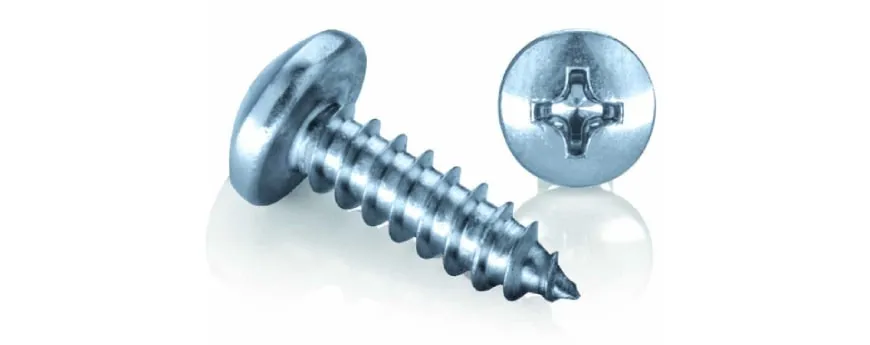
پیچ چیست؟ انواع و کاربرد آن
پیچ (screw)، در واقع استوانهای است که شیارهای مارپیچ آن را احاطه کرده است. طراحی شیار پیچها برای بریدن مواد نرمتر و سختتر متفاوت است، شیارها اغلب بهصورت مثلث، مربع، ذوزنقه و نیم دایره روی سطح جانبی بدنه ایجاد میشود. شایعترین کاربرد پیچ برای نگه داری اشیا و قطعات به یکدیگر است. در انتهای اغلب پیچ ها یک بخش خاص و نوک تیز وجود دارد تا ورود به قطعه آسان شود. ابزار های رایج برای استفاده از پیچ ها آچار و پیچ گوشتی است، سر این ابزار معمولا بزرگتر از بدنه پیچ است تا بتواند نیروی بیشتری به پیچ وارد کرده و آن را در طول قطعه براند.
بخش استوانهای از قسمت انتها تا نوک پیچ را پای پیچ گویند که ممکن است کل یا بخشی از آن رزوه شده باشد. به فاصله میان هر شیار با شیار دیگر گام پیچ گفته می شود. بیشتر جهت صعود مارپیچ ها به فرم ساعت گرد است که اصطلاحا به آنها پیچ راستگرد گویند که برای باز کردن آن باید آچار را به سمت چپ بگردانیم. پیچ های چپ گرد در موارد خاص مورد استفاده قرار میگیرند.
پیچ چیست؟
پیچ، نوعی سطح شیبدار است که به دور یک محور یا استوانه پیچیده شده و برای ایجاد اتصال مکانیکی استفاده میشود. یکی از متداولترین روشهای اتصال قطعات، مخصوصاً در سازههای مکانیکی، بهکارگیری پیچ و مهره است. پیچها اغلب در مواردی استفاده میشوند که نیاز به جداسازی و تنظیم مجدد دارند، برخلاف چسب یا جوش که اتصالات دائمی ایجاد میکنند.
اصطلاح "Bolt" بهطور کلی برای انواع اتصالات رزوهدار بهکار میرود، از جمله پیچهای دو سر رزوه (Stud Bolt) و پیچهای خودکار (Machine Screws). موضوعات متعددی در مورد پیچ و مهره وجود دارد، از جمله جنس و آلیاژهای مصرفی، ابعاد، آنالیز شیمیایی، خواص مکانیکی، طراحی، روش تولید، استانداردهای مرتبط، بازرسی کیفی، پوششدهی، خوردگی، شکستهای احتمالی و نحوه اعمال گشتاور. استاندارد ISO 1891 نیز تعاریف و اصطلاحات مرتبط با پیچ و مهره را مشخص میکند.
