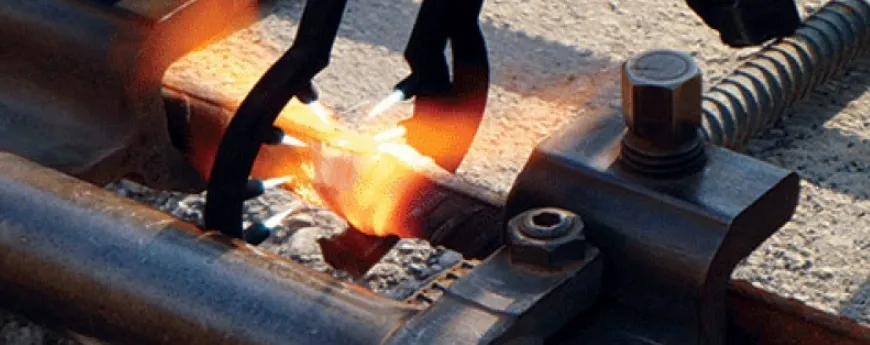
فورجینگ میلگرد چیست؛ اجرای فورجینگ میلگرد
عملیات فورجینگ میلگرد، یکی از قدیمیترین روشها برای اتصال میلگردها است. این روش نسبتا ساده اما حساس بوده و نیاز به تجربه و دانش کافی دارد. فورجینگ (Forging)، به عملیاتی گفته میشود که طی آن دو میلگرد آنقدر حرارت میبینند که در ابتدا به حالت خمیری درآمده و سپس میتوانند تحتفشار بههم پیوند بخورند.
در این مقاله ضمن تعریف تجربی و علمی فورجینگ به معرفی ابزارها و دستگاههای موردنیاز برای اجرای فورجینگ و شرح خود این عملیات میپردازیم. ازآنجاکه این روش حساسیتهای خاص خودش را دارد، نکاتی را هم درباره کیفیت و اصول انجام این فرآیند مطرح خواهیم کرد. در پایان نیز روشهای مرسوم برای حصول اطمینان از کیفیت جوش حاصلشده را شرح میدهیم. در پایان این مقاله دیدی جامع نسبت به این روش، مزایا و حساسیتهای آن به دست خواهید آورد. پس تا پایان با ما همراه باشید.
فورجینگ میلگرد چیست؟
تکنولوژی جوشکاری فورجینگ سر به سر میلگرد (Forging) در سال 1952 میلادی با هدف بهکارگیری در صنعت حملونقل ریلی ابداع و توسعه یافت. این روش که ابتدا برای اتصال ریلهای راهآهن به کار میرفت، بهتدریج با پیشرفت فناوری و نیاز به استحکام بیشتر در سازههای مختلف، وارد حوزه ساختوساز شد. یکی از روشهای پیشرفته و کاربردی در اتصال میلگردها، جوشکاری سر به سر یا فورجینگ (Forging) است. این تکنیک به عنوان یکی از زیرمجموعههای جوشکاری گازی (اکسی-استیلن) شناخته میشود که در آن، گرمای حاصل از احتراق گاز به همراه فشار هیدرولیکی کنترلشده، منجر به اتصال کامل و پیوسته دو سر میلگرد میشود.
با رشد روزافزون شهرها، افزایش ارتفاع ساختمانها و گسترش پروژههای عمرانی، اهمیت مقاومسازی سازهها بیش از پیش نمایان شد. در این میان، جوش فورجینگ سر به سر میلگرد به دلیل ضریب ایمنی بالا، کاهش مصرف مصالح اضافی، افزایش استحکام اتصالات و کاهش هزینههای اجرایی، بهعنوان یک روش نوین و کارآمد مورد توجه مهندسان و پیمانکاران قرار گرفت.
این تکنولوژی با ایجاد یک پیوند مولکولی قوی بین میلگردها، نقاط ضعف احتمالی ناشی از روشهای سنتی اتصال مانند اورلپ یا کوپلینگ میلگرد را برطرف کرده و عملکرد بهتری در برابر نیروهای کششی و فشاری ارائه میدهد. به همین دلیل، امروزه در بسیاری از پروژههای عمرانی، از ساختمانهای مسکونی گرفته تا پلها و سدها، این روش جایگزین سایر روشهای اتصال میلگرد شده است.
