرون به صرفه است و هرکدام از آنها چگونه به تولید این نوع میلگردها منجر میشوند. ما سعی کردیم تا در این بخش، به صورت کامل و تخصصی هرکدام از این روشها را زیر ذرهبین ببریم و عملیات آنها را به صورت ساده توضیح دهیم:
- تولید میلگردهای آلیاژی به روش ترمکس: روش ترمکس در مقام مقایسه با روش آلیاژی سازی، کمهزینهتر و به اصطلاح مقرون به صرفه است. در روش ترمکس، میلگرد آلیاژی پس از پروسه نورد گرم، به وسیله آب و نمک وارد مرحله خنکسازی میشود. با این روش، دمای میلگرد پایین میآید و مرکز آن همچنان داغ باقی میماند. در نهایت، حرارت و انرژی گرمایی به صورت طبیعی از قسمت مرکزی به سطوح انتقال مییابد و مشخصات فنی میلگرد دستخوش تغییرات میشود.
- روش آلیاژسازی: همانطور که از اسم این روش پیداست، فولاد به کار رفته در میلگرد آلیاژی در همان ابتدا با ترکیب فروآلیاژها تولید میشود و به تولید میلگرد منجر خواهد شد. در این پروسه، شمش فولادی مورد نظر با استفاده از روش نورد گرم در قالب میلگرد بیرون میآید و پروسه خنکسازی را به تدریج طی میکند.
مزایا و معایب روشهای ترمکس و آلیاژسازی
انتخاب روش تولید میلگرد تأثیر مستقیمی بر مقاومت، شکلپذیری و استحکام نهایی محصول دارد. دو روش ترمکس و آلیاژسازی از رایجترین فرآیندهای تولید میلگرد هستند که هرکدام مزایا و معایب خاص خود را دارند. روش ترمکس به دلیل فرآیند خنککاری سریع، میلگردی با شکلپذیری بالا و مقاومت کششی مناسب تولید میکند و گزینهای مناسب برای مناطق زلزلهخیز محسوب میشود. اما این میلگردها معمولاً نازکتر بوده و نسبت به میلگردهای آلیاژی مقاومت کمتری در برابر تنشهای شدید دارند.
در مقابل، روش آلیاژسازی به دلیل ترکیب فلزات مختلف، میلگردی با ضخامت بیشتر، مقاومت بالا و توزیع یکنواخت استحکام در سطوح داخلی و خارجی ارائه میدهد. این میلگردها در برابر ضربه و فشار عملکرد بهتری دارند، اما فرآیند تولید آنها به کربن بیشتری نیاز دارد و هزینه بالاتری نیز در بر خواهد داشت. در انتخاب بین این دو روش، باید نوع کاربری، شرایط محیطی و الزامات ایمنی سازه را مدنظر قرار داد تا بهترین گزینه بر اساس نیاز پروژه انتخاب شود.
مزایا روش ترمکس | معایب روش ترمکس | مزایا روش آلیاژسازی | معایب روش آلیاژسازی |
افزایش مقامت | نازک بودن میلگرد | ایجاد مقاومت یکسان | هزینه بسیار بالای پروسه |
شکلپذیری بالا | میزان سختی کمتر | گزینه مناسب برای | نیازمند زمان به |
انعطافپذیری | مقاومت به مراتب | ضخامت بیشتر | نیاز به کربن بیشتر |
تفاوت اصلی بین میلگرد غیر آلیاژی با میلگرد آلیاژی چیست؟
مهمترین و اساسیترین تفاوت بین میلگردهای آلیاژی با میلگردهای غیر آلیاژی در میزان کربن به کار رفته در آنها، پروسه ذوب و میزان مقاومت آنها در برابر خوردگی است. بدیهی است که میلگردهای آلیاژی با توجه به ساختار خود از مقاومت بسیار بالاتری نسبت به میلگردهای غیر آلیاژی برخوردار هستند و میتوانند در برابر خوردگی و سایر آسیبها ایستادگی کنند.
معرفی انواع میلگردهای آلیاژی
در مطالب ابتدایی این مقاله، با 7 نوع از انواع میلگرد آلیاژی آشنا شدیم و دانستیم که هرکدام آنها از یک عنصر فلزی خاص مثل تنگستن، وانادیون یا منگنز برخوردار شدهاند. ما تصمیم گرفتهایم تا در این بخش، هرکدام از این 7 میلگرد را به صورت مختصر و مفید معرفی کنیم.
- میلگرد کروم دار: این نوع از انواع میلگردهای آلیاژی علاوه بر میزان قابل توجه کربن، دارای عنصر کروم هم در ساختار خود است. فلز کروم باعث ایجاد خاصیت زد زنگ در میلگرد آلیاژی میشود و میتواند مقاومت این مقطع فولادی را بیش از پیش افزایش دهد.
- میلگرد وانادیوم دار: عنصر وانادیوم به لطف ساختار ریز و بافت انعطافپذیری که دارد، اجازه بزرگ شدن ساختار فولاد را صادر نمیکند. استفاده از وانادیوم در مقادیر و درصدهای بالا به افزایش استحکام و سختی میلگردهای آلیاژی منجر میشود.
- میلگرد تنگستن دار: وجود عنصر تنگستن باعث حفظ ثبات شیمیایی در ساختار میلگرد آلیاژی میشود؛ همین قابلیت باعث میشود تا سختی و استحکام میلگرد افزایش بیابد و از آن برای ساخت مته، تیغه و ابزار اینچنینی استفاده شود.
- میلگرد منگنز دار: منگنز یکی از پایههای قابلیت شکلپذیری در میلگردهای آلیاژی است؛ این ویژگی به دلیل خصوصیت عنصر منگنز است که از تشکیل ذرات موسوم به آستنیت (Austenite) در میلگرد جلوگیری میکند.
- میلگرد کبالت دار: میلگردهای کبالت دار معمولاً از سختی و مقاومت مطلوبی برخوردار نیستند و برای افزایش سطح مقاومت و سختی آنها مقداری تنگستن به آنها اضافه میکنند.
- میلگرد نیکل دار: عنصر نیکل یکی از عواملی است که باعث افزایش سختی و شکلپذیری در میلگرد آلیاژی میشود. همچنین جالب است بدانید که اضافه شدن حدود 35 درصد عنصر نیکل به میلگردهای آلیاژی باعث افزایش مقاومت آنها در برابر خوردگی و اکسید آهن میشود. از میلگرد آلیاژی نیکل دار برای ساختن مفتول ورقهای آلیاژی استفاده میشود و به دلیل انعطافپذیری بالای آن میتوان آن را در صنایع بسیاری به کار گرفت.
- میلگرد مولیبیدن دار: با اضافه شدن مقدار 0.2 تا 0.5 درصد مولیبیدن در میلگردهای آلیاژی، میزان مقاومت آنها در برابر خوردگی افزایش مییابد و میتوان روی خواص مقاومتی آن حساب ویژهای باز کرد.