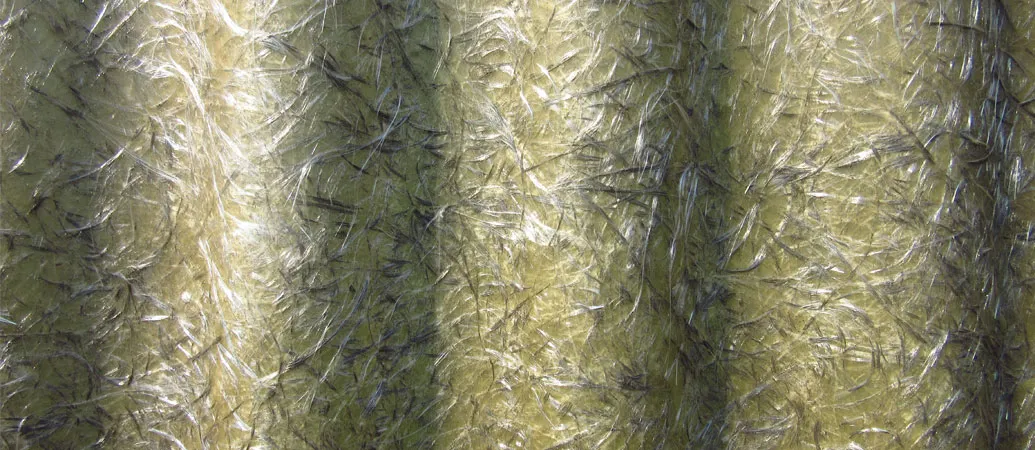
کامپوزیت چیست و انواع آن
مواد کامپوزیتی، از زمان ساخت اولین سازهها گرفته تا کمک به پیشرفت تکنولوژیهای امروزی، نقش مهمی در تاریخ بشر داشتهاند. کامپوزیتها زندگی روزمره ما را تحت تاثیر قرار دادهاند. جالب است بدانید که این مواد دورریز ندارند! مثلا در یک کارخانه خودروسازی، میتوان قطعات کامپوزیتی غیرقابل استفاده را آسیاب کرده و به عنوان پرکننده و تقویتکننده بتن، به کار برد. مصالح ساختمانی، کاربردهای پزشکی، صنایع نفت و گاز، هوافضا، حمل و نقل، ورزش و... در تمام این بخشها، کاربرد محصولات کامپوزیتی غیرقابل چشمپوشی است. کشتیهای فضایی، بدون وجود کامپوزیت (composite)، احتمالا هیچوقت از زمین خارج نمیشدند! اگر میخواهید با این مواد شگفتانگیز بیشتر آشنا شده و به دلایل اهمیت و پراستفاده بودن آنها پی ببرید، مطالعه این مقاله راه مناسبی است.
کامپوزیت متشکل از دو یا چند ماده با خواص فیزیکی و شیمیایی نسبتا متفاوت است که برای دستیابی به هدف مشخصی مانند افزایش استحکام، درخشش یا مقاومت در برابر الکتریسیته، با یکدیگر ترکیب میشوند.
مواد کامپوزیت چیست؟
مواد کامپوزیتی یا مرکب، از ترکیب دو یا چند ماده با خواص فیزیکی و شیمیایی متفاوت ساخته میشوند. این ترکیب از طریق فرآیندهای مکانیکی یا متالورژیکی صورت میگیرد، اما برخلاف مواد آلیاژی، اجزای تشکیلدهنده کامپوزیت، هویت مستقل خود را حفظ میکنند. در واقع، این مواد به شکلی کنار هم قرار میگیرند که مرز میان آنها کاملاً قابل تشخیص است، اما ماده نهایی، ویژگیهایی را ارائه میدهد که هیچیک از اجزای آن بهتنهایی قادر به فراهم کردنشان نیستند.
در آینده، با گسترش تولید کامپوزیت در کشور، قیمت آن کاهش خواهد یافت. نکته جالب اینجاست که در فرآیند تولید این مواد، اجزا در یکدیگر حل نمیشوند، بلکه ترکیب آنها باعث بهبود ویژگیهایی مانند استحکام و دوام میشود. کامپوزیتها از گذشته تاکنون مورد استفاده بشر بودهاند؛ برای مثال، مردم بینالنهرین ۱۵۰۰ سال قبل از میلاد با ترکیب کاه و گل، آجرهایی مقاومتر تولید میکردند. حتی در طبیعت نیز نمونههایی از کامپوزیت وجود دارد، مانند چوب که از فیبرهای سلولزی و لیگنین تشکیل شده است. در صنعت مدرن نیز این مواد به شکلهای متنوعی کاربرد دارند؛ برای نمونه، در تولید چمن مصنوعی، ترکیب پلیاتیلن با وینیل استات باعث بهبود رنگپذیری و انعطافپذیری آن میشود.