ابزار مورد نیاز برای اجرای فورجینگ
برای انجام فورجینگ میلگرد به ابزارها و دستگاههای زیر نیاز داریم:
دستگاه جوش
- کپسول اکسیژن و کنترلکننده آن
- کپسول گاز استیلن و کنترلکننده آن
- نازل اکسیژن
- نازل استیلن
- مشعل
دستگاه کمپرسور
- پمپ فشار
- پدال پمپ
- نازل فشار هیدرولیکی
- سیلندر RAM
- سیلندر خارجی
- گیرههای نگهدارنده میله
- دستگاه برش
این دستگاه بهمنظور صاف و یکدست کردن مقاطع میلگردها قبل از جوشکاری استفاده میشود. برش لبههای میلگرد سبب میشود که هرگونه زنگزدگی، لهشدگی، ناصافی و خوردگی از بین رفته و ضمانت کیفیت عملیات بالا برود.
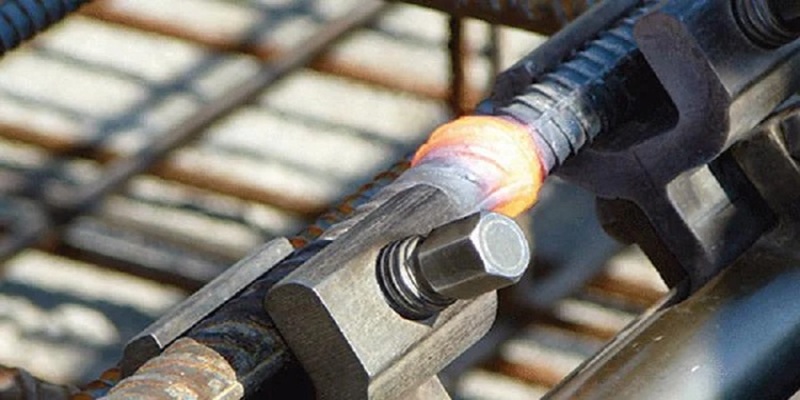
روش انجام عملیات فورجینگ میلگرد
در این روش پسازاینکه دو سر میلگردها توسط دستگاه برش صاف و یکدست شد، توسط گیرههای نگهدارنده در یک راستا قرار میگیرند. میلههای نگهدارنده، خود شامل بخشهای ثابت، متحرک و انواع پیچها هستند که بهوسیله آنها میتوان زاویه قرارگیری دو میلگرد در برابر یکدیگر را تنظیم کرد.
در مرحله بعد شیر دو کپسول اکسیژن و استیلن باز شده و گازها در تناسبی که باید رعایت شود با یکدیگر ترکیب شده و هرکدام وارد نازلهای خود میشوند. فشار هرکدام از گازها را میتوان توسط فشارسنجهای دو کپسول تنظیم کرد.
لازم به ذکر است که هر کپسول دو فشارسنج دارد. یکی از آنها فشار گاز خارجشده و دیگری فشار داخل کپسول را نشان میدهد. بدیهی است که رابطه این دو با یکدیگر معکوس است. مقادیر لازم فشار گاز خروجی برای هرکدام از این دو گاز را در بخش بعدی شرح خواهیم داد.
این دو نازل درنهایت با یکدیگر یکی میشوند و یک گاز خروجی ترکیبی وارد شیلنگ مشعل میشود. با استفاده از شیرهای تنظیم روی مشعل نیز میتوان تناسب دو گاز را تغییر داد. معمولا از دو رنگ متفاوت برای شیرهای تنظیمی هر یک از دو گاز استفاده میشود. نازل، شعله را بهصورت حلقوی روی میلگردها میگیرد که باعث میشود آنها بهصورت یکنواخت گرم شوند.
در مرحله بعد و پس از نرم شدن میلگردها بهاندازه لازم، دستگاه کمپرسور وارد عمل میشود. این دستگاه با فشار هیدرولیکی خود دو میله را در هم فرو میبرد که به آن عملیات فورجینگ میگویند. فشار کمپرسور را میتوان با استفاده از شیرهای تنظیم فشار روی آن بهصورت دستی کنترل کرد.
عملیات جوش فورجینگ
برای اجرای عملیات جوش فورجینگ میلگرد، علاوه بر خود میلگردها به ابزار و دستگاههایی نیاز داریم. این عملیات شامل سه مرحله است که آنها را در این بخش شرح خواهیم داد.
