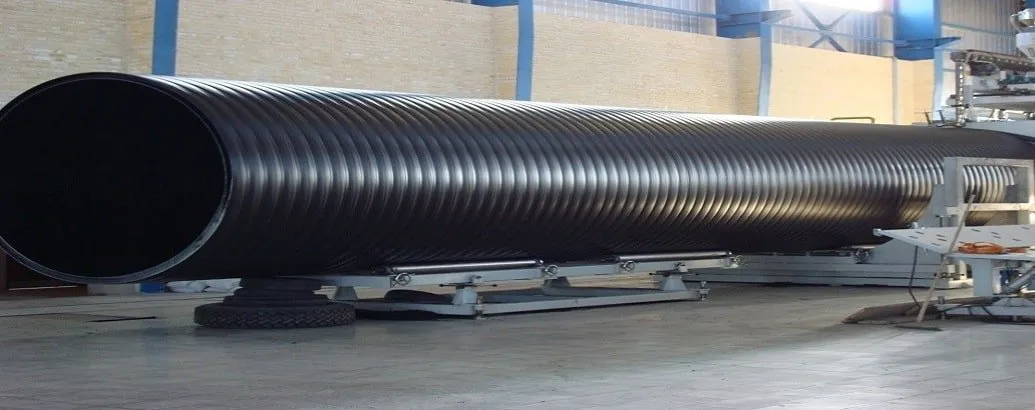
شیوه های فرم دهی و فرآیند تولید لوله اسپیرال
در مطالب قبلی به بررسی لوله مانیسمان و لوله سیاه پرداختیم. در این مطلب به بررسی لولههای اسپیرال میپردازیم. در این شیوهی تولیدی لولهی مد نظر به صورت مارپیچ از ورق تولید میگردد. ورق مورد استفاده ضخامتهای مختلفی دارد. به این روش تولیدی در زبان انگلیسی SPIRAL WELD میگویند. جوش لوله اسپیرال از مهمترین ساختار این محصول فولادی به شمار میآید. اینکه جوش لوله به چه صورتی زده میشود حائز اهمیت است، زیرا استحکام لوله به مقاومت لوله در برابر جریان ورودی لوله و فشاری که بر دیوارههای آن وارد میشود وابسته است. بیشترین کاربرد این لولهها در صنعت گاز و نفت میباشد. در این مطلب ابتدا تعریفی از لوله اسپیرال را مطرح میکنیم و در ادامه به بررسی شیوههای فرمدهی لولههای اسپیرال، تولید لوله اسپیرال به روش یک مرحلهای، تولید لوله اسپیرال به روش دو مرحلهای و فرآیند تولید لولهی اسپیرال میپردازیم.
لوله اسپیرال چیست؟
لوله اسپیرال (SSAW) که با نام لوله جوش مارپیچی نیز شناخته میشود، از نورد فولاد کمکربن یا کمآلیاژ در زاویهای مشخص ساخته شده و سپس جوش داده میشود. این لولهها عمدتاً برای انتقال نفت، گاز طبیعی و سایر مایعات استفاده میشوند. برخی مدلهای آن از پلیاتیلن یا الیاف کربن تولید میشوند که در صنایع مختلف کاربرد دارند. سطح داخلی صاف این لوله اصطکاک جریان را کاهش داده و به بهبود انتقال مایعات کمک میکند، درحالیکه ساختار مارپیچی بیرونی آن استحکام بالایی در برابر فشارهای محیطی ایجاد میکند. انعطافپذیری بالای لوله اسپیرال، آن را برای پروژههایی که به خمکاری نیاز دارند، ایدهآل کرده است. همچنین، برای کسب اطلاعات بیشتر درباره لوله اسپیرال میتوانید به مقاله لوله اسپیرال چیست، مراجعه کنید.
شیوههای فرمدهی لولههای اسپیرال
از استاندارد لولههای تولیدی در جهان میتوان به تولید لولههای اسپیرال اشاره کرد. در این شیوه ورق از تعدادی غلتک عبور میکند تا اینکه به شکل لوله در میآید. یا تغییر زاویهی تغذیهی اولیه ورق شاهد تغییر قطر لوله خواهیم بود. به عبارتی لولههای اسپیرال در قطرهای مختلف را میتوان تنها با تغییر زاویهی تغذیه اولیهی ورق تولید نمود. از مزیتهای این روش نسبت به لولههای درز مستقیم این است که برای تولید ورق با قطرهای مختلف تنها باید زاویهی تغذیه ی اولیهی ورق تغییر نماید و مانند تولید لوله درز مستقیم نیازی به تغییر کل قالبهای خط تولید نمیباشد. همین امر سبب میشود تا هزینهی تولید لوله تا حد زیادی کاهش پیدا کند. تولید لولههای اسپیرال به دو شیوه ی یک مرحلهای و دو مرحلهای صورت میپذیرد.