تفاوت کامپوزیت و آلیاژ چیست؟
میدانیم که آلیاژ و کامپوزیت هر دو ترکیبی از حداقل دو عنصر هستند. اما تفاوتهایی میان این دو ماده وجود دارد که آنها را برای کاربردهای مختلف مناسب میسازد. بسیاری از تکنولوژیهای نوین، نیازهایی دارند که توسط آلیاژهای موجود قابل پاسخگویی نیست. مانند ویژگیهای مکانیکی بهتر که در کامپوزیتها یافت میشود. تفاوتهای دیگر میان این دو ماده، شامل موارد زیر است:
- تعریف و ویژگیها: یکی از این تفاوتها به تعریف آلیاژ و کامپوزیت بازمیگردد. در ترکیب آلیاژ، یکی از عناصر حتما باید فلز باشد که تعیینکننده خواص فیزیکی آلیاژ است، در حالی که در کامپوزیتها چنین الزامی وجود ندارد و همه مواد میتوانند غیرفلزی باشند. همچنین مواد به کار رفته در یک کامپوزیت را میتوان با روشهای فیزیکی از یکدیگر جدا کرد، در حالی که عناصر سازنده آلیاژ برای بازگشت به حالت اولیه خود، نیازمند واکنش شیمیایی هستند. یک آلیاژ در اصل همان ماده اولیه با خواص بهتر است. آلیاژ کردن به طور دائمی خصوصیات فیزیکی فلزات را تغییر می دهد و مقاومت در برابر خوردگی و اکسیداسیون، خصوصیات الکتریکی، استحکام و... را بهبود میبخشد. در مقابل، کامپوزیت، ترکیبی از عناصر برای تشکیل مادهای کاملا جدید است که ممکن است نسبت به مواد سازنده، مقاومتر، سبکتر یا ارزانتر باشد.
- نوع مخلوط: آلیاژها در دو دسته همگن و ناهمگن یافت میشوند. با توجه به نسبت فلز ترکیب شده با عناصر، آلیاژ میتواند یک یا چند فاز داشته باشد که در صورت تکفاز بودن آن را ماده همگن و در غیر این صورت، ناهمگن مینامند. این در حالی است که تمامی کامپوزیتها مواد ناهمگن هستند.
- هدایت الکتریکی و درخشندگی: آلیاژها به دلیل برخورداری از فلز در ساختار خود، هادیهای خوبی هستند و همچنین درخشندگی زیادی دارند. اما در بین انواع کامپوزیتها که در همین مقاله به آنها خواهیم پرداخت، هیچ یک از آنها درخشان نیستند و فقط پلیمرها هستند که به میزان کمی الکتریسیته را عبور میدهند و بقیه نارسانا هستند.
- آرایش: کامپوزیتها همیشه دارای پیوند هستند، در حالی که آلیاژها میتوانند در آرایش خود پیوند نداشته باشند.
- نقاط ذوب و جوش: کامپوزیتها نقاط جوش و ذوب مشخصی دارند، در حالی که این دماها، در آلیاژهای مختلف متغیر است.
بررسی ساختار کامپوزیتها
نرخ کامپوزیتها به اجزای تشکیلدهنده آنها بستگی دارد. طور کلی، یک ماده کامپوزیت سه جز دارد:
- تقویتکننده: تقویتکننده (reinforcement) به عنوان فاز ناپیوسته یا پراکنده، به شکلهای مختلفی مانند الیاف، پوسته و ذرات وجود داشته و خصوصیات متنوعی دارند. الیاف، متداولترین مواد تقویتکننده هستند که بیشترین تاثیر را در ویژگیهای مکانیکی ماده کامپوزیتی دارند. علت این تاثیرگذاری را باید در نسبت بالای طول به قطر الیاف جستجو کرد که باعث ایجاد تنش برشی موثری بین این ماده و ماتریس شده و قابلیت پردازش و تولید قطعات کامپوزیت به شکلهای مختلف را افزایش میدهد. از مهمترین الیاف کامپوزیتی میتوان به شیشه، کربن و آرامید اشاره کرد.