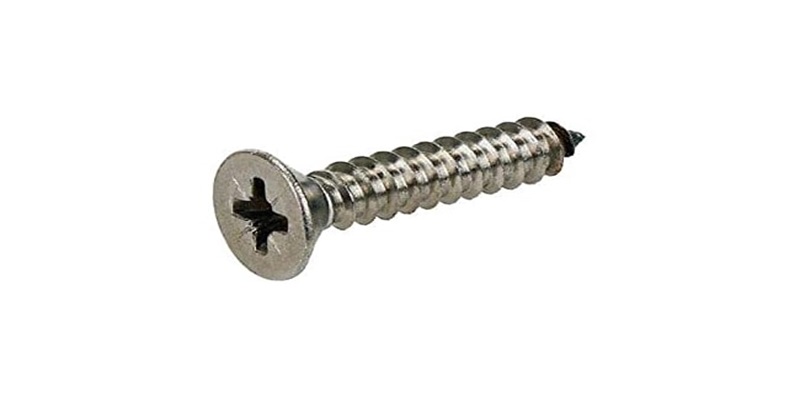
متریال: در پیچهای فلزی از فولاد کربن پایین , کربن متوسط و کربن بالا استفاده میکنند. یکی از مهمترین نکاتی که در تولید پیچ و مهره باید به آن توجه داشت نوع جنس و مواد اولیه است که در کیفیت محصول و قیمت تمام شده آن تاثیر زیادی دارد .نوع مفتول فولادی که در تولید پیچ و مهره ها استفاده می شود باید قابلیت فرم پذیری سرد (ColdHeadingQuality (CHQ باشند.
این نوع فولاد معمولا از فولاد های ساختمان و معمولی گرانتر است. در این نوع فولاد سعی می شود حبابهای ریز هوا به حداقل برسد و سطح و مقطع مفتول به صورت یکنواخت و همگن تر باشد تا در هنگام تولید ایجاد ترک نشود.
نکته: این نوع از پیچها بعد از تولید مورد عملیات حرارتی قرار گرفته تا میزان مقاومتشان تقویت گردد. فولاد های کربن پایین: پیچ های تولید شده از این فولاد معمولا در صنایعی استفاده می شود که فشار بالایی چه از لحاظ دما، کشش و نیرو بر روی آن نباشد، مانند صنایع برق و مخابرات و صنایع پایین دستی به این پیچها، پیچ آهنی میگویند.
- فولاد های کربن متوسط: پیچهای تولیدشده از این فولاد بهعلت استحکام بالا دزر صنایع پل سازی، استراکچر سازی، نفت و صنایع حساس استفاده میشوند. این نوع از پیچها، پیچ فولادی یا خشکه خطاب میشوند.
- فولاد های کربن بالا (زنگ نزن): پیچ های تولید شده از این فولاد به علت مقاومت بسیار بالا در زمینه های مختلف در صنایع دریایی، صنایع غذایی ومکانهای بسیار مرطوب استفاده میشوند.
نکته: بهعلت هزینه بسیار بالای این محصولات از مشابه فولادی با پوشش های مختلف در صورت امکان استفاده میشود. استفاده از فلزهای آلمینیوم، مس و برنج نیز معمول است.
- فورج: فورج پیچ و مهره به دو روش سرد و گرم انجام میگیرد. در روش فورج گــرم بعــد از حــرارت دهــی سـر قطـعه در دمـای بــالا (۸۵۰-۱۲۰۰) توسط دستگاه پرس شکل سر پیچ ایجاد می شود. در روش فورج سرد یا اکستروژن بدون استفاده از حرارت و توسط دستگاه قالب زنی ، پیچ در طی چند مرحله ولی بسیار سریع تغییر مقطع داده و بصورت آماده استفاده (رزوه شده) از دستگاه خارج میشود.