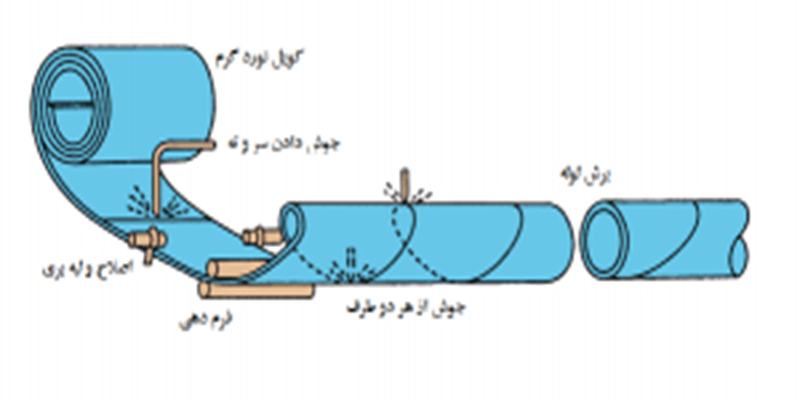
تولید لوله اسپیرال به روش یک مرحلهای
اولین روش تولید اسپیرال به شیوهی یک مرحلهای بوده است. این شیوه خود شامل سه گام برای تولید لوله است.
- آمادهسازی: در این مرحله سر ورقها را به یکدیگر جوش میزنند، لبهی ورقها پخ زده میشوند و در نهایت صاف میگردند.
- شکلدهی: با انجام عملیات شکلدهی به صورت کامل لبهی ورق باید به حالت پیش خم درآید تا مانع از ایجاد برآمدگیهای غیرقابل پرس شود.
- جوشکاری زیرپودری: توجه داشته باشید که در عملیات جوشکاری تنظیم مشعل به صورت کاملا اتوماتیک انجام میشود.
به منظور جوشکاری درز این نوع از لولهها دو مرحله صورت میگیرد. مرحلهی اولیه، درز داخلی را به وسیلهی دستگاه جوش زیرپودری در موقعیت ساعت ۶ جوش میدهند. مرحلهی ثانویه، در موقعیت ساعت ۱۲ پاس خارجی جوش خورده میشود. بعد از جوشکاری لوله را برش میدهند.
سرعت تولید لوله اسپیرال به روش یک مرحلهای وابسته به سرعت جوشکاری زیرپودری میباشد( سرعت این نوع از جوشکاری معمولا بین ۱ تا ۲٫۵ متر بر دقیقه است. به طور استثنا ممکن است به ۳ متر بر دقیقه نیز برسد). سرعت تولید لوله در این روش به دلیل محدودیت در سرعت جوشکاری معمولا کند میباشد.
تولید لوله ی اسپیرال به روش دو مرحلهای
مراحل تولید این نوع لوله تقریبا مانند روش تولید یک مرحلهای میباشد و تفاوت آن با روش بالا، تنها در نوع جوشکاری است. در این روش برای جوشکاری درز از روش GMAW استفاده میشود. که به منظور جوش پاس ریشه به کار میرود، سایر مراحل درز از داخل و خارج به وسیلهی جوشهای زیرپودری پر میشوند. جوشکاری GMAW همان جوشکاری قوسی فلزی با گاز است که به طور معمول به صورت نیمه اتوماتیک انجام میگیرد اما از آن به صورت تمام اتوماتیک نیز استفاده مینمایند. از طریق شکلگیری قوس الکتریکی ایجاد شده بین الکترود کلافی و قطعه کار، حرارت مورد نیاز به منظور ذوب تولید میشود.
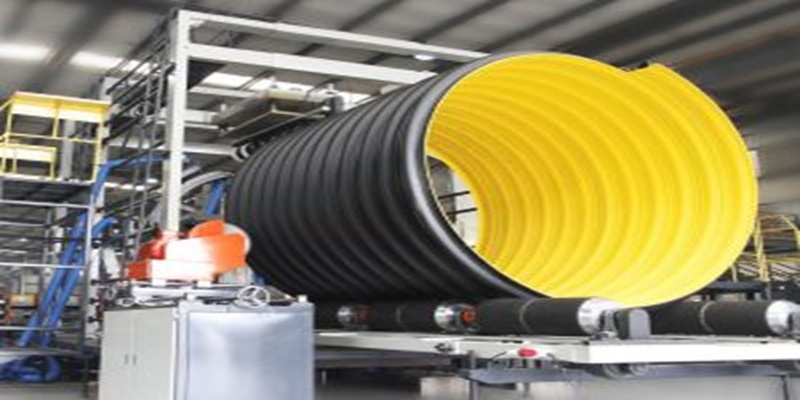
فرآیند تولید لوله اسپیرال
در این بخش از این مطلب به طور مختصر فرآیند تولید این نوع از لولهها را در چندین مرحله به تفکیک مورد بررسی قرار میدهیم.
