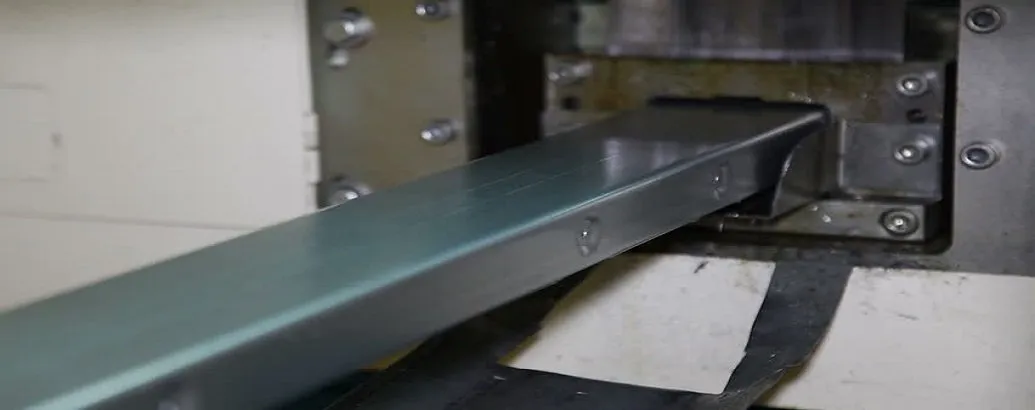
فرآیند تولید مستقیم و غیرمستقیم پروفیل
تولید پروفیل بهدلیل اینکه در ابعاد و اشکال مختلف صورت میگیرد در صنعت آهن آلات و ساخت و ساز یک محصول حائز اهمیت است. فرایند تولید پروفیل معمولا برای کاربریهای مختلف همچون قطعات ساختمانی، پنجرهها، دربها، و محصولات انجام می شود. همانطور که میدانید عملیات فوق اهمیت بالایی دارد زیرا مدیریت کیفیت و دقت در تولید پروفیل در عملکرد این مقطع فولادی مهم است.
پروفیل از جمله مقاطع فولادی است که در ساختمانسازی کاربرد بیشتری دارد و در انواع باز و بسته در بازار مورد استفاده قرار میگیرد. قوطیها اسکلتبندی بسیاری از سازهها مانند در و پنجره را تشکیل میدهند، به همین خاطر قیمت پروفیل تاثیر زیادی بر هزینه تمام شده برخی از سازهها دارد. فرآیند تولید پروفیل به دو روش مستقیم و غیر مستقیم تقسیم میشود. در این مقاله قصد داریم در مورد فرآیند و روشهای تولید پروفیل بحث کنیم.
پروفیل فولادی به دو روش مستقیم و غیرمستقیم تولید میشود که روش غیرمستقیم نسبت به مستقیم، در خط جوش، انحنای سطحی و اندازه اضلاع دقت پایینتری دارد.
فرآیند تولید پروفیل چگونه است؟
پروفیلها به طور کلی در دو نوع صنعتی و ساختمانی قرار دارند. نوع ساختمانی که در اینجا مورد بحث ما هستند، در دو گروه باز و بسته قرار دارند که از لحاظ فرآیند ساخت به دو شیوه نورد سرد و نورد گرم تولید میشوند.
به طور کلی نوعی از ساخت قوطی فولادی، نورد گرم است. در این روش پروفیل با استفاده از شمش داغ فولادی ساخته میشود. در مواردی که پروفیل در سازه شکل جدیتری در ایمنی بنا دارد، از این نوع استفاده میکنند. مدل دیگر، ساخت پروفیل با نورد سرد است. در این روش معمولا ورقها را میآورند و با استفاده از دستگاههای فرمدهی مانند پرس، تغییرات ایجاد میکنند. معمولا محصولات این روش را در سازههای سبکتر استفاده میکنند. زیرا واقعیت این است که پروفیلهای ساخته شده توسط نورد گرم بسیار مقاومت بیشتری دارند. دو نوع دیگر بدون درز جوش و با جوش است.
در بدون درز جوش، ورق را باز میکنند و روی هم میگذارند تا ضخامت پیدا کند. سپس با دستگاه مخصوص ERW بدون جوش پروفیل را میسازند. در روش با جوش، با حرارت برق، ورقها به هم جوش میخورند و پروفیل را تشکیل میدهند.