- ماتریس (زمینه): ماتریس (matrix) به عنوان فاز پیوسته، متصلکننده تقویتکنندهها به یکدیگر بوده و آنها را کنار یکدیگر، در موقعیت ثابت نگه داشته و مانع از حرکت و اعوجاج بین الیاف میشود. در نتیجه تقویتکنندهها در برابر آسیبهای فیزیکی و محیطی مقاوم میشوند. با توجه به نوع سازه، الیاف یا سایر تقویتکنندهها در یک موقعیت خاص قرار گرفته و سپس به وسیله ماتریس، در جایگاه خود تثبیت میشوند. مواد مختلفی مانند پلی استر، اپوکسی و فنول را میتوان به عنوان ماتریس، در ساختمان یک کامپوزیت به کار برد. اما لازم است در انتخاب آن دقت کافی به خرج داده شده و به خصوصیات ماده کامپوزیتی مورد نظر توجه شود. به این دلیل که ویژگیهایی مانند مقاومت در برابر خوردگی، مقاومت الکتریکی و حرارتی و اشتعالپذیری، به طور مستقیم به نوع ماده زمینه بستگی دارند.
- فاز میانی: لایهای فشرده شده از ماتریس که در سطح تقویتکننده تشکیل میشود را فاز میانی مینامند که در حقیقت فصل مشترک میان این دو ماده است. برای ذرات پراکنده که ابعاد آنها در حد میکرون بوده، تاثیر این لایه قابل چشمپوشی است. اما نانوذراتها سطح وسیعتری داشته و میتوانند درصد قابل توجهی از حجم کامپوزیت را اشغال کنند. بنابرین در تقویتکنندههایی با جنس نانوذراتهای پراکنده، فاز میانی بر خواص کامپوزیت تاثیرگذار است. در حقیقت، بسیاری از ویژگیهای برجسته نانوکامپوزیتها از جمله مقاومت تسلیم، ناشی از فاز میانی است.
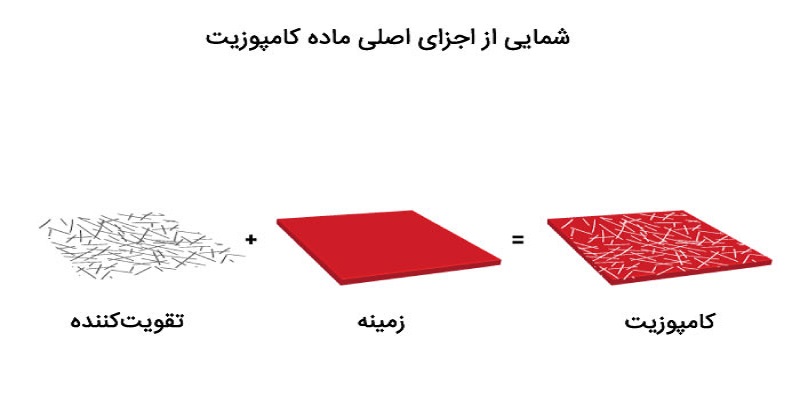
انواع کامپوزیتها
کامپوزیتها را میتوان به صورت زیر دستهبندی کرد:
- بر اساس نوع مادهی زمینه
- بر اساس نوع و شکل ماده تقویتکننده
با توجه به نوع ماتریس، کامپوزیتها عمدتا در چهار گروه جای میگیرند:
- کامپوزیتهای با زمینه فلزی (MMC): کاربرد این نوع کامپوزیت، در صنعت هوافضا بسیار بالاست. استفاده از فلز آلومینیوم به عنوان زمینه، که چگالی کمتری نسبت به آهن دارد، برای افزایش مقاومت آن، صورت میگیرد. درکامپوزیتهای زمینه فلزی، از الیاف پیوسته کربن، کاربید، سیلیکون یا الیاف سرامیکی به عنوان تقویتکننده استفاده میشود.
- کامپوزیتهای زمینه سرامیکی (CMC): در ساختمان این محصول، الیاف سرامیکی یا کربنی، به وسیله ماتریس سرامیکی مانند کاربید سیلیکون، احاطه شدهاند.
- کامپوزیتهای با زمینه مواد آلی، پلیمری یا پلاستیکی تقویتشده (PMC): این کامپوزیت از الیاف کوتاه یا بلندی ساخته شده که توسط یک زمینهی پلیمری آلی، به یکدیگر متصل شدهاند. ویژگی اصلی این نوع کامپوزیت، پخش کردن بار میان الیاف، به وسیله ماتریس است.
یکی از پرکاربردترین کامپوزیتها با زمینهی پلیمری، فایبرگلاس نام دارد که مادهی تقویتکننده در آن، شیشه است. درباره این کامپوزیت که با نام FRP (پلاستیک تقویتشده با الیاف) نیز شناخته میشوند.