- مواد اولیه: مواد اولیه وارد کارخانه میشوند. سپس واحد کنترل کیفیت، مواد را مورد بازرسی قرار میدهد.
- آمادهسازی کلاف: سر کلافها به وسیلهی دستگاه CCP برش داده میشود (قبل از انتقال کلافها به سمت ماشینهای مخصوص لولهسازی).
- باز کردن کلافها: کلافها به سمت دستگاههای کلاف باز کن منتقل میشوند این دستگاهها کلافها را باز میکنند.
- صاف کردن ورقها: بعد از اینکه کلافها در مرحلهی بالا توسط دستگاههای کلاف باز کن باز میشوند، انواع ورق به سمت غلطکهای صاف کن جابهجا میشوند تا فرآیند صاف کردن ورقها صورت گیرد.
- انتهای هر کلاف را به ابتدای کلاف بعدی جوش میدهند: به این نوع جوش، جوش عرضی میگویند که به منظور عملیات جوش، دو انتهای کلاف مورد استفاده قرار میگیرد. عملیات جوشکاری در این مرحله، جوشکاری زیر پودری است.
- پخزدن ورقها: به منظور جوشکاری صحیح، عملیات پخ زدن لبههای ورق با استفاده از تیغههای لبهبرداری یا دستگاه پخزن صورت میگیرد.
- انجام تست امواج مافوق: به منظور اطمینان صددرصدی از عملیات جوشکاری درز، از امواج مافوق به منظور تست جوشکاری درز به صورت مداوم در طی فرآیند تولید استفاده میکنند. تست به وسیلهی دستگاه آلتراسونیک اتوماتیک انجام میشود و در نظر داشته باشید که عملیات تست مخرب بعد از شکلدهی لوله صورت میگیرد.
- برش لوله: برای اینکه لوله در استانداردهای مد نظر برش داده شوند از دستگاه برش پلاسما استفاده میکنند. حرارت لازم برای عملیات برشکاری از طریق یونیزه شدن گاز نیتروژن حاصل میشود.
- تمیز کردن داخل لوله: پودرهای جوشکاری به هنگام انجام جوشکاری پودری در داخل لولهها میمانند. بعد از مرحلهی برش دادن لولهها، به منظور تمیز کردن این پودرها که در لولهها باقی مانده در صورتی که لوله جوش عرضی داده شده باشد بعد از عملیات جوشکاری عرضی به دستگاه تمیزکنندهی داخلی انتقال مییابد و در غیر اینصورت ( یعنی لولهها به طور عرضی جوش داده نشوند) مستقیم به دستگاههای تمیزکننده منتقل میشوند.
- بازرسی چشمی لوله: بعد از تمیزکاری، لولهها به بازرسی چشمی انتقال مییابند که عملیات بازرسی بر روی بدنهی لوله و درز جوش صورت میگیرد.
- تعیمر لولههای مخرب: اگر در مرحلهی بالا تشخصی داده شود که لوله معیوب است لوله به سمت ایستگاه تعمیرات جوش انتقال مییابد و اقدام به تعمیر موارد معیوب مینمایند.
- تست هیدرواستاتیک لولهها: بعد از مراحل بازرسی و تعمیرات صورت گرفته لولهها به منظور انجام تست هیدرواستاتیک به مرحلهی هیدروتست به وسیلهی خطوط انتقال به طور اتوماتیک جابهجا میشوند.
- پخ کردن: بعد از مرحلهی هیدروتست با توجه به نیاز خریدار اگر نیازی به پخ زدن احساس شود لولهها را به قسمت Beveling Machine منتقل میکنند تا عملیات پخ زنی دو سر لولهها انجام شود.
- بازرسی نهایی: بعد از انجام مراحل بالا، بر روی تمامی جوشها و بدنهی لوله، کنترل کیفی نهایی صورت میگیرد. بدین منظور از روش تست آلتراسونیک دستی برای تمامی موارد استفاده مینمایند.
- حمل و نقل لولهها: بعد از اتمام مراحل تولید برچسبی که حاوی اطلاعات لوله میباشد در داخل لوله چسبانده میشود. این اطلاعات شامل مواردی از قبیل، وزن لوله، سایز لوله، شماره لوله است.
کاربردهایی از لولههای اسپیرال
لولههای اسپیرال کاربردهای زیادی دارند در این قسمت تعدادی از کاربردهای مهم لولهی اسپیرال را مطرح مینماییم. لولههای انتقال مواد نفتی، سیستمهای آبرسانی و زهکشی آبیاری تحت فشار.
موارد فوق در زمینهی تولید لولهی اسپیرال و کاربردهای آن میباشد. اگر در این زمینه اطلاعاتی دارید، میتوانید آن را از طریق کامنت با ما و دیگر دوستان به اشتراک بگذارید. در مطالب آینده، به بررسی سایر روشهای تولید لولههای فولادی خواهیم پرداخت.