- تمیز کردن مقاطع میلگرد
بهمنظور به حداقل رساندن احتمال بهوجود آمدن اکسیداسیون در بافت جوش، لازم است که قبل از شروع بهکار بهخوبی سطح آنها را از هرگونه زنگزدگی، خوردگی و مواد دیگر پاک کنیم. بهاینمنظور، میتوان مقاطع را با انواع مواد شوینده استاندارد، شستشو داد که از هرگونه چربی زدوده شوند.
بااینحال، مطمئنترین روش این است که سطح مقطع بسیار کوچکی از هر دو میلگرد را به استفاده از دستگاه برش بهصورت صاف و یکدست ببریم. میتوان گفت این مرحله تنها مرحلهای است که در طول فرآیند، منجر به تولید ضایعاتی هرچند اندک میشود. لازم بهذکر است که برش را باید تنها کمی قبل از شروع مرحله بعد که عملیات حرارتی است، انجام دهیم. درصورتیکه فاصله زمانی این مرحله و مرحله بعدی زیاد شود، ممکن است سطح مقطع میلگرد مجدداً اکسید شود یا بههرنحو آلودگیهایی به خود جذب نماید.
- مرحله حرارت دهی
در این مرحله، دو میلگرد با استفاده از گیرههای نگهدارنده، درست روبهروی یکدیگر قرار میگیرند. این میلهها در ابتدا متحرک بوده که پس از تنظیم موقعیت میلهها بهصورت دلخواه و محکم کردن بست و پیچهای آن، ثابت شده و آماده حرارتدهی میشوند.
دو کپسول پر از گاز اکسیژن و اکسیاستیلن در مرحله بعد وارد فرآیند میشوند. این دو کپسول دارای نازلهایی هستند که گاز داخل آنها را به سمت مشعل هدایت میکند. درواقع، دو نازلی که هرکدام از یک کپسول میآیند، در میانه راه با هم یکی شده و توسط یک شیلنگ به مشعل میرسند.
روی هرکدام از این کپسولها تنظیمکنندههایی وجود دارد که بهوسیله آنها میتوان، فشار آنها را تنظیم کرد. بارومتر روی هرکدام از کپسولها، دو عدد را بهعنوان فشار نشان میدهد. یکی از این اعداد، فشار داخل کپسول و دیگری فشار گاز واردشده به نازل است. هرکدام از این اعداد با یک رنگ نشان داده میشوند. آنچه برای ما بیشتر مهم است، فشار گاز خارجشده از هر کپسول است.
طبق تجربه و استانداردهای بینالمللی فشار گاز اکسیژن باید بین 5 تا 7 و فشار گاز اکسیاستیلن باید روی 0.5 بار باشد.
پس از ترکیب دو گاز در نازل مشعل، عملیات حرارتی شروع میشود. روی خود مشعل نیز تنظیمکنندههایی برای تنظیم میزان ورود هر گاز، وجود دارد. معمولاً اجراکنندگان حرفهای از رنگ شعله متوجه میشوند که ترکیب دو گاز در وضعیت درستی قرار دارد یا خیر.
دمای لازم برای خمیر شدن میلگردهای فولادی، بین 1200 تا 1300 سانتیگراد است. حرارت شعله باید بهاندازهای باشد که این روند، نه زیاد کند انجام شود و نه با سرعت بیشازحد. در غیر این صورت، ساختار جوش ایجادشده شکننده خواهد بود.
زمان حرارت دهی، رابطه مستقیمی با قطر میلگردها دارد؛ یعنی هرچه میلگردها قطورتر باشند، زمان بیشتری هم برای پلاستیکی شدن نیاز دارند. حداقل زمان لازم برای نازکترین میلگردها، حدود 40 ثانیه است. این زمان میتواند تا سه دقیقه یا کمی بیشتر هم ادامه یابد.
بهطورکلی، در جوش سر به سر میلگرد و بهخصوص در مرحله حرارتدهی، تجربه، دقت و دانش فرد مجری عملیات، بسیار مهم است. او باید شیب بالا رفتن دما را کنترل کند و بتواند بهخوبی زمان لازم برای قطع عملیات حرارتدهی و رفتن به مرحله فشار هیدرولیکی را تشخیص دهد.