- نوع باز: نبشی، ناودانی و تیرآهن
- نوع بسته: پروفیلهای قوطی
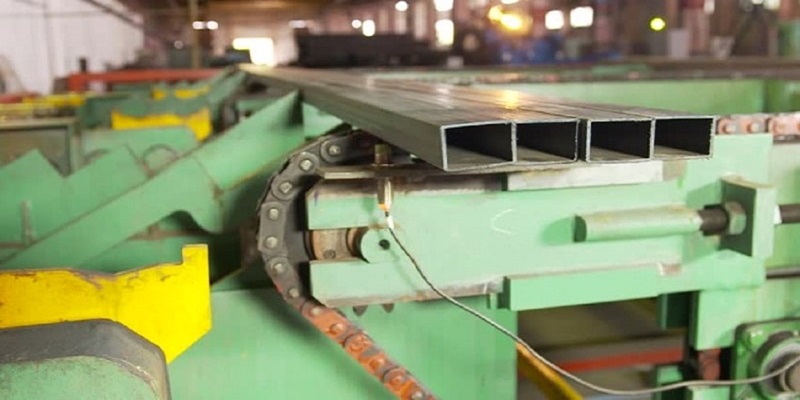
ماده اولیه برای تولید این محصول که تأثیر زیادی بر روی قیمت پروفیل، ورق تولید شده توسط کارخانههای فولاد است. این ورقها در گذشته توسط واردات از کشورهای آسیای میانه تأمین میشد؛ اما در حال حاضر کارخانههای فولاد مبارکه، گیلان و اهواز توان تولید این ورقها را دارند.
ورق به کار رفته در فرآیند تولید پروفیل باید دارای خصوصیات مکانیکی خاصی باشد؛ به طور مثال ورق ST37 استانداردهای کافی برای تولید پروفیل را دارا است. البته در نظر داشته باشید ورقها به صورت کلاف در بازار عرضه میشوند و در ابتدای فرآیند تولید پروفیل باید از دستگاههای برش نیمه اتوماتیک و اتوماتیک برای آماده کردن آنها استفاده کرد.
در اکثر کارخانههای تولیدکننده پروفیل، ورق فولادی را از طریق نورد سرد به شکلها و ابعاد متفاوتی در میآورند تا محصول نهایی حاصل گردد (برای مثال نوع باز و بسته به همین شیوه تهیه میشوند) این فرآیند شامل مراحل زیر است:
1. مواد اولیه
همانطور که گفته شد، در ایران پیش از تاسیس کارخانه فولاد مبارکه، مواد اولیه از کشورهای اروپایی و همچنین ژاپن تامین میگردید. اکنون بخش عمدهای از مواد اولیه تولید مقاطع فولادی همچون پروفیل از کارخانه فولاد مبارکه تهیه میشود و مقداری نیز از کشورهای آسیای میانه، برزیل، اروپا و اروپای شرقی وارد میشود.
ماده اولیه مصرفی که ورق است باید دارای ویژگیهایی باشد، از جمله ترکیبات شیمایی خاص و خواص مکانیکی مناسب (این ویژگیها باید مد نظر قرار داده شوند تا در زمان تولید پروفیل برای سازنده و در نهایت برای مصرف کننده مشکلی پیش نیاید). از جمله ورقهایی که این ساختار را دارند میتوان به ورق با استانداردهای، ST37، JIS G 3131 و G 3132 اشاره کرد که دارای ترکیبات شیمیایی خاصی (سیلیس ۰/۳۵، کربن ۰/۳ تا ۰/۱، گوگرد ۰/۰۴، فسفر ۰/۰۴ و منگنز ۰/۵) است.
2. برش کلاف به نوار
مرحله دوم تولید پروفیل ورقهای خریداری شده که به صورت کلاف است، به نوارهایی با عرض مشخص به کمک دستگاه برش بریده میشوند. دستگاههای برش به دو صورت تمام اتوماتیک و نیمهاتوماتیک موجود هستند که بسته به نیاز مورد استفاده قرار میگیرند و دارای بخشهای مختلفی هستند.