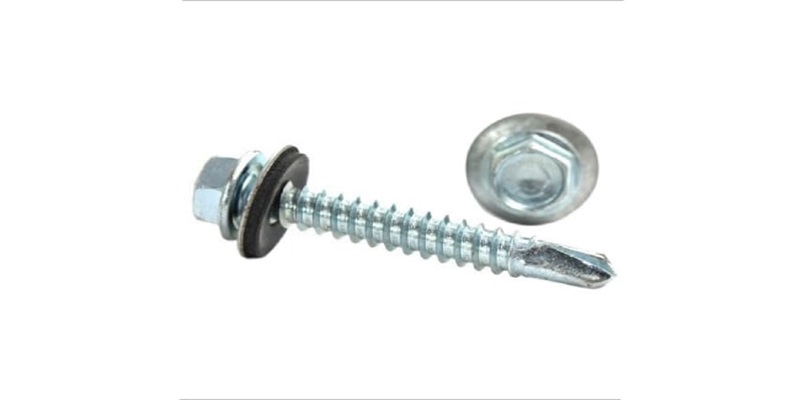
انواع پیچ براساس ظاهر
- پیچ های خودکار: پیچ های خودکار نوعی از پیچ هستند که برای ثایت شدن در قطعه مورد اتصال نیازی به مهره ندارد و درون کار فرو می رود و نوک آن معمولا مانند میخ تیز است، در مواردی می تواند قطعه را سوراخ کند. مانند پیچ سر مته ای و پیچ چوب.
- پیچ های غیر خودکار: این نوع پیچها برای ثابت شدن نیاز به مهره دارند یا قطعه ای که مانند مهره باشد و بتواند کار مهره را انجام دهد, معروفترین آن را می توان پیچ شش گوش را ذکر کرد همچنین پیچ اتاقی، پیچ جوشی، پیچ استوانه، پیچ آلن و استاد بولت و
پوشش های مختلف پیج
- پوشش: همانگونه که در گذشته توضیح دادیم برای استفاده از پیچ و مهره های آهنی و فولادی در محیط های مرطوب و صنایع دریایی از پوشش های مختلف استفاده می شود که به اختصار هر کدام را توضیح میدهیم.
- فسفات و کرومات: این پوششها که پوششهای تبدیلی نامیده میشوند، پوششهایی هستند که از خود فلز ایجاد میشوند. فسفاتها و کروماتها نامحلولاند.
با استفاده از محلولهای معینی مثل اسید سولفوریک با مقدار معینی از نمکهای فسفات ، قسمت سطحی قطعات فلزی را تبدیل به فسفات یا کرومات آن فلز میکنند. در نتیجه، به سطح قطعه فلز چسبیده و بعنوان پوششهای محافظ در محیطهای خنثی میتوانند کارایی داشته باشند. این پوششها بیشتر به این دلیل فراهم میشوند که از روی آنها بتوان پوششهای رنگ را بر روی قطعات فلزی بکار برد. پس پوششهای فسفاتی ، کروماتی ، بعنوان آستر نیز در قطعات صنعتی میتوانند عمل کنند؛ چرا که وجود این پوشش ، ارتباط رنگ با قطعه را محکمتر میسازد. رنگ کم و بیش دارای تخلخل است و اگر خوب فراهم نشود، نمیتواند از خوردگی جلوگیری کند.
- اکسید فلزات: اکسید برخی فلزات بر روی خود فلزات ، از خوردگی جلوگیری میکند. بهعنوان مثال، میتوان تحت عوامل کنترل شده، لایهای از اکسید آلومینیوم بر روی آلومینیوم نشاند. اکسید آلومینیوم رنگ خوبی دارد و اکسید آن به سطح فلز میچسبد و باعث میشود که اتمسفر به آن اثر نکرده و مقاومت خوبی در مقابل خوردگی داشته باشد. همچنین اکسید آلومینیوم رنگپذیر است و میتوان با الکترولیز و غوطهوری، آن را رنگ کرد. اکسید آلومینیوم دارای تخلخل و حفرههای شش وجهی است که با الکترولیز، رنگ در این حفرهها قرار میگیرد.