- کامپوزیتهای کربن/کربن (CC): زمینهی این کامپوزیتها شامل کربن بوده و تقویتکنندهها، فیبرهای کربن سه بعدی، درشکل های تابیده و بافته شده هستند.
بر اساس نوع ماده تقویتکننده، کامپوزیتها عبارتند از: - کامپوزیتهای تقویتشده به وسیله الیاف (FRC): کامپوزیتهایی که در آنها فاز پراکنده به شکل رشته است، اهمیت بیشتری در صنعت و تکنولوژی دارند. موادی که به عنوان الیاف تقویتکننده به کار میروند، با توجه به قطر و مشخصه مربوطه به سه دسته ویسکرها، رشتهها و سیمها تقسیم میشوند. خواص مکانیکی این کامپوزیتها به خواص رشته، مقدار نیروی منتقل شده از فاز ماتریس و درصد حجمی آن بستگی دارد. در این کامپوزیتها هر چه رشته نازکتر باشد، استحکام آن بیشتر خواهد بود.
- کامپوزیتهای تقویت شده به وسیله ذرات (PRC): این مواد کامپوزیتی، با توجه به مکانیزم مستحکم شدن یا تقویت شدن، به دو گروه درشتذره و مستحکم شده با ذرات پراکنده، تقسیم میشوند.
- کامپوزیتهای درشتذره: در کامپوزیتهای درشتذره، فعل و انفعالات بین ذره و ماتریس، نمیتواند در مقیاس مولکولی یا اتمی رخ دهد و فاز تقویتکننده سفتتر از زمینه است. به نحوی که این ذرات، باعث توقف حرکت فاز زمینه در مجاورت خود میشوند.
کامپوزیتهای مستحکم شده با ذرات پراکنده: در این کامپوزیتها، اندازه ذرات بین ۱۰ تا ۱۰۰ نانومتر بوده و فعل و انفعلات بین آنها، در مقیاس اتمی و مولکولی اتفاق میافتد. این عمل باعث افزایش استحکام، در این نوع کامپوزیت میشود. - کامپوزیتهای سبز: ماتریس و تقویتکننده این کامپوزیتها از موادی ساخته میشوند که از نظر زیستی تجزیهپذیر بوده و در محیط زیست باقی نمیمانند. موادی مانند پلیمرهای سنتزی قابل جذب بیولوژیکی، به عنوان فاز زمینه و الیاف گیاهی به عنوان تقویتکننده به کار میروند. برای کسب اطلاعات بیشتر درباره ورق کامپوزیت و انواع آن به مقاله مربوطه مراجعه کنید.
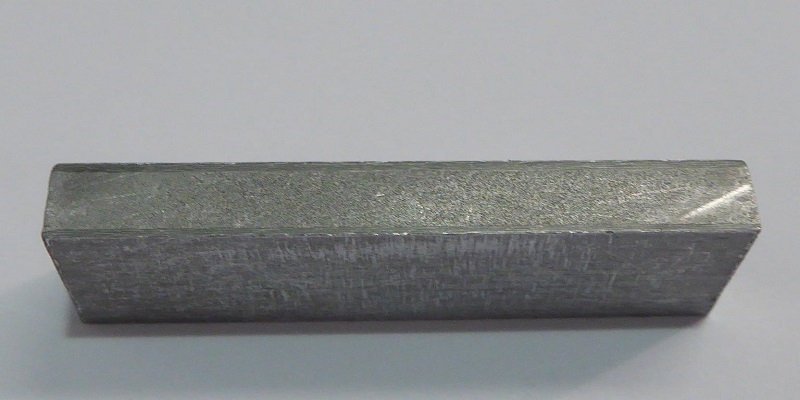
خواص مکانیکی، شیمیایی و الکتریکی کامپوزیت ها
استفاده از مواد مختلف برای ساخت کامپوزیت، میتواند ضعف هر یک از آنها را پوشش داده، نقاط قوت آنها را تقویت کرده و ویژگیهای تازهای به وجود بیاورد. خصوصیات حاصل شده، به عواملی مانند مقدار، اندازه و شکل تقویتکننده، توزیع فاز تقویتکننده، خواص مکانیکی ماتریس و طبیعت فصل مشترک بین ماتریس و تقویتکننده، بستگی دارد. برخی از مهمترین این ویژگیها، موارد زیر هستند:
- مقاومت در برابر خوردگی: کامپوزیتها مقاومت بالایی در برابر موارد خورنده و شیمیایی دارند و در برابر آب، رطوبت و تابش مستقیم نور نیز از خود استحکام نشان میدهند.