کلافهای ورق روی کلافگیر قرار میگیرد (کلافگیر حرکت چرخشی دارد)، کلافگیر میچرخد تا سر ورقها در زیر غلتکهای صافکننده قرار گیرد؛ با انجام این عملیات ورقها صاف و تخت میگردند. به وسیله دستگاه گیوتین سر ورقها برای جوشکاری در مرحله بعد برش داده میشود.
ورقها به کمک غلتکهای تغذیه به سمت دو شافت اصلی (که دارای محرک است و روی این محرکها تیغههایی از جنس فولاد با سختی بین ۵۹ تا ۶۱ راکول دارند) حرکت میکنند، حال ورق از بین دو تیغه عبور میکند و عملیات برش صورت میگیرد.
برای حرکت دقیق ورقها به سمت جلو از دو عدد شافت جداکننده که روی آنها تیغههای کوچکی قرار گرفته است، استفاده میکنند. نوارهای تولیدی در این مرحله دستهبندی میشوند و به خطوط تولیدی مختلف انتقال مییابند.
در مرحله نهایی، نوارهای برشخورده بهوسیله شافتهای جداکننده که دارای تیغههای کوچک برای هدایت دقیق هستند، به گیرهای مخصوص در داخل دستگاه نوارجمعکن متصل میشوند. این دستگاه وظیفه دارد با کشیدن ورقها، آنها را بهصورت مرتب و منظم جمعآوری کند. در پایان این فرآیند، نوارهای آمادهشده بر اساس ابعاد و مشخصات موردنیاز، دستهبندی شده و برای مراحل بعدی تولید به بخشهای مختلف کارخانه ارسال میشوند. دقت بالا در این مرحله نهتنها بر کیفیت نهایی محصول اثرگذار است، بلکه موجب بهینهسازی زمان و کاهش هزینههای تولید نیز میشود.
قسمتهای مختلف دستگاه برش
از بخشهای مختلف یک دستگاه برش میتوان به موارد زیر اشاره کرد:
- ذخیره کلاف
- ضربهگیر
- کلافگیر
- سیستم کنترل کننده کناره به منظور تنظیم بهتر
- میز حمل کننده
- غلتکهای تغذیه ورق
- صاف کننده ورق
- قرقرههای هدایت ورق
- نگهدارنده نوارها
- غلتکهای جدا کننده نوارهای بریده شده
- نوار جمع کن
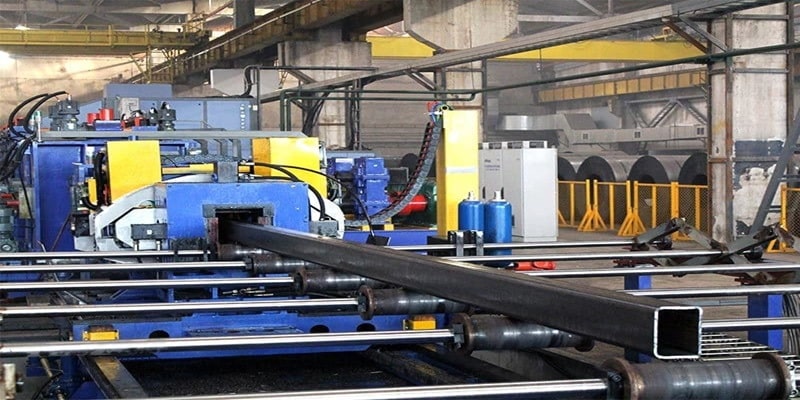
فرآیند تولید مستقیم پروفیل
در روش تولید مستقیم پروفیل ابتدا با خم کردن ورق شکل زوایای مورد نظر برای پروفیل را ایجاد میکنند و سپس با کمک جوشهای فرکانسی دو به دو، لبههای ورق را به یکدیگر جوش میدهند تا مقطع مورد نظر شکل بگیرد. سپس آن را با کمک اره اتوماتیک محصول برش داده میشود و به مرحله بستهبندی ارسال خواهد شد؛ البته قبل از انتقال محصولات به انبار، کارت مشخصات و تاییدیه کنترل کیفی بر روی آنها نصب میگردد. شما میتوانید برای آشنایی بیشتر با پروفیل به مقاله پروفیل چیست و انواع آن مراجعه کنید.