در این مرحله، ایمنی کار بسیار اهمیت پیدا میکند. باید همواره از سالم بودن تمامی نازلها و کنترلکنندهها بهخصوص کنترلکنندههای روی مشعل، اطمینان حاصل کرد. در صورت بازگشت گاز از مشعل به کپسول، انفجار رخ خواهد داد که پیامد آن خسارات سنگین جانی و مالی است؛ بنابراین، همواره باید از قرار داشتن این کنترلکنندهها در وضعیت درست و سالم بودن آنها اطمینان حاصل کرد.
- مرحله اعمال فشار هیدرولیکی
دستگاه اعمال فشار از چند پمپ هیدرولیکی و شیرهای اعمال فشار، تشکیل شده است. پس از پایان مرحله حرارتدهی و با خمیری شدن میلگردها، نوبت به استفاده از این دستگاه میرسد. این دستگاه به انتهای دو میلگرد فشار وارد کرده و باعث میشود که دو سر خمیری شده آنها در یکدیگر ادغام شوند و اجرای فورجینگ صورت میگیرد.
در کار کردن با دستگاه اعمال فشار، باید این نکته را در نظر داشت که فشار اعمال شده باید از هر دو طرف یکسان باشد. فشار کمپرسور را میتوان با استفاده شیرهای تعبیهشده روی آن تنظیم کرد. در این مرحله هم تجربه و مهارت فرد مسئول جوش سر به سر میلگرد، بسیار مهم است. طبق برخی استانداردها گفته میشود که به ازای هر سانتیمتر مربع از مقطع میلگرد، به حدود 300 الی 400 بار فشار هیدرولیکی، نیاز است.
- اعداد و ارقام در عملیات فورجینگ
دمای لازم برای نرم شدن میلگردها بین 1200 تا 1300 درجه سانتیگراد است. بنابراین، مشعل باید تا رسیدن میلگردها به این دما کار کند. این زمان به ضخامت میلگردها بستگی دارد. میلگردهای باضخامت کم به حدود 40 ثانیه تا یک دقیقه زمان نیاز دارند. میلگردهای نسبتا ضخیم یا ضخیم هم بین 1 تا 3 دقیقه زمان برای نرم شدن نیاز خواهند داشت. فشار گاز خارجشده از هریک از مخازن اکسیژن و استیلن هم باید به ترتیب بین 5 تا 7 و 0.5 bar باشد. درنهایت فشار دستگاه کمپرسور هم باید به ازای هر یک سانتیمتر میلگرد 300 الی 400 کیلوگرم بر سانتیمتر مربع باشد.
نکاتی مهم در اتصال فورجینگ
حرارت حاصل از سوختن گاز استیلن را نمیتوان به شکل کامل کنترل کرد؛ بنابراین باید فرد مسئول انجام فورجینگ در رعایت فشار گاز و طی شدن زمان لازم برای رسیدن فلز به دمای موردنظر، دقت و تجربه لازم را داشته باشد.
مدتزمانهای ذکرشده تقریبی هستند و به دمای محیط نیز بستگی دارند؛ بنابراین مسئول فورجینگ باید تجربه کافی در تشخیص ظاهری زمان مناسب برای اعمال فشار را داشته باشد.
این روش برای آبوهواهای مناطق سردسیر باید با دقت و حساسیت بیشتری انجام شود چراکه اتصالات فورجینگ مقاومتشان در دمای پایین کاهش مییابد؛ بنابراین لازم است که کنترلهای کیفی بیشتری در این شرایط انجام شود.
باید دقت داشت که شیب بالا رفتن دمای میلگردها چندان بالا نباشد چراکه باعث شکنندگی آن پس از سرد شدن خواهد شد. همچنین، درصورتیکه سرد شدن نیز با سرعت بالا اتفاق بیفتد، سبب ایرادات ساختاری در نقاط جوش خواهد شد. این امر بهخصوص، در سازههای ساختمانی که نیاز به استحکام، امنیت و مقاومت در برابر زلزله دارند، اهمیت بیشتری پیدا میکند.
فشار واردشده توسط دستگاه فشار به سر هر دو میلگرد باید کاملا یکنواخت باشد. در غیر این صورت استحکام نقاط جوش تحت تاثیر قرار خواهد گرفت.
روی مشعل شیرهای یکطرفهای قرار دارند که وظیفهشان جلوگیری از بازگشت گاز به داخل مخازن است. اگر این شیرها بهدرستی عمل نکنند، خسارات جانی و مالی فراوانی به وجود خواهد آمد.