- مقاومت مکانیکی: بر خلاف فلزات که در تمام جهتها و شرایط به یک میزان مستحکم هستند، کامپوزیتها را میتوان به گونهای مهندسی و طراحی کرد که در یک جهت خاص، استحکام بیشتری داشته باشند.
- مقاومت الکتریکی: مقدار این مقاومت به نوع مواد به کار رفته در تولید کامپوزیت بستگی دارد. مثلا کامپوزیت ساخته شده با الیاف شیشه عایق، و کامپوزیت دارای الیاف کربن، هادی است.
- هدایت حرارتی بسیار کم: این خصوصیت، کامپوزیتها را برای استفاده به عنوان عایق حرارتی، مناسب میسازد
- مقاومت ویژه بالا و مدول ویژه بالا: این دو ویژگی، از برجستهترین خصوصیات کامپوزیتها هستند. برای مثال، در کامپوزیت رزین تقویتشده با الیاف کربن، مقدار مدول ویژه، ۵ برابر بیشتر از فولاد و آلیاژ آلومینیوم، و مقدار مقاومت ویژه، ۳ برابر بیشتر از این دو ماده است.
- مقاومت در برابر خستگی بالا: کامپوزیت الیاف، به ویژه کامپوزیت زمینه رزین، حساسیت کمتری نسبت به بریدگی و تنش دارد. علاوه بر این، فاز فصل مشترک بین ماتریس و الیاف، میتواند انتشار ترک را کند کرده و یا جهت آن را تغییر دهد و از گسترش ترک جلوگیری کند. بنابراین، مقاومت در برابر خستگی در کامپوزیتها بالاست.
- مقاومت زیاد در برابر شکستگی: در کامپوزیتهای الیاف، تعداد بسیار زیادی رشته مستقل از الیاف وجود دارد. این مقدار به طور کلی به هزار تا ده هزار، در هر سانتیمتر مربع میرسد. همانطور که گفته شد این الیاف به وسیله ماده زمینه به هم متصل میشوند. اگر در اثر اضافه بار یا عوامل دیگر، تعدادی از این الیاف شکسته شوند، بار بین الیاف سالم باقی مانده توزیع شده و در نتیجه از بروز آسیب ناگهانی جلوگیری میشود.
- میرایی خوب: فرکانس طبیعی یک سازه، به جرم و شکل آن مربوط بوده و با توان دوم ریشه مدول ویژه، متناسب است. اگر فرکانس طبیعی ماده زیاد باشد، احتمال بروز تشدید و آسیب رسیدن به سازه کمتر است.
- چگالی پایین: به همین دلیل، حمل و نصب و بارگیری کامپوزیتها بهصرفهتر است.
- سهولت در تولید و ساخت شکلهای پیچیده، با روشهای ساده، کارآمد و مقرون به صرفه
- آسان بودن مونتاژ قطعات و عملیات تعمیر و عیبیابی
- ضریب انبساط حرارتی پایین
- بهبود اتصالات و تولید یکپارچه
- جذب انرژی مناسب
آینده کامپوزیت در ایران؛ فرصتها و چالشها
در این مقاله با ساختار کامپوزیتها، خصوصیات و انواع مختلف آنها آشنا شدیم. توسعه فناوری ساخت کامپوزیتهای دارای زمینهی پلیمر، باعث شده تا طیف گستردهای از صنایع، از ویژگیهای این محصول ارزشمند بهره بگیرند. صنایعی که عموما به تلفیقی از خواص مختلف نیاز دارند که با به کار بردن تنها یک ماده، قابل دستیابی نیست. مطابق با استاندارد بینالمللی، شاخص توسعهیافتگی از نظر مصرف کامپوزیت، مقدار سالیانه 3 کیلوگرم به ازای هر شهروند است. بیش از ۹۵ درصد از کامپوزیت مصرف شده در ایران، از نوع زمینه پلیمری است که در داخل کشور نیز با روشهایی مانند پیچش الیاف، SMC و قالب بسته تولید میشوند. به نظر شما این صنعت در سالهای آتی، در ایران رشد بیشتری خواهد داشت؟ چه چالشهایی را پیش روی آن میبینید؟ به طور کلی برای اطلاع از نرخ محصولات فولادی مانند: قیمت میلگرد، تیرآهن و … به لیست صفحات قیمت در آهن آنلاین مراجعه نمایید.