استانداردهای تولید پروفیل
رعایت استانداردهای کیفی در تولید پروفیل بسیار مهم است. استانداردها نقش مهمی در تضمین کیفیت و اثربخشی پروفیل ها دارند، استانداردهایی که در زیر قرار دارد مشخصات و ویژگی های مورد نیاز برای پروفیل ها را تعریف می کنند:
- استانداردهای ASTM در ایالات متحده
- استانداردهای EN در اروپا
مزایای تولید مستقیم پروفیل
- تیز بودن زوایهها
- دقیق بودن ابعاد
- ثابت بودن خط جوش
- کم بودن انحنای سطحی
- کیفیت بالا نسبت به سایر روشها
معایب تولید مستقیم پروفیل
- افزایش استهلاک قالبها (به دلیل تفاوت در سرعت خطی، متفاوت بودن قطر در قسمتهای مختلف قالب)
- نیاز به دقت بالا به منظور ماشینکاری و عملیاتهای حرارتی
- متفاوت بودن قطر پروفیل تولیدی در قسمتهای مختلف
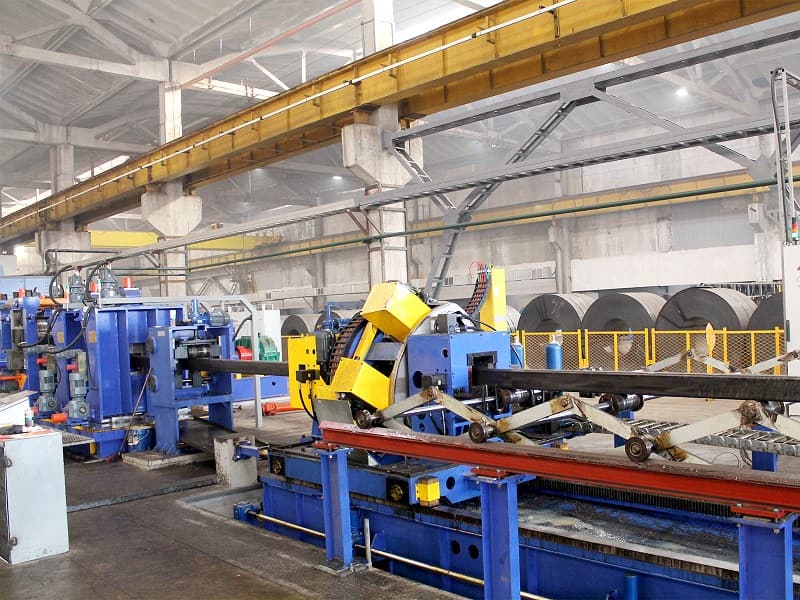
فرآیند تولید غیرمستقیم پروفیل
در تولید غیرمستقیم قوطی، نوار به یکی از سه روش شکلدهی لبهای، شکلدهی مرکزی و شکلدهی از طریق شعاع ورق به لوله تبدیل میشود. سپس به شکل مد نظر درمیآید.
این روش On Line نام دارد. در این روش با تولید یک لوله با عوض کردن چندین قالب در قسمت سایزینگ میتوانیم چندین نوع پروفیل تولید کنیم. این روش نسبت به روش تولید مستقیم پروفیل در خط جوش، انحنای سطحی و اندازه اضلاع دقت پایینتری دارد.
زمینههای کاربردی ساخت پروفیل فولادی
میدانیم پروفیل فولادی در انواع مختلف صنعتی و ساختمانی به دو صورت باز و بسته تولید میشود و اجناس مختلفی دارد و در این مقاله در زمینه فرآیند تولید مستقیم و غیرمستقیم پروفیل فولادی و مزایا و معایب هر کدام صحبت کردیم. بسته به نوع و کیفیت تولید، جنس پروفیل و ابعاد سفارشی، قیمت این کالای صنعتی تعیین میشود و هدف ما از این مقاله و مقالات دیگر مرتبط، شفافسازی عوامل موثر بر این قضیه است؛ اگر راستای تولید انواع پروفیل اطلاعات یا تجاربی فرای این مقاله دارید، لطفا با ما به اشتراک بگذارید.