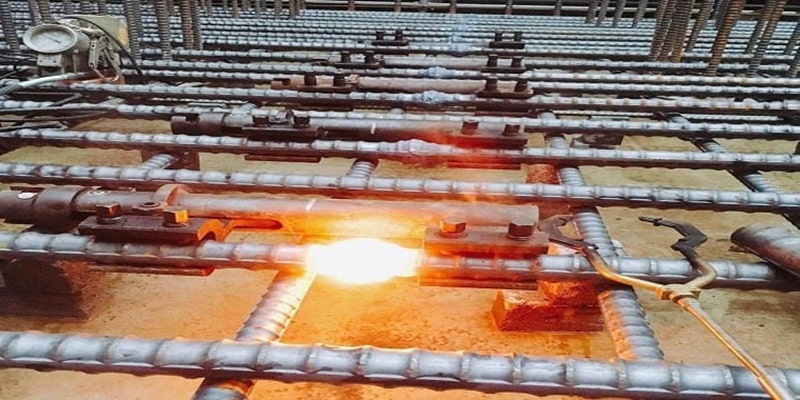
کنترل کیفیت عملیات فورجینگ میلگرد
پس از انجام عملیات فورجینگ و سرد شدن میلگرد بهدستآمده، باید آزمایشهایی روی قطعه انجام داد تا از کیفیت جوش در نقطه اتصال اطمینان حاصل شود. لازمبهذکر است که ازآنجاکه میلگردهای فورجینگ شده عمدتا در عملیات ساختمانی، راهآهن و موارد مشابه بهکاربرده میشوند، باید از استحکام آنها اطمینان حاصل کرد. برخی از کنترلهای کیفی معمول در فورجینگ میلگرد عبارتند از:
- آزمایش کشش
در این ارزیابی قطعه موردنظر توسط دستگاههای کشش از دو سوی آن کشیده میشود. درصورتیکه میلگردها با کیفیت پایینی به هم جوش خورده باشند، در محل اتصال ترک بهوجود خواهد آمد.
- آزمایش اولتراسونیک
مزیت این روش و روش مشابه آن رادیوگرافی این است که در آنها احتمال آسیب رسیدن به میلگردها وجود ندارد، بلکه تنها نقاط ناپیوستگی آنها مشخص میشود. در این روشها از مطالعه رفتارهای پرتوهای نوری تابیده شده به میلگرد روی دستگاههای اندازهگیری مخصوص، نقاط شکننده و ضعیف را شناسایی میکنند. به این دو روش غیرتخریبی یا Non-Destructive میگویند.
- آزمایش خم کردن
در این روش میلگرد بهدست آمده از روش فورجینگ تحت زوایای خم تا 90 درجه قرار میگیرد. در صورت مشاهده هرگونه شکست در محل جوش مشخص میشود که کیفیت انجام فورجینگ پایین بوده و نباید از آن قطعه استفاده کرد. به این روش در کنار آزمایش کشش، روشهای تست تخریبی یا Destructive گفته میشود.
عملیات فورجینگ یکی از عملیات رایج، ارزان و نسبتا مطمئن (در صورت انجام درست و اصولی) اتصال میلگرد است.در اجرای این روش که به اتصال سربهسر نیز معروف است دو سر دو میلگرد توسط گاز تشکیلشده از اکسیژن و استیلن بهقدری گرم شده که پس از رسیدن به دمایی بین 1200 تا 1300 درجه سانتیگراد نرم و خمیری شوند. سپس دو میلگرد توسط دستگاه کمپرسور به یکدیگر فشرده شده و با برقرار شدن پیوند مولکولی اتصال فورجینگ انجام میشود.
فورجینگ میلگرد؛ روشی مطمئن برای اتصال سربهسر
این روش مزایای متعددی دارد اما باید در انجام آن دقت و تجربه کافی داشت. درغیراینصورت ممکن است جوش از استحکام مناسبی برخوردار نباشد که خسارت جانی و مالی، بهخصوص برای کاربرد در سازههای ساختمانی درپی خواهد داشت. میلگردهای فورجشده را میتوان تحت آزمایشهای متعددی ازنظر کیفی قرار داد و از کیفیت جوش بهوجود آمده اطمینان حاصل کرد. شما میتوانید برای مشاهده قیمت میلگرد در سایز و برندهای مختلف به لیست قیمت مرتبط در سایت مراجعه کنید.