- گالوانیزه گرم مذابی (HotDipGalvanaized): روی فلزی است به رنگ سفید متمایل به آبی٬ بالاتراز ۱۰۰ درجه سانتیگراد شکننده٬ مابین۱۰۰ الی ۲۰۰ درجه سانتیگراد نرم٬ قابل انحنا و انبساط است و میتوان به صورت ورق نازک درآورد، بالای ۲۰۰ درجه سانتیگراد دوباره شکننده میشود. خاصیت تکنیکی خیلی مهم روی حفاظت خیلی خوب پوششهای آن در مقابل خوردگی است.
این خاصیت ترجیحا بواسطه تشکیل لایه یکنواخت و چسبنده اتمسفر ایجاد میشود و عموما شامل اکسید و هیدروکسید کربنات روی و گاهی نیز سولفات و کلرید روی میباشد. این روش گالوانیزه کردن بوسیله غوطهور نمودن فلز در حمام روی مذاب در دمای ۴۲۰-۴۵۰ C انجام میشود و پس از خارج نمودن نمونه از حمام، روی نخست با اکسیژن و سپس با کربن واکنش داده و لایه مقاوم بهخوردگی (ZnCo3) را ایجاد میکند.
این روش برای جلوگیری از زنگ زدگی استفاده میشود. این نوع گالوانیزه باعث پیوند روی و آهن میشود و این پوشش قابلیت پذیرش جوش دارد و برای کار در دمای بالا (تا ۲۰۰C ) مناسب است. گاهی به حمام روی سرب افزوده میشود که هدف از این کار افزایش سیالیت روی است. این امر باعث کاهش مصرف روی و قابل بازیافت بودن سرباره میشود.
- گالوانیزه الکتریکی (سفید،زرد، هفت رنگ و سبز) (zinc plated): در این روش ترسیب گالوانیک یک فلز بر پایه واکنشهای الکتروشیمیایی صورت میگیرد. هنگام الکترولیز در سطح محدود الکترود/الکترولیت در نتیجه واکنشهای الکتروشیمیایی الکترونها یا دریافت میشوند (احیا) و یا واگذار میشوند (اکسیداسیون). برای اینکه واکنشها در جهت واحد مورد نظر ادمه یابند لازم است.
بهطور مداوم از منبع جریان خارجی استفاده شود. واکنشهای مشخص در آند و کاتد همچنین در الکترولیت همیشه به صورت همزمان صورت میگیرند. محلول الکترولیت باید شامل یونهای فلز رسوبکننده باشد و چون یونهای فلزها دارای بار مثبت است به علت جذب بارهای مخالف تمایل به حرکت در جهت الکترود یا قطبی که دارای الکترون اضافی میباشد (قطب منفی یا کاتد) را دارند. قطب مخالف که کمبود الکترون دارد قطب مثبت یا آند نامیده میشود.
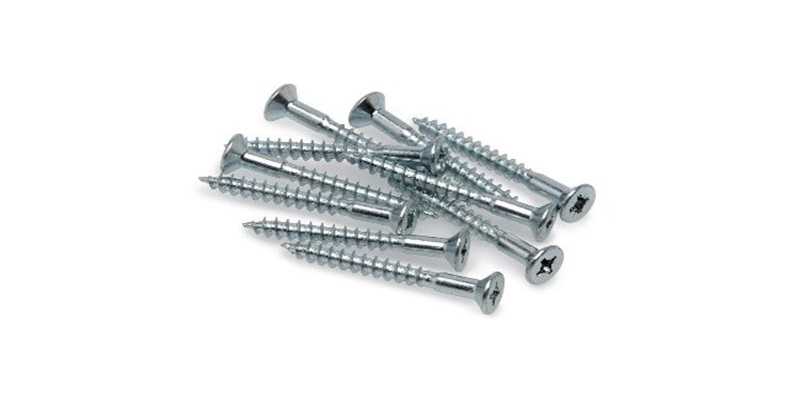
به طور کلی سیکل معمول پوششدهی را میتوان به صورت زیر در نظر گرفت:
- یک اتم در آند یک یا چند الکترون از دست میدهد و در محلول پوششدهی به صورت یون مثبت در میآید.
- یون مثبت به طرف کاتد یعنی محل تجمع الکترونها جذب شده و در جهت آن حرکت میکند.
- ین یون الکترونهای از دست داده را در کاتد به دست آورده و پس از تبدیل به اتم به صورت جزیی از فلز رسوب میکند.
- نیکل کروم: (نیکل سفید شبیه به نقره متمایل به زرد / کروم سفید شبیه به نقره متمایل به آبی) در این روش ابتدا نمونه با نیکل آبدهی می شود (نیکل رسانا بوده خاصیت مغناطیسی دارد, زنگ نمی زند و جوش می پذیرد) بعد از آن با کروم به منظور ایجاد سطحی صیقلی, خوب و مقاوم در برابر خوردگی ایجاد میشود (کروم زنگ نمیزند، جوش و نقاشی نمیپذیرد و در برابر اسید های هالوژن دار تاثیر میپذیرد اما در برابر گازها ,محلول های قلیایی و نمکی مقاوم است).
- تفلن (P.T.F.E): پوشش P.T.F.T در رنگ های مختلف مانند سبز, آبی, زرد ,مشکی, توسی و …… می باشد. این پوشش در برابر خوردگی و سایش مقاومت دارد. این پوشش توانایی تحمل دمای ۲۰۰ تا ۳۵۰ C رادارد.ضمنا پوشش تفلن عایق الکتریکی و ضد آب بوده و در برابر اسید, باز و نمک ایستایی دارد. گروه دیگری از پوشش ها هستند که مورد استفاده در صنایع قید و بستی است و از توضیح آن پرهیز مینماییم. مانند پوشش طلا , نقره , پلاتین و …
تولید رزوه: با ۲ روش می توان رزوه ها را تولید نمود:
- 1. ماشینکاری (حدیده): در این روش توسط تراشکاری رزوه هایی را بر روی میلگرد ایجاد میکنیم. قطر خارجی رزوه های تولید شده به این روش برابر با قطر ساق پیچ است.
- 2. نورد (رولینگ) (مالشی): در این روش بجای تراش و حذف قسمتهایی از میلگرد اولیه، توسط فرآیند اکستروژن رزوه ها را ایجاد میکنیم.
همچنین، در صورت نیاز به قیمت روز میلگرد آجدار و ساده تمامی کارخانهها میتوانید به بخش قیمت میلگرد امروز وبسایت آهنآنلاین مراجعه فرموده و خرید نمایید.
مقطع پیچ قبل از رزوه شدن دارای ۲ قطر متفاوت می باشد، قسمتی که قرار است رزوه شود دارای قطری کمتر بوده که پس از رزوه بواسطه انبساط شعاعی و دارای قطری برابر ساق (Shank) میشود. ضعیف ترین منطقه رزوه نسبت به نیروهای مکانیکی قطر کوچک (Minor) است و چون این مقدار در هر دو روش تولید برابر است بنابراین، از لحاظ مقاومت یکسانند، از طرفی کار سرد بر روی آلیاژ پیچ در روش نورد موجب افزایش فشردگی و استحکام رزوه ها میشود.
در این روش بعد از عملیات رزوه زنی، پیچهای با گرید ۸٫۸ و بالاتر جهت افزایش استحکام و سختی مورد عملیات حرارتی سختکاری (۷۰۰-۹۰۰) قرار گرفته آستنیتی می شود (۱۰ دقیقه بهازای هر۱۰ میلیمتر ضخامت)، سپس در روغن کوئنچ شده و پس از آن جهت بازگشت خواص ضربه پذیری و جلوگیری از تردی در دمای ۴۰۰ تا ۶۰۰ تمپر میشود. هنگام عملیات حرارتی Quench-Tempering بهمنظور جلوگیری از کربوره شدن بیش از حد یا دکربوره شدن ، دمای کوره میبایست خنثی بوده و تحت کنترل باشد. عملیات حرارتی در کنار مواد اولیه و فرایند تولید از ارکان تولید پیچ و مهره محسوب